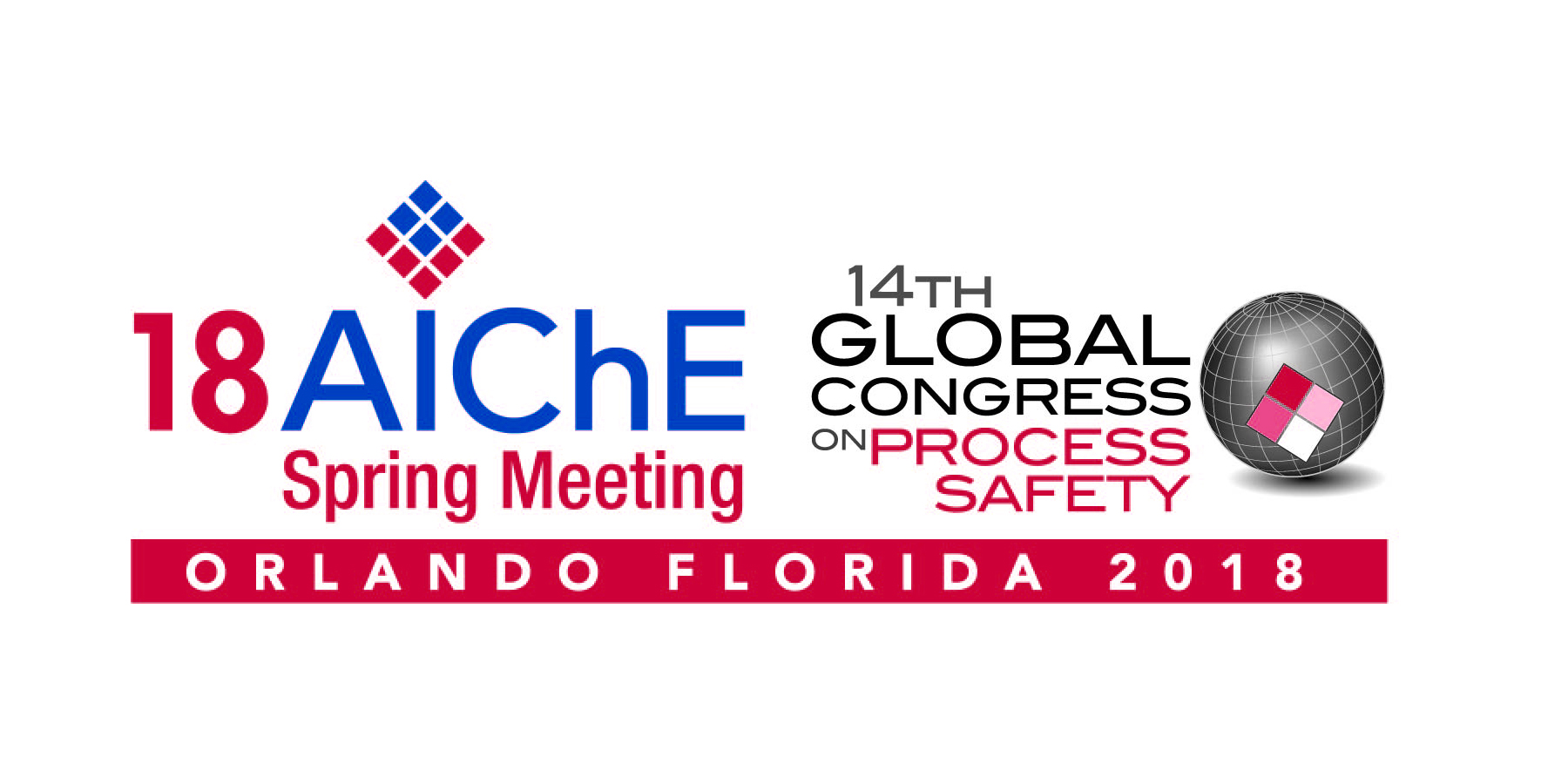
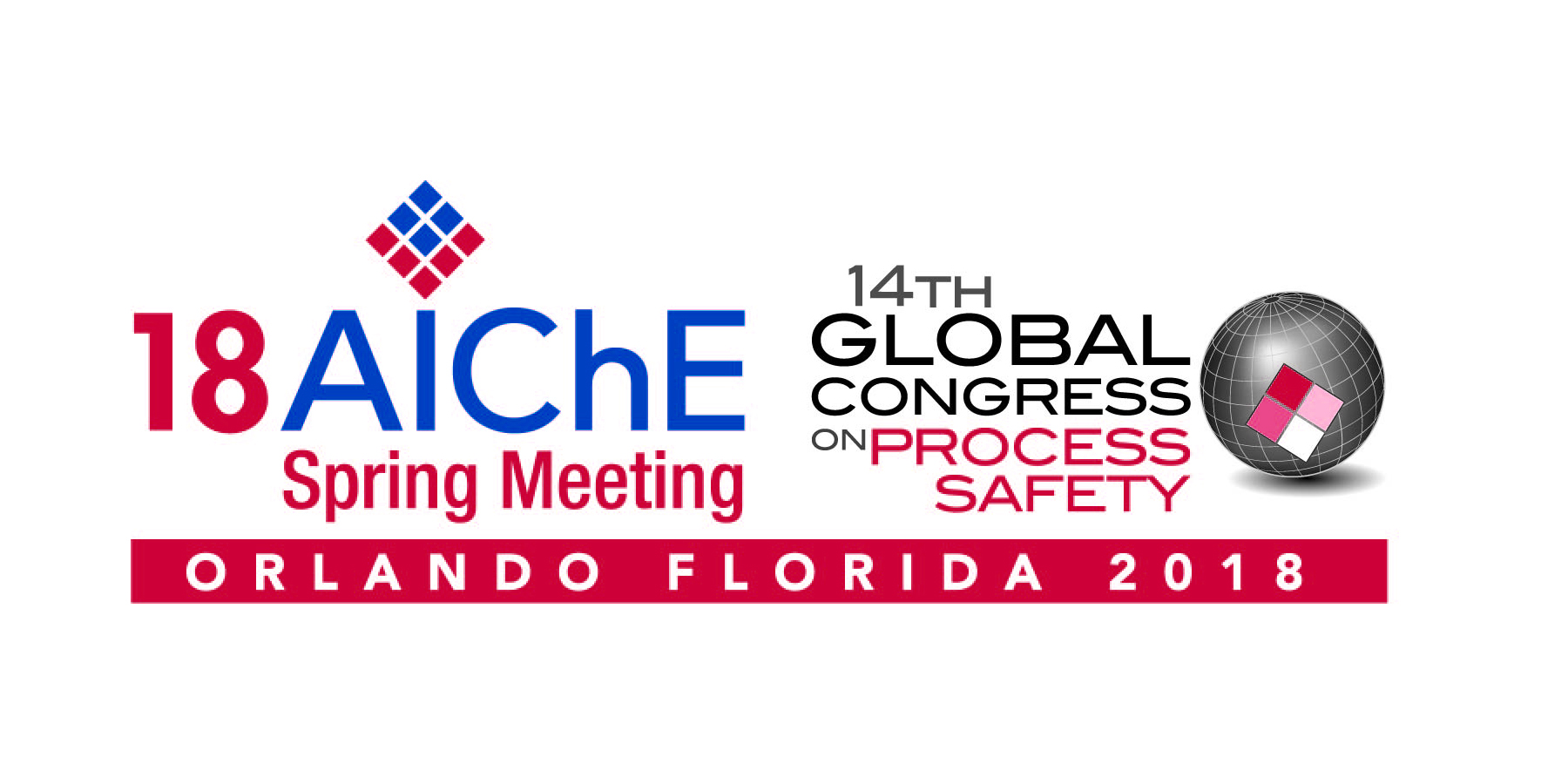
Selecting the Proper Gas
Compressibility Z for Relief Valve Sizing
Freeman Self (feself@bechtel.com)
Satyajit Verma (sverma4@bechtel.com)
Bechtel Oil, Gas and Chemicals, Inc.
Prepared for
presentation at the
American
Institute of Chemical Engineers Spring Meeting
14th
Global Congress on Process Safety
Orlando, Florida
April 2018
Process Safety Spotlights(T1F) - Chair and Contact: Wayne Chastain
- T1F00 Pressure
Relief Design - Oral Session -
Abstract
Introduction
Gas flow sizing
of relief valves is commonly performed using the analytical gas formula for
choked flow. The gas compressibility is
an important parameter. The proper
selection of the value of Z will avoid possible over-sizing or under-sizing a
relief valve.
This paper
will explain when one should use the ideal gas compressibility Z (equal to 1.0)
or when to use the actual Z (at temperature and pressure) when sizing a relief
valve using the analytical gas choked flow formula.
