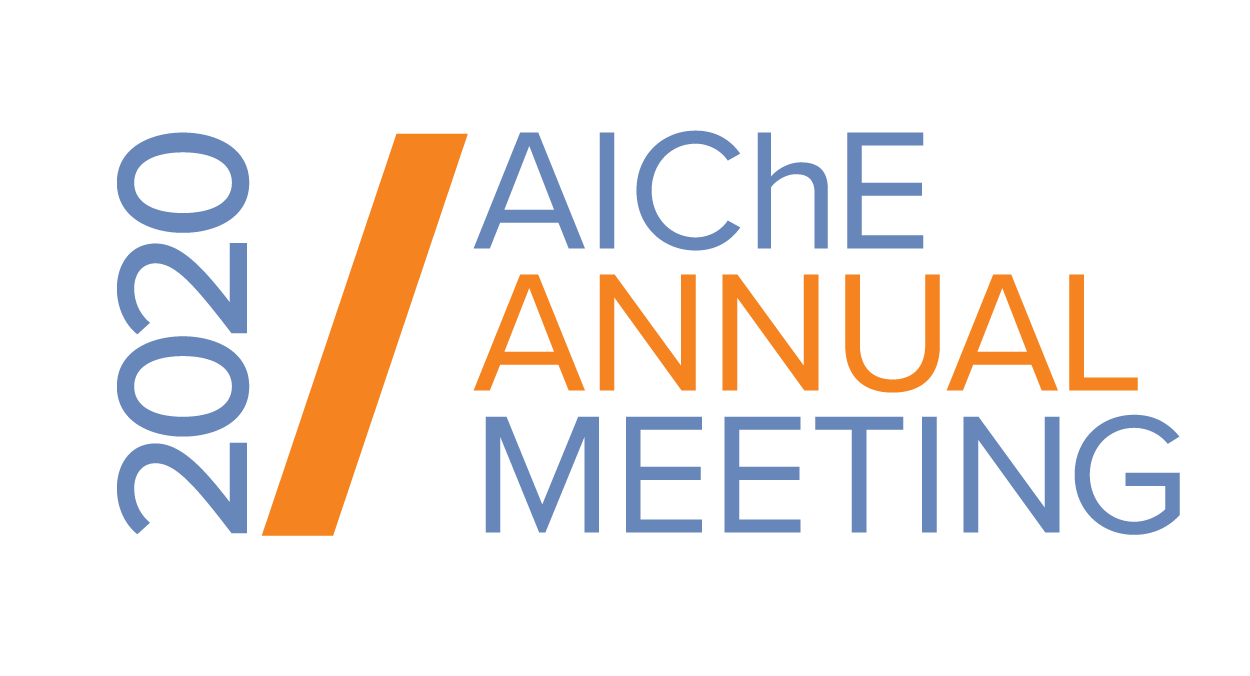
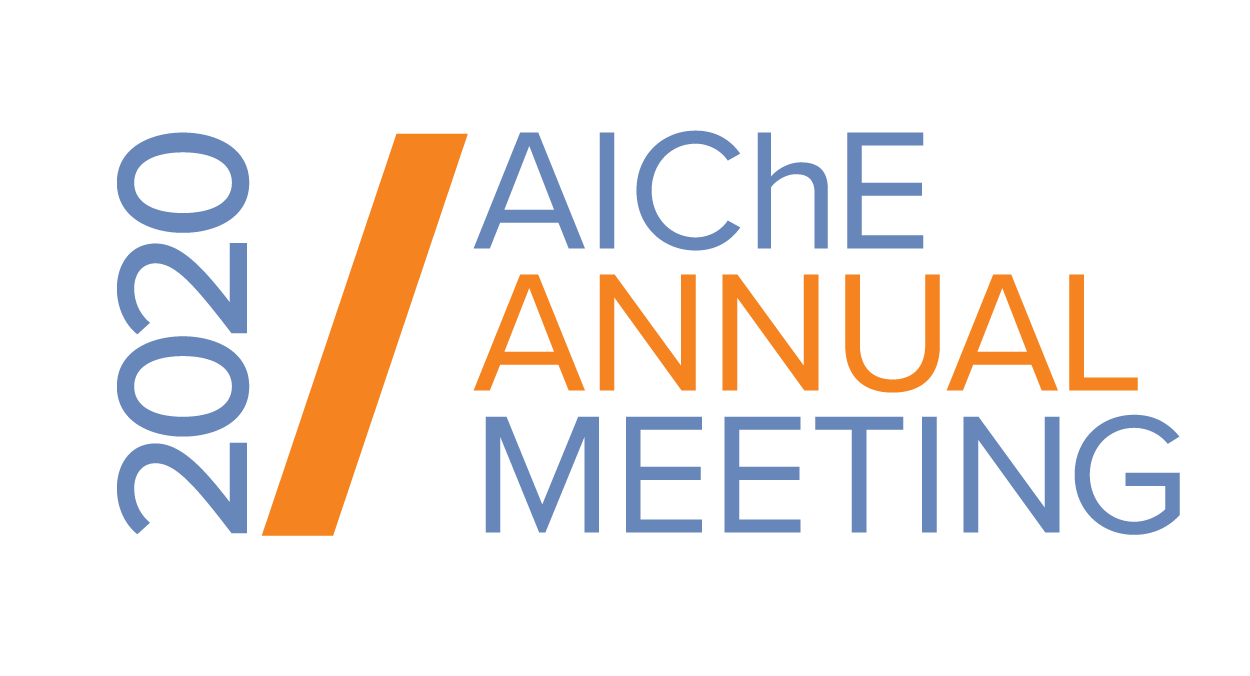
For the efficient implementation of digital-twin framework, real-time modeling strategies concerning virtual model and plant updates need to be developed. The presented work focuses on developing these strategies, where the major aspects involve: 1) model maintenance based on real-time data obtained from plant operation; 2) algorithms for real-time system analyses; 3) determination of frequency criterion for model and plant updates. Model maintenance of the virtual plant is performed using model adaptation strategies, including recursive adaptation and ensemble-based methods [3,4]. Unlike commonly used methods where models are updated and maintained off-line, these strategies allow real-time model updates in the virtual plant during manufacturing plant operation. After developing real-time model updating strategies within the digital twin framework, the model updates are used for dynamic system analyses, like sensitivity and feasibility analysis [5-7], providing uninterrupted monitoring of process performance. Based on these analyses, corrective process improvements are suggested for real plant operation, in situations where, the current process settings can potentially lead to violations of drugâs quality specifications. Along with this capability of real-time update of virtual and real plant, frequency criterion for these updates need to be investigated for an efficient update strategy in the digital twin framework. These updates are generally performed at the same frequency associated with plant measurements [8] but can be modified based on a user-defined plant-model mismatch criterion [9] to reduce required computational resources.
In this presentation, the results of such a framework for a continuous direct compaction line, together with Industry 4.0 will be illustrated. This will allow for a computationally efficient and robust implementation of digital-twin framework in pharmaceutical manufacturing for scientific, risk-based regulation compliant process operation.
