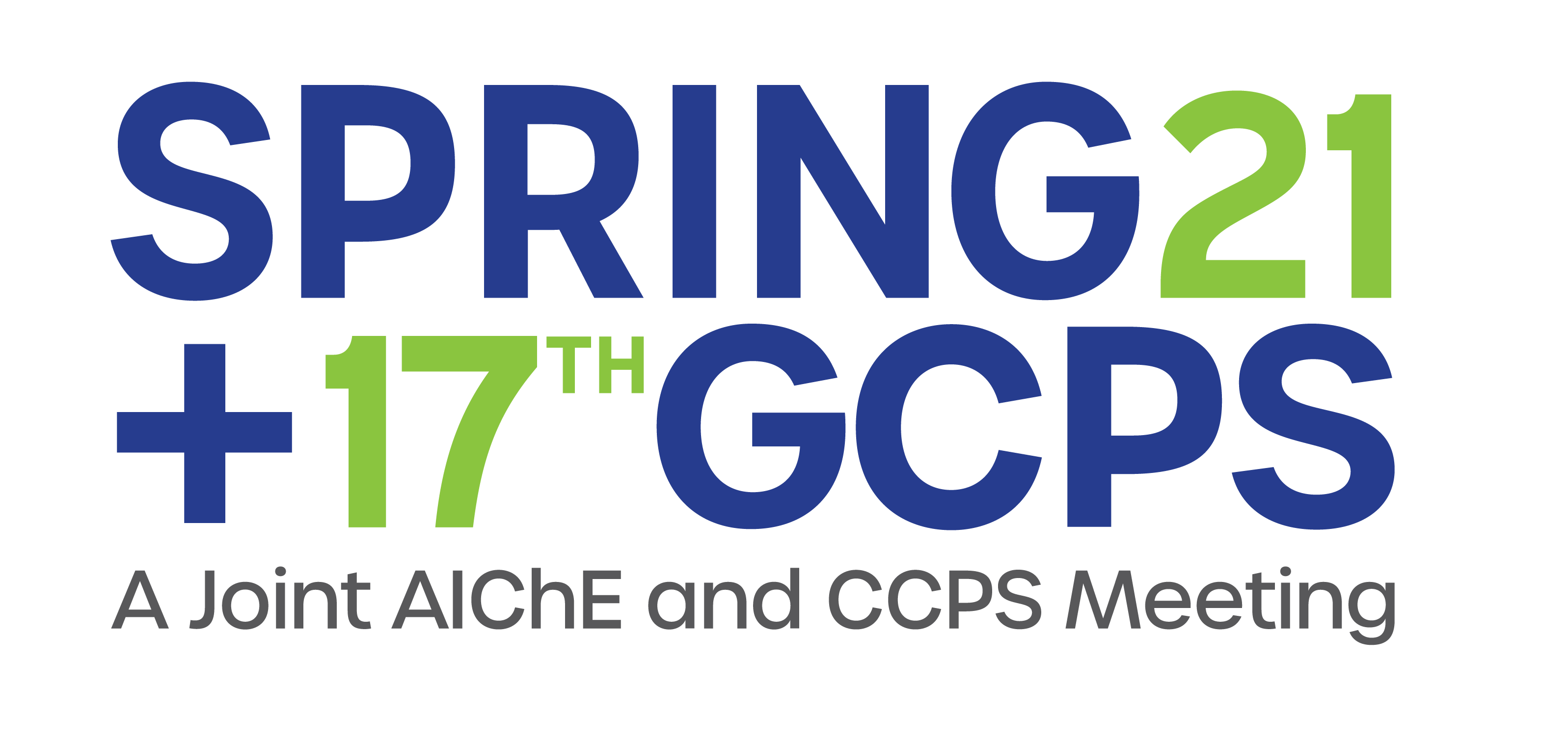
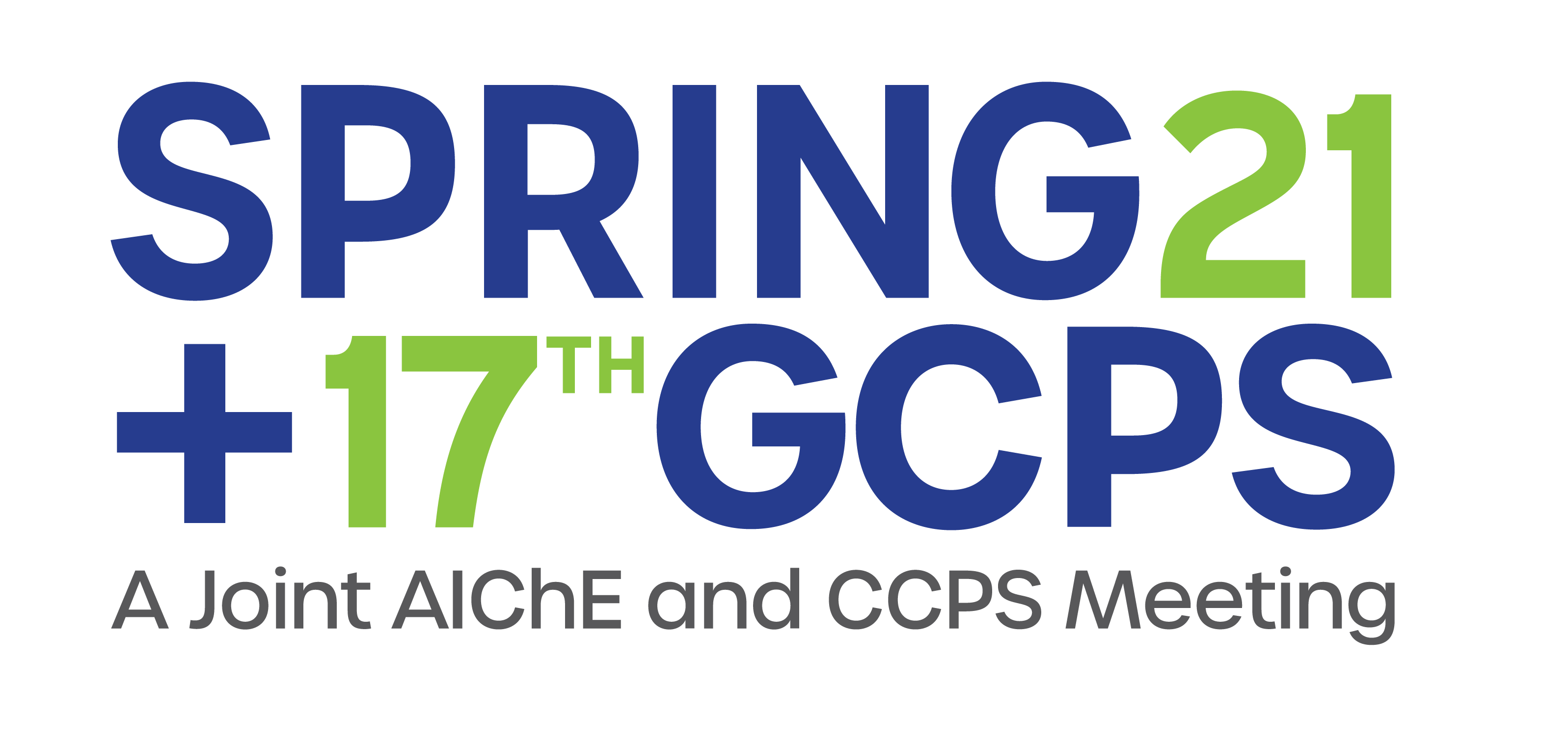
This work aims to implement a safety management system within a company currently responsible for the largest share of the bulk LPG market, considering the particularities of this type of operation, totally dependent on road transport for LPG distribution. To achieve this the first step was identifying the main activities that represent the bulk system's operation, involving bobtail trucks, as follows: supply through road routes; unloading, which is the supply to the customer and the operation of the bobtail truck itself.
The strategy of implementing the safety management system considered sequential application of the following steps: 1) Reassessment of the bobtail truck project, aligning it with the latest technological solutions; 2) Conducting a hazard identification study for supply and unloading activities, proposing a customized hazard identification model for supply; 3) barriers auditing to evaluate unloading components reliability; 4) Auditing operating activities based on CCPS RBPS in order to identify existing gaps. The fifth and final step is the definition of the Process Safety Management approach aligned with road transportation best practices worldwide and in compliance with legal and corporate requirements.
The studies already developed demonstrate that a careful analysis of the main normative reference identified gaps in the bobtail project, with emphasis on passive safety systems, absent in the original project. In the supply risk assessment stage (routes assessment), a specific model for route risk analysis was developed using a customized Excel spreadsheet for risk analysis through predefined menus. This model reduced the assessment time required and the level of subjectivity, allowing the company to develop hundreds of analyzes with the use of video conferencing tools, essential in this case, due to its nationwide scope.
This is a work in progress and the next steps, when completed, will make the company achieve a degree of excellence in Process Safety Management through monitoring for the implementation of all RBPS elements that have been identified as absent or deficient. Many other industrial sectors that carry out transport of dangerous products can benefit from this methodology for implementing RBPS, through the use of the described models, adapting them to the specific modal.