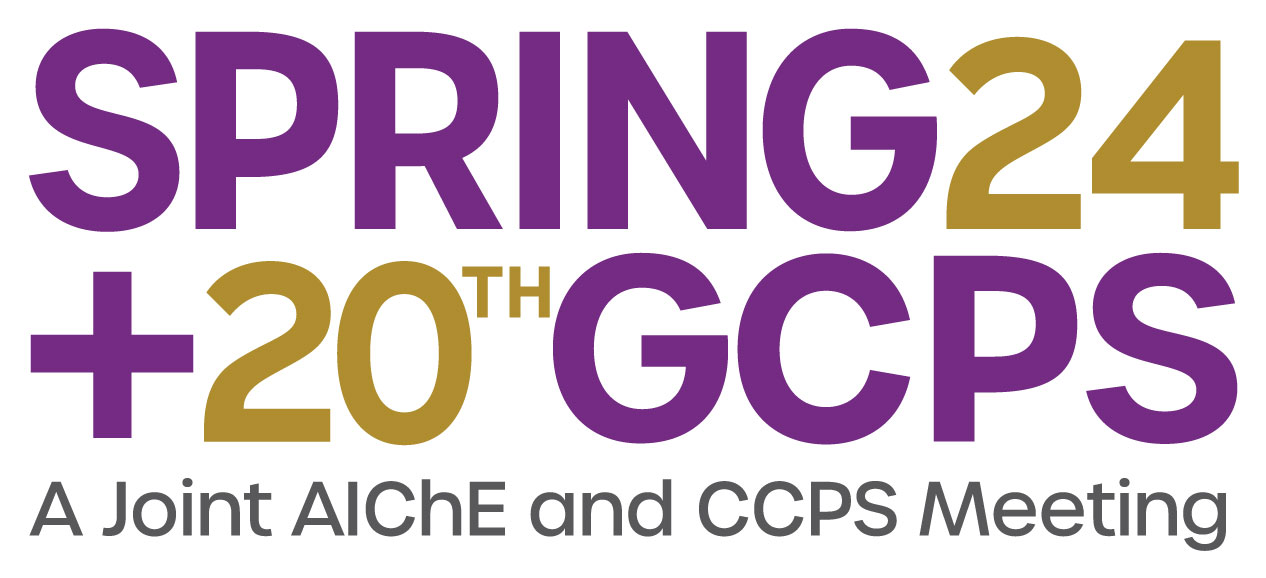
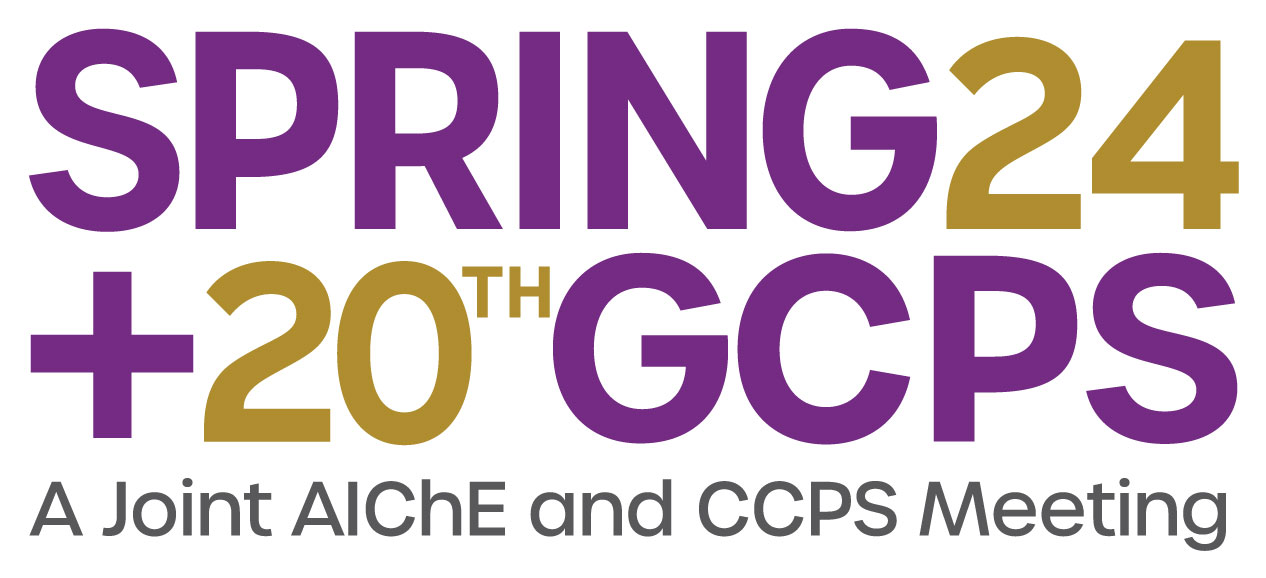
Catalytic reactors are important in many application areas, ranging from hydrogen, fuels, plastics, pharmaceuticals, food products, emission control, and countless others, with reactors and catalysts often engineered to minimize unwanted by-products. Catalyst development often involves testing small scale experimental systems that have vastly different heat and mass transfer characteristics as compared to those of commercial-scale reactors. For example, lab-scale powder experiments may be minimally affected by internal mass transfer resistances, while narrow tube diameters may limit radial temperature variability inside the packed bed. Also, catalyst coatings on structured reactors such as monoliths may have a thermal profile that is difficult to measure during testing. Batch autoclave reactors reduce external transport limitations but reveal little about what happens inside a catalyst where concentrations may be very different from those in the bulk mixture. Given these experimental challenges, translating performance between reactor scales, or identifying catalyst performance problems is greatly enhanced by accessible reaction engineering tools.
Practical catalysts balance non-linear multi-step reactions with second-order diffusion effects. This interplay can reveal unexpected findings that mask laboratory observations or scale-up problems. Critical diffusion dimensions that affect side reactions depend on the reaction network complexity. These critical diffusion lengths that inhibit side reactions may be on the order of just a few mm, or as large as 1000+ mm. The âsecret life of catalystsâ occurs inside catalyst structures (e.g., pellets, powders, and wall coated catalysts), where transport is controlled by diffusion and where series or series-parallel reactions can dominate. Although this internal region physically contains most catalyst sites, complex reactions inside pore structures are generally poorly analyzed and rarely optimized. Side reactions that run amok inside a catalyst can be conflated with an intrinsic catalyst problem and the catalyst practitioner may move to the next formulation or condition. Reduced performance at scale can become accepted, instead of being understood and improved upon.
