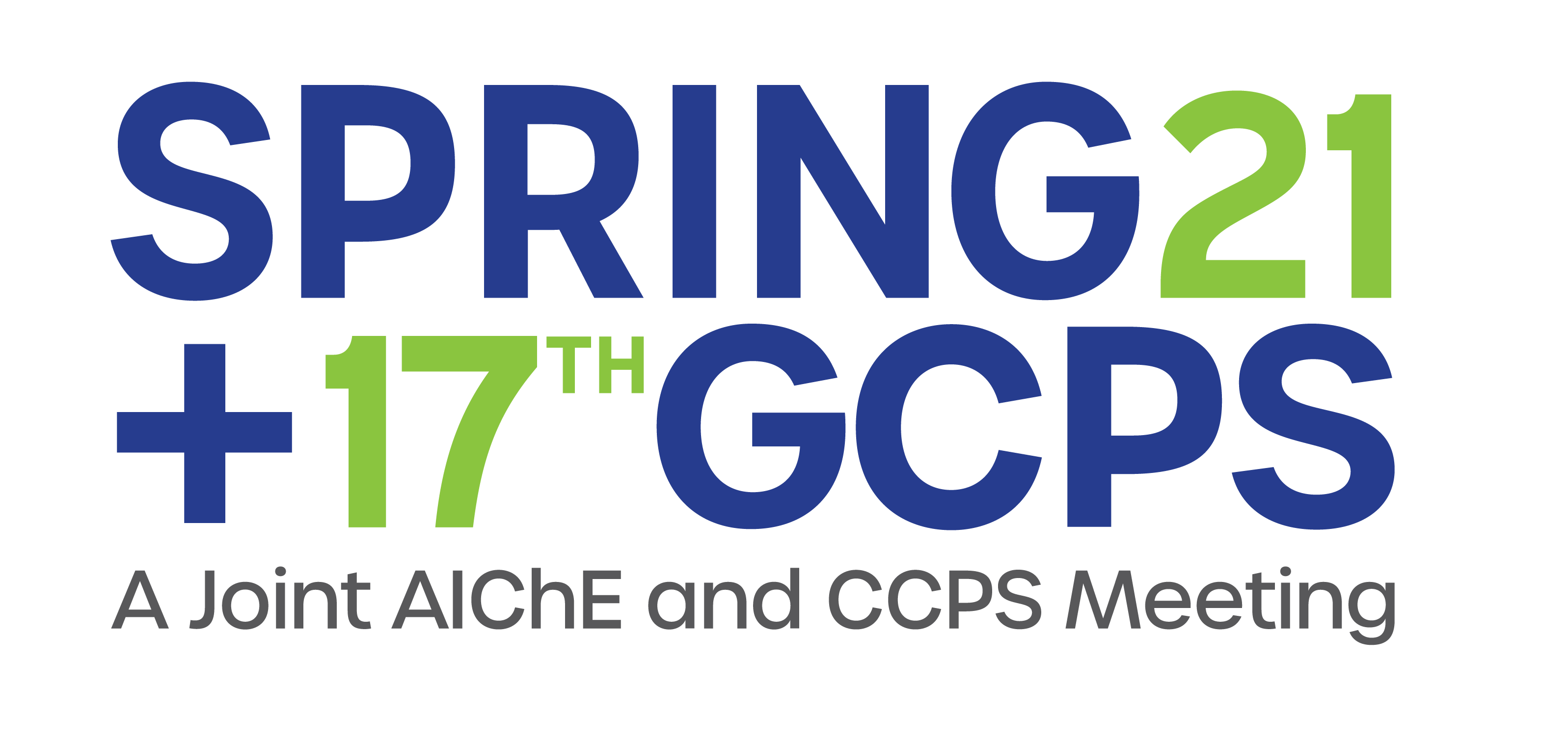
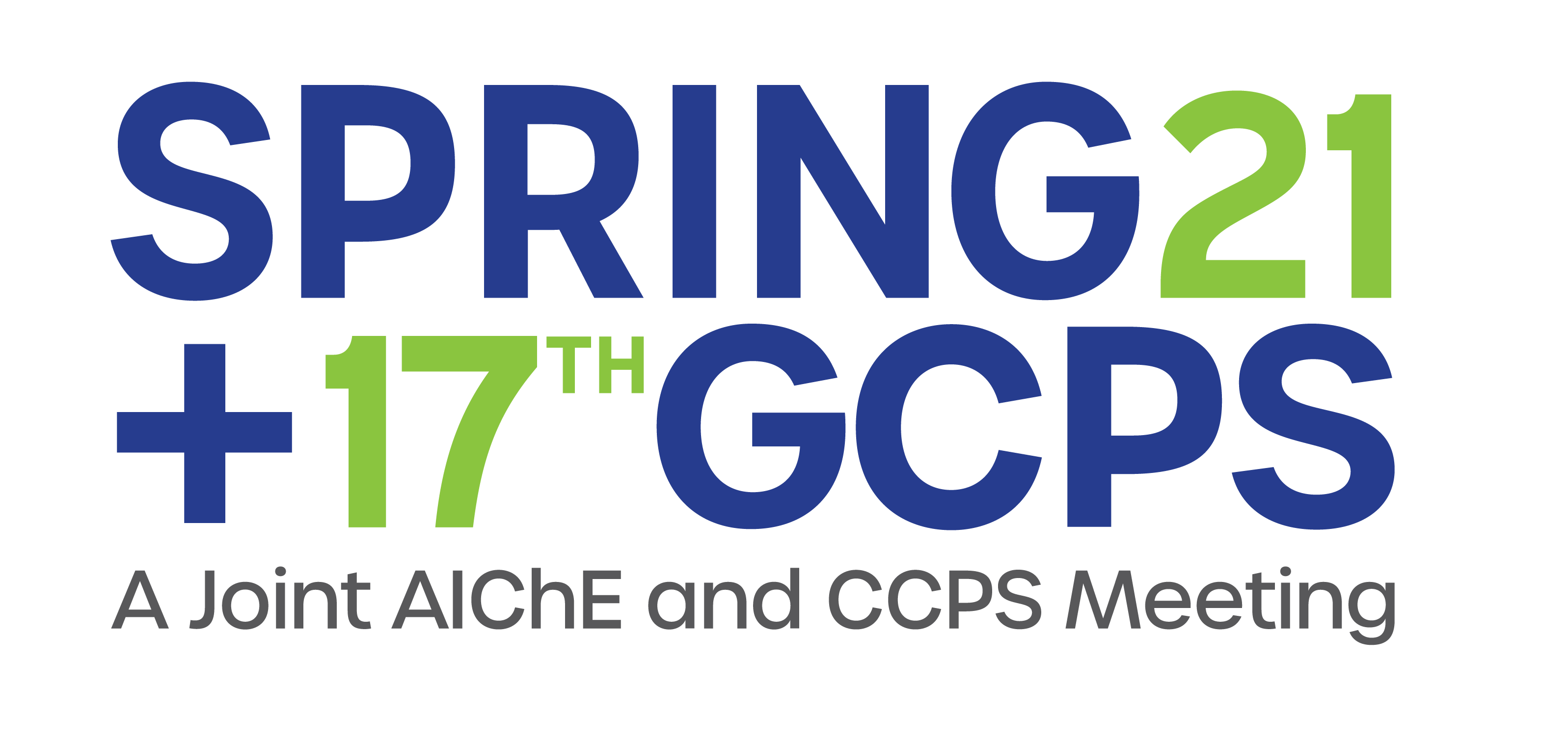
This work was designed to present to NETWORK Research and Services, a demonstration of the concepts and applications of real cases in the area of Human Factors, Risk, Reliability and Crisis. Although we work with Complex Systems that are difficult to predict (such as the chemical process industries) and understanding the nature of the processes in Sociotechnical Systems, we can build Rules and Barriers that have better results than current ones. Concepts are the basis, tests are confirmation, algorithms indicate associated methods and techniques and validation indicates the certainty of achieving good results. In the case of Reliability, the concepts and algorithms were tested with real cases from the Oil Industry.
The new concepts are systemic failure; cultural force field; socioeconomic and affective utility of the task versus feedback; causal link of low risk perception; difference between enabling elements of hazard energy versus human factors in the operational situation; management models to avoid accidents and to avoid energy losses and respective techniques that include the discussion about culture and human factors.
A discussion of cultural threats of behavior change (example: culture of guilt and generational conflicts) and application cases indicating solutions to bad habits and incorrect decisions, they make it easier to understand why social risks are dynamic and do not separate from the operational routine.
The human elements are part of the project and cut (disable) the flow of dangerous energy. The intention is that these elements of the safety culture and the technological project are safeguards, but it may be that the project is incomplete or that the barriers have suffered social and physical threats, reducing resistance in relation to the load. These elements of the managerial (stress and leadership), technological (risk and complexity) and behavior (4Cs) dimensions will be limiting the passage of energy by human factors (which includes management, culture, organization and technology). The 9 levels of human factors that will compose the Bayesian network are: Culture, Social Phenomenon, Company, Management & STAFF, Group and Individual, Operational Control, Failure Control, Accident and Crisis or Disaster.