Reference:
[1] M. Grieves, J. Vickers, Digital Twin: Mitigating Unpredictable, Undesirable Emergent Behavior in Complex Systems, in: Transdisciplinary Perspectives on Complex Systems, Springer, Cham, 2017: pp. 85â113.
[2] A. Belhadi, K. Zkik, A. Cherrafi, S.M. Yusof, S. El Fezazi, Understanding Big Data Analytics for Manufacturing Processes: Insights from Literature Review and Multiple Case Studies, Computers & Industrial Engineering. 137 (2019).
[3] P. Kadlec, R. Grbic, B. Gabrys, Review of adaptation mechanisms for data-driven soft sensors, Computers & Chemical Engineering. 35 (2011) 1â24.
[4] K. Hazama, M. Kano, Covariance-based locally weighted partial least squares for high-performance adaptive modeling, Chemometrics and Intelligent Laboratory Systems. 146 (2015) 55â62.
[5] G. Bano, Z. Wang, P. Facco, F. Bezzo, M. Barolo, M. Ierapetritou, A novel and systematic approach to identify the design space of pharmaceutical processes, Computers & Chemical Engineering. 115 (2018) 309â322.
[6] Z. Wang, M.S. Escotet-Espinoza, M. Ierapetritou, Process Analysis and optimization of continuous pharmaceutical manufacturing using flowsheet models, Computers and Chemical Engineering. 107 (2017) 77â91.
[7] F. Boukouvala, V. Niotis, R. Ramachandran, F.J. Muzzio, M. Ierapetritou, An integrated approach for dynamic flowsheet modeling and sensitivity analysis of a continuous tablet manufacturing process, Computers & Chemical Engineering. 42 (2012) 30â47.
[8] G. Bano, P. Facco, M. Ierapetritou, F. Bezzo, M. Barolo, Design space maintenance by online model adaptation in pharmaceutical manufacturing, Computers & Chemical Engineering. 127 (2019) 254â271.
[9] A.S. Badwe, R.D. Gudi, R.S. Patwardhan, S.L. Shah, S.C. Patwardhan, Detection of model-plant mismatch in MPC applications, Journal of Process Control. 19 (2009) 1305â1313.