The physics of coupled reaction and diffusion is not new, described by (among others) Turing (1952), Aris (1975) and Fogler (1986). Every undergraduate chemical engineer learns the principles of internal diffusion limitations and a simple effectiveness factor analysis in their reaction engineering class.
The problem lies in the use of simplified analyses. Reality is often more complex and interesting than a simplified analysis might conclude. So why is this known effect of internal diffusional resistance coupled with reaction mostly ignored or oversimplified? Accessible reaction engineering tools are not routinely available nor are results generally expected to challenge the interpretation of laboratory data. Here, accessible means readily usable with little programming or customization needed for the chemical engineer more interested in the application than the theory. Without such reactor simulation tools, it is difficult to see what one doesnât expect to find.
DETCHEM (2022) is a suite of accessible reaction engineering tools designed to help to understand what happens inside a catalyst, integrating:
- multi-step reaction kinetics, either from microkinetic models with perhaps hundreds of steps or apparent rates with a few steps, coupled with
- catalyst internal pore diffusion that may be molecular, Knudsen, or mixed, coupled with
- realistic heat transfer models, such as state-of-the art correlations for packed beds, structures, or open channels, to model the flow of heat that results from exterior heating/cooling along with endo- or exothermic heat transfer demands linked to the kinetic mechanisms.
It is much easier to blame the catalyst for poor performance and move to the next interesting science experiment or accept the industrial expectation that performance deteriorates with scale up. Reaction kinetics are the Rosetta Stone to translate between catalyst geometries and reactor scales. Evaluating catalyst performance that includes realistic pore diffusion and reaction coupled with local heat transfer can reveal the true nature of a problem and provide clues on how to find practical solutions.