Overview
Sizing of
relief valves in gas flow is commonly performed using the analytical gas
formula for choked flow. The common form
used in vendor catalogues and API Standard 520-I Sizing, Selection and
Installation of Pressure-Relieving Devices is:
W = A Kd C P Ö
( M / T Z ) (1)
Rearranging
using the formula for density results in:
W = A Kd C Ö
( P r )
(2)
W
is mass flow [lb/hr], A is orifice area [in2], Kd is discharge coefficient, P
is inlet pressure [psia], M is molecular weight [lb/mole], T is Rankin
temperature [°R], C is coefficient
containing only the parameter K ideal gas heat capacity ratio (K = Cp / (Cp
R)), C is the same coefficient with revised conversion factors, r
is density [lb/cf] and Z is the gas compressibility
Although deceptively simple, the
assumptions inherent in the derivation may result in drastically oversized or
undersized relief valves. Yet, there
has been little elucidation of the issues.
The results may be surprising since there are no clear resolution for
certain situations.
To explain the problem, it is necessary
to understand two of the major assumptions utilized in the derivation of the
choked flow equation. (The derivation is
quite complex but may be found in advanced transport books.)
· Gas is ideal, which
means the compressibility Z is equal to 1.0 and the ratio of heat capacities is
constant
· The density (as a
function of pressure) is determined using a specific correlation called the
isentropic expansion expression. This expression states that the density at
the throat pressure, as the backpressure on the relief valve is reduced, may be
calculated from the previous pressure and density, ideal gas heat capacity ratio
K and utilizing a constant entropy process.
(The subscripts 1 and 2 are used for any two pressures along an
isentropic path.)
P / rK = constant (3) or stated equivalently:
P1 / r1K = P2 / r2K (4) where K is the ideal gas heat capacity ratio
K = Cp / (Cp R)
The
Conundrum of Density
The analytical gas formula for choked
flow - equation (2) - shows that the flow rate at choked condition through the
relief valve is a function of density. When
sizing the relief valve using the typical equation (1), the density at the
initial pressure is established by the compressibility. If the gas is close to
ideal, the ideal and actual densities will be comparable in value.
The densities at other pressures are
implicitly represented by the isentropic expansion expression equation (3 or
4) which is used in the derivation of equation (1 or 2). The density pressure relationship can be
demonstrated by calculating the densities utilizing the isentropic expansion
expression equation (3 or 4). In general, they are almost a linear function of
pressure since K is close to the value of one.
In contrast, the actual densities frequently do not usually exhibit a
linear relationship with pressure. Consequently
the densities from the isentropic expansion expression may not track the
actual densities.
Therefore accuracy of the choked gas flow
rate calculation depends both on:
· the initial value of
the compressibility,
· how well the actual densities
track the densities represented by the isentropic expansion expression.
Two examples will illustrate the
differences in results, and how they are affected by the densities. The graph plots the fluids density and pressure
at the relief valve orifice as the backpressure on the relief valve is reduced
from the initial pressure to a lower pressure. Three densities are plotted: 1. the actual
density (from a process simulator), 2. the density calculated from the
isentropic expansion expression equation (3) with the initial ideal gas
density (Z=1.0), and 3. the density calculated from the isentropic expansion
expression with the initial actual density.
· Example 1 provides an
illustration of the situation where the ideal gas compressibility provides an
acceptable sized relief valve. Although the initial ideal gas density is higher
than that calculated with the actual Z, the ideal gas density curve coincides
better with the actual densities.
· Example 2 illustrates
the opposite situation where the actual gas compressibility provides an
acceptable sized relief valve. Using the
ideal gas compressibility produces higher flowrates and an oversized relief
valve.
Additional examples will be provided in
the presentation that will provide guidance on proper selection of the gas
compressibility factor.
Conclusions
The homogenous direct numerical
integration method (HDI) will provide the best answer in all cases. (The HDI method is provided in API Standard
520-I Sizing, Selection and Installation of Pressure-relieving Devices.) However analytical gas equation is commonly
employed to size relief valves in gas service.
The proper selection of the value of Z when using the analytical
equation will avoid possible over-sizing or under-sizing a relief valve in gas
service.
Presenter(s)
Language
Pricing
Individuals
AIChE Member Credits | 0.5 |
AIChE Pro Members | $19.00 |
Employees of CCPS Member Companies | Free |
AIChE Graduate Student Members | Free |
AIChE Undergraduate Student Members | Free |
AIChE Explorer Members | $29.00 |
Non-Members | $29.00 |