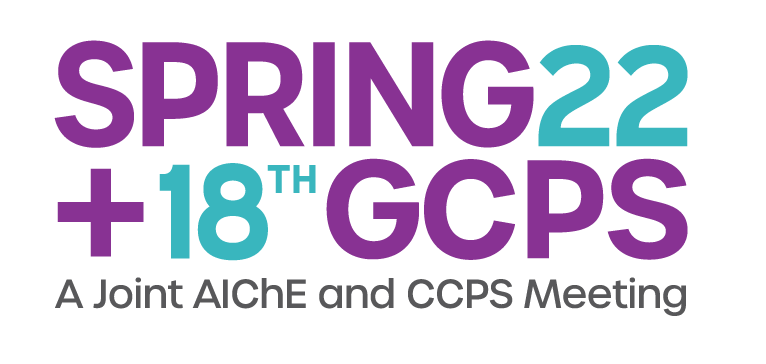
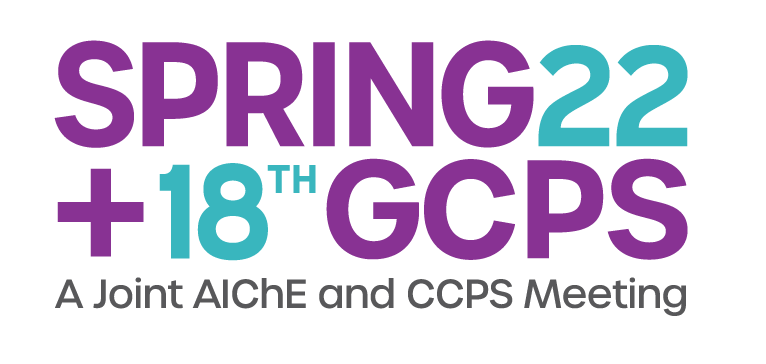
The rigorous application of continuous improvement to Process Safety Management (PSM) programs to a facility or operation results in: continuity of operations; improved operability; enhanced product quality; contractor and worker safety, technical documentation configuration control and sound management of change, thorough and effective incident investigation and loss reduction through evaluation of near misses, integrated shared Safety Culture and many more tangible safety and cost saving aspects of a personal commitment to PSM.
The strategic implementation of lessons learned story telling through almost all of the elements of PSM to engage employees and management to personally commit to and fully participate in the PSM Program. The Author has personally seen this as a means to: enhance Safety Culture, reduce incidents, personnel injuries and capture near misses; avoid loss of containment/chemical releases; minimize Product Quality Issues; Increase Reliability; implement consistent Management of Change (MOC) and PSI Configuration Control; develop specific and enhanced emergency action plans and emergency operating procedures (EOPs). The programs at many of my clients have all benefitted by use of related examples from the Company and related industry specific examples presented through training, Hazard Analysis sessions, MOC and Incident Brainstorming activities.
The authors will discuss how the use of Storytelling via relevant lessons learned make the reasons for fully engaging in PSM clear to the company stakeholders from Plant Maintenance, Operations, Engineering, SHE personnel through Plant Management and Corporate Management. People understand story based communications and can attach a better sense of commitment when there is a clear image created that the efforts to complete the program elements are worth saving their own and fellow employees lives, health and protecting the plant from damage are linked to real results and real losses.
The authors will share case studies where PSM Programs they have implemented improved availability (continuity of operations), increased profitability and established integrated safety cultures at multiple facilities, operations and institutions through vital means of including relatable examples that put a clear picture of the effects and consequences to real people from real events. Example Stories include Union Carbide Corporate measures post-Bhopal; ICI Americas metrics from application of HAZOP; HF Plant loss of containment events and effects on surviving operators; Hot Work Permit signed by Plant Manager that killed two contractors welding on top of an âEmptyâ Pint tar Spirits Tank; Pres-Startup Safety Review when a Not-in-Kind Replacement Caused half of the newly constructed Greenfield Natural Gas Liquids (NGL) Plant to Burn.
Author will share how he learned from the First Generation of Process Safety Leaders at the outset of State (NJ-TCPA, DE-EHSRMA and CAL-OSHA) and Federal Programs (OSHA-PSM, EPA-RMP) implemented Post-Bhopal and how throughout his career he has used the specific examples of losses and incidents to amplify the message of why implementing PSM whole-heartedly is the key to saving lives, supporting and improving plant safety and improving operability and profitability through a fully integrated PSM Program and fully committed staff.
Presenter(s)
Language
Pricing
Individuals
AIChE Member Credits | 0.5 |
AIChE Pro Members | $19.00 |
Employees of CCPS Member Companies | Free |
AIChE Graduate Student Members | Free |
AIChE Undergraduate Student Members | Free |
AIChE Explorer Members | $29.00 |
Non-Members | $29.00 |