The Investigation on the Operational and Technical Culture indicates the formal and informal rules of operation of the team in the Operational Routine, allowing the prediction of the future behavior of the worker, the process and the equipment from the signs of failure. It is possible to calculate the level of approach of the discomfort zone for safety events from this plant history. For this we use, data mining, grouping, analysis of main components; definition and calculation of the objective function, heuristic rules, and adjustment of factors through fuzzy mechanics.
This solution-guiding document addresses events with different stress levels in which the operating team lives: operational deviations, uncontrolled processes, damage on equipment, and task failures, safety events such as fire, and catastrophic events that unfold for crisis. Theoretical models are presented, discussion of human error in emergencies, and proposal of appropriate competence for emergency brigade.
The internal and external regulation after these discussions needs to revise its principles to correct the standardization and organizational communication processes, which would change the procedures for team building and the criteria for the technology project. Thus, the discussion on the regulation and formatting of human elements and human factors will clarify technicians and managers as to what should be done. An improvement program that includes researching lessons learned is included in the work.
Finally, here technological solutions are suggested in the technological, managerial, social and organizational dimension for the best control of companies. Products and Processes, Courses, Interventions in Human Factors to review concepts and habits. Based on the experience of the metallurgical industry, we propose interventions to adjust the safety culture. Also for better guidance on mathematical and statistical techniques, we present a roadmap and the reference area. A brief presentation of the techniques for identifying and measuring behavior variables (enabling elements) is carried out.
keywords: reliability, human fator, organizational culture, just culture, safety