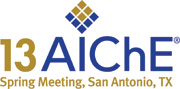
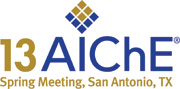
Thermal Fluids: the Key to Overall Site Integration
G.T.Polley, M.Picon Nunez & E.Tamakloe
Dept. of Chemical Engineering, University of Guanajuato, Mexico
Structure of Presentation
Need for efficient transfer of energy across separate geographical zone
Overall Factory Sites
Improvement of CDU Fired Heater Efficiency
Transfer of Energy Across Geographical Zones
A recent study of the energy efficiency of an FCC plant revealed a number of distillation column re-boilers positioned well below the heat recovery pinch but being driven by steam.
Examination of the plant structure (Figure 1) revealed the probable cause of this inefficiency, the piping costs associated with the use of direct integration would be very high and not justified by the energy saving achieved.
Figure 1. Plant Structure
Design of New Plant Using Process Decomposition Analysis
Full Problem: 36 MW 6.04 M$/annum
Column Region: 3.2 2.46
Gas Area: 74.1 7.53
Summation: 77.3 MW 9.99 M$/annum
Failure to transfer energy between the two zones results in over 100 % increase in energy consumption.
Inter-Zonal Transfers: Comparison of Grand Composite Curves
Analysis of inter-zonal transfers involves comparison of pinch locations in each of the zones and the Grand Composite Curves for each of the zones.
Column Region:
Gas Processing Area:
The temperature differences allow for indirect integration. This is a preferred option for it allows the plant zones to be independently operated and minimises that transport of process fluid across the plant.
Transfer limited by formation of second pinch.
By using oil operating between 245 and 120 C it is possible to transfer 39 MW between the two zones. The decomposition analysis is:
Full Problem: 36 MW 6.04 M$/annum DT = 10 C
Column Region: 4.9 2.10 24 C
Gas Area: 35.13 4.97 10 C
Summation: 40.03 MW 7.07 M$/annum
The transfer has resulted in a net energy saving of 37.3 MW. The process uses 4.03 MW more than the prediction for the overall problem.
A document providing full design solution is available from the authors.
Overall Factory Sites
?Site Composites? are built up by extracting the ?supply? and ?demand? elements of the Grand Composite Curves for the Individual Plants.
Capital costs dominated by piping costs.
The capital cost of piping varies with diameter raised to a power 3.
Size of pipe required to transport a liquid very much smaller than that required to transfer steam.
Use thermal fluid. DO NOT TRANSPORT STEAM.
Improvement of CDU Fired Heater Efficiency
Fouling rates in convective section of a fired heater are affected by the flow conditions on the crude side
If crude enters as a single phase liquid fouling rates are high
Presenter(s)
Language
Pricing
Individuals
AIChE Member Credits | 0.5 |
AIChE Pro Members | $15.00 |
Fuels and Petrochemicals Division Members | Free |
AIChE Graduate Student Members | Free |
AIChE Undergraduate Student Members | Free |
AIChE Explorer Members | $25.00 |
Non-Members | $25.00 |