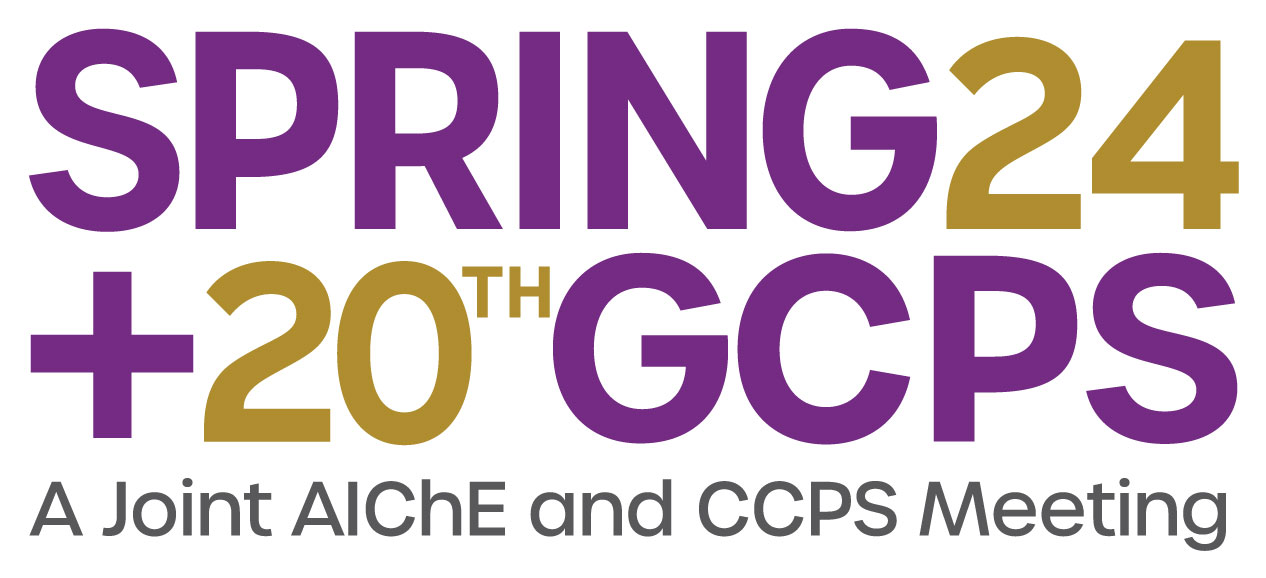
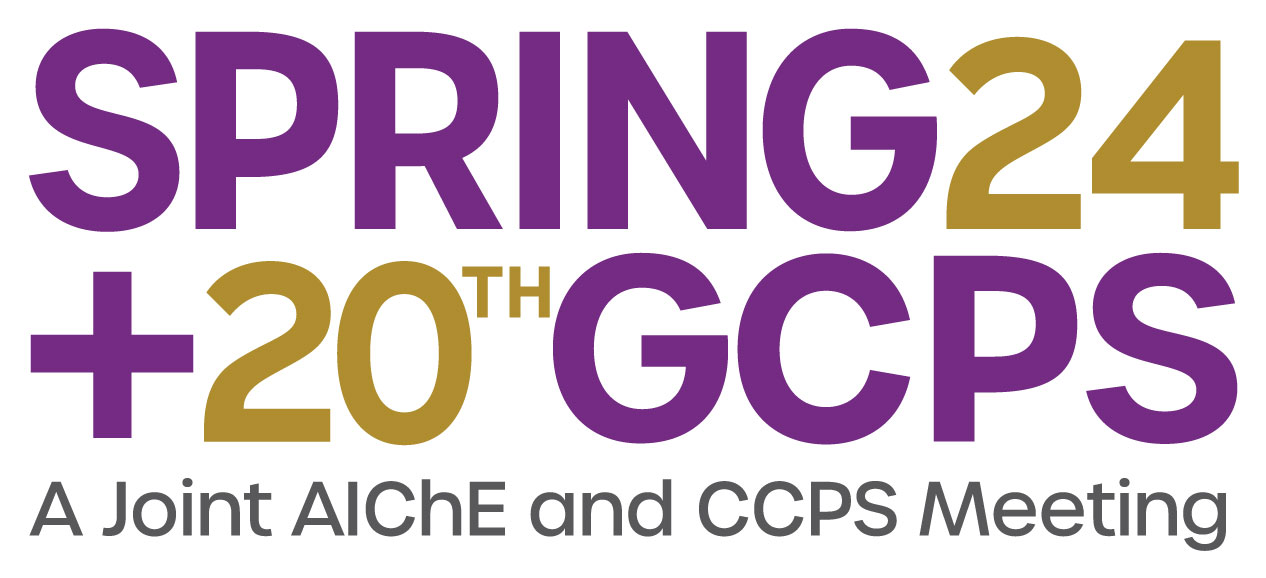
The increasing production and improper disposal of plastic waste have led to a growing environmental crisis, prompting earnest efforts towards efficient recycling. Polyolefins, such as polypropylene (PP), polyethylene (PE), and polystyrene (PS), constitute a significant portion of plastic waste found in municipal solid waste [1]. Recycling polyolefins is crucial for achieving sustainability goals in the chemical industry and promoting a circular economy. Traditional disposal methods, including landfilling and incineration, are environmentally detrimental, causing pollution, greenhouse gas emissions, and the generation of nano-plastics. Therefore, chemical recycling approaches such as pyrolysis have attracted attention in recent years due to their potential to thermochemically convert plastic waste into valuable products and allow operational flexibility in large-scale processes [1].
Pyrolysis enables the thermal decomposition of polyolefins into low-value oils. Steam-cracking plants can utilize these oils, provided the pyrolysis oil or a blend of naphtha/pyrolysis oil meets the industry standards regarding composition and stringent contaminant [2]. However, pyrolysis demands high temperatures and substantial energy consumption, limiting its broader applicability [3]. The introduction of a catalyst to the thermal pyrolysis process helps to reduce the energy demand and enhances selectivity for valuable products, such as light olefins (C2-C4 olefins). Light olefins are sought-after platform chemicals given their significance as building blocks for various plastic products and chemicals [4] . High light olefin selectivity can be achieved either via ex-situ upgrading of the thermal pyrolysis volatiles in a close-coupled second reactor, or in-situ by mixing the catalyst with plastic waste directly and feeding it to a thermo-catalytic pyrolysis reactor. Ex-situ catalytic pyrolysis offers a substantial benefit over in-situ catalytic pyrolysis considering the presence of non-volatile contaminants in the plastic waste. The first step thermal pyrolysis prevents the direct contact of a portion of contaminates with the catalyst, thereby partially preserving the catalyst active sites. However, hazardous contaminants in the plastic waste, such as PVC, still pose a significant threat to ex-situ catalytic pyrolysis. PVC pyrolysis leads to the formation of highly corrosive and poisonous HCl gas, which severely and irreversibly deactivates the catalyst by causing dealumination, rupturing the catalyst framework [5, 6]. For instance, PP waste recycling rate is limited by its varying compositions and contamination levels [7].
Creating a robust catalyst that can selectively crack different types of polyolefins to light olefins while preserving its stability against hazardous contaminants is crucial. Thus, HZSM-5 is modified in this work to improve its stability while facilitating the diffusion of bulky and branched polypropylene pyrolysis vapors into catalyst pores, where active sites are mostly located.
The HZSM-5 catalysts were desilicated with NaOH and impregnated with phosphorous prior to severe steaming at 800 °C, where detailed synthesis can be found elsewhere [8]. The pyrolysis experiments were conducted by using a single-shot tandem micro-pyrolysis facility (Rx-3050TR, Frontier Labs, Japan) combined with comprehensive two-dimensional gas chromatography employing a flame ionization detector and time-of-flight mass spectrometer (GCxGC-FID/TOF-MS) to quantify and identify the complex pyrograms accurately. The pyrolysis reactor was maintained at 550 °C and loaded with grounded PP, deliberately contaminated with PVC (5 wt.%). He was used as the carrier gas to purge volatiles into the second reactor loaded with a fixed catalytic bed at 600 °C. A detailed description of the experimental unit and details about the method used for product quantification can be found in our previous study [4].
Polypropylene was effectively converted into light olefins with high selectivity using parent, phosphorus-modified, and mesoporous phosphorus-modified HZSM-5 catalysts. The integration of a second close-coupled catalytic reactor to the pyrolysis unit substantially increased the light olefin selectivity from ~25 wt.% to 74-84 wt.%. Phosphorus and mesopore modification followed by severe steaming at 800 °C significantly reduced catalyst acidity from 0.65 NH3 mmol/g to 0.10 NH3 mmol/g. The reduced acidity of the modified catalysts have led to ~5 wt.% lower light olefin yields for a single run compared to unmodified ZSM-5. However, during 150 consecutive experimental runs, the parent HZSM-5 exhibited the most rapid and severe deactivation, with its light olefin selectivity decreasing from 79 wt.% to 44 wt.%. In contrast, the phosphorus-modified catalyst maintained a relatively higher selectivity at 57 wt.%. Notably, the mesopore-introduced phosphorus-modified catalysts achieved the highest light olefin selectivity after 150 experimental runs (63 wt.%). The presence of mesopores , in principle, reduces the residence time of light olefins inside the catalyst pores which possibly delays deactivation by coke. Then, pyrolysis temperature and catalyst-vapor contact time were optimized to maximize light olefin selectivity for parent HZSM-5 and the best performing catalyst: phosphorous modified mesoporous HZSM-5. Increasing the catalyst-vapor contact time to 117 ms at a pyrolysis temperature of 550 °C resulted in the highest light olefin selectivity obtained so far in reported literature, up to 84 wt.%, even surpassing the maximum achieved olefin selectivity with parent catalyst over a single run.
Catalyst deactivation due to coke formation during pure PP pyrolysis vapor cracking was reversible, as all the catalysts were successfully regenerated. Pyrolysis of PVC-contaminated PP led to faster deactivation for all catalysts, with light olefin selectivity dropping below ~65 wt.% after 50 runs. However, the modified catalysts were effectively regenerated after waste PP pyrolysis for 50 run, whereas the parent HZSM-5 was permanently deactivated. This could be attributed to phosphorus modification preventing dislodged alumina from leaving the zeolite framework by interacting with Si and leached Al to form SAPO species, thereby preserving the framework [6]. Given that just a 5wt.% PVC contamination in the feed renders commercial HZSM-5 unusable, it is crucial to develop a robust catalyst to withstand impurities in plastic waste for recycling. Notably, phosphorus modification with mesopore introduction has demonstrated excellent stability improvements to overcome this problem.
References
- Eschenbacher, A., et al., Maximizing light olefins and aromatics as high value base chemicals via single step catalytic conversion of plastic waste. Chemical Engineering Journal, 2022. 428: p. 132087.
- Kusenberg, M., et al., A comprehensive experimental investigation of plastic waste pyrolysis oil quality and its dependence on the plastic waste composition. Fuel Processing Technology, 2022. 227.
- Abbas-Abadi, M.S., et al., Challenges and opportunities of light olefin production via thermal and catalytic pyrolysis of end-of-life polyolefins: Towards full recyclability. Progress in Energy and Combustion Science, 2023. 96.
- Akin, O., et al., Chemical recycling of plastic waste to monomers: Effect of catalyst contact time, acidity and pore size on olefin recovery in ex-situ catalytic pyrolysis of polyolefin waste. Journal of Analytical and Applied Pyrolysis, 2023. 172.
- Lewandowski, K. and K. Skorczewska, A Brief Review of Poly(Vinyl Chloride) (PVC) Recycling. Polymers, 2022. 14(15).
- Ibanez, M., et al., Simultaneous coking and dealumination of zeolite H-ZSM-5 during the transformation of chloromethane into olefins. Catalysis Science & Technology, 2016. 6(1): p. 296-306.
- Kulas, D.G., A. Zolghadr, and D. Shonnard, Micropyrolysis of Polyethylene and Polypropylene Prior to Bioconversion: The Effect of Reactor Temperature and Vapor Residence Time on Product Distribution. Acs Sustainable Chemistry & Engineering, 2021. 9(43): p. 14443-14450.
- Eschenbacher, A., et al., Highly selective conversion of mixed polyolefins to valuable base chemicals using phosphorus-modified and steam-treated mesoporous HZSM-5 zeolite with minimal carbon footprint. Applied Catalysis B-Environmental, 2022. 309.
Presenter(s)
Language
Pricing
Individuals
AIChE Member Credits | 0.5 |
AIChE Pro Members | $19.00 |
Fuels and Petrochemicals Division Members | Free |
AIChE Graduate Student Members | Free |
AIChE Undergraduate Student Members | Free |
AIChE Explorer Members | $29.00 |
Non-Members | $29.00 |