Interesting reaction examples will be discussed that reveal the secret life of catalysts. A Dry Reforming of Methane (DRM) Nickel catalyst was shown to concentrate CO inside the pellet when operated with a S:C below 1.5 and a high pressure of 20 barg. The calculation of carbon activity inside the 6-mm catalyst tablets revealed the likely location coke formation, both in terms of axial position along the length of the reactor and radial position inside the pellet. Subsequent SEM-EDS confirmed this prediction with an internal measurement of coke which coincidently deteriorated performance over time. The same Ni-based catalyst formulation was coated as a thin layer on a highly conductive HeatPathTM catalyst pellet and operated at very low S:C without coke formation detected by SEM-EDS inside the spent pellets. There was also no loss of reactor performance with this HeatPathTM catalyst. The problem was found and resolved by first fitting apparent reaction kinetics, and then evaluating configurations and operating conditions using DETCHEM PBR to maintain a carbon activity of less than one anywhere inside the thinly coated catalyst. Without the right accessible tools, finding an engineering solution would have been extremely difficult.
In another example, a DETCHEM PBR analysis of RWGS on a Nickel-based catalyst was completed to determine how to best configure a catalyst to operate at pressure without coke formation. A microkinetic model with 6 gas phase species, 13 surface species, and 52 surface reactions was used to model the catalyst. Catalyst particles of reasonable dimensions for commercial fixed bed reactors show a strong internal pellet CO concentrating effect and a carbon activity greater than 1. The concentration of CO at the center of the pellet is substantially higher than at the edge of the pellet. To evaluate the effect of thin coatings and the potential for coke formation, the same RWGS microkinetics were also applied to a model of a wall coated monolith reactor using DETCHEM CHANNEL. Catalyst thickness varied between 10 and 100 microns. A critical catalyst thickness was identified for the structured catalyst, beyond which the carbon activity inside the wall coating can also exceed unity. Surprisingly, the detailed microkinetic model shows a small methane formation rate (selectivity <2%) for which the highly exothermic methanation reaction can in some cases maintain a sufficient internal catalyst temperature to overcome carbon formation in a monolith. An alternative catalyst formulation that suppresses methane formation would not benefit from this extra heat and would be more likely to form coke in the slightly colder catalyst interior. A coated highly conductive catalyst pellet could also overcome the predicted carbon formation. For these cases, direct local temperature measurements are challenging, and the solution to promote a small amount of methanation is only found via simulation. Once again, accessible DETCHEM tools augment development to see what is happening inside the catalyst. The secret life of catalysts is no longer hidden, but now understood and problems overcome by changing geometry, operating conditions, thickness, or any other parameter available to the engineer.
The tradeoff of kinetics, pore diffusion, and heat transfer can lead to surprising, counterintuitive, and interesting findings. This secret life of catalysts might be promoting unwanted series or series-parallel reactions that are difficult to understand without supporting reaction engineering tools. Or, in the case of the RWGS catalyst, a small amount of methanation (i.e., an unwanted side reaction) proved to be beneficial. Here, improving a catalyst to reduce methanation could in fact exacerbate carbon formation. For a practitioner, experimental observation alone would be challenging to understand why one system failed and the other did not. Development time and cost can be reduced by guiding efforts with useful analysis tools.
The use of accessible reaction engineering tools (such as DETCHEM PBR and DETCHEM CHANNEL) speeds development and catalyst optimization, avoids pitfalls of experimentally missing the âsweet spotâ, reduces scaleup risk, and may solve vexing plant problems.
References
R. Aris. The Mathematical Theory of Diffusion and Reaction in Permeable Catalysts: The theory of the steady state. Clarendon Press, Oxford, 1975.
O. Deutschmann, S. Tischer, C. Correa, D. Chatterjee, S. Kleditzsch, V.M. Janardhanan, N. Mladenov, H. D. Minh, H. Karadeniz, M. Hettel, V. Menon, A. Banerjee, H. Gossler, A. Shirsath, E. Daymo, DETCHEM Software package, 2.9 ed., www.detchem.com, Karlsruhe 2022.
H.S. Fogler. Elements of Chemical Reaction Engineering, Prentice Hall, New Jersey, 1986.
A. Turing. The chemical basis of morphogenesis. Phil. Trans. R. Soc. London, 237:37â72, 1952.
Presenter(s)
Language
Pricing
Individuals
AIChE Member Credits | 0.5 |
AIChE Pro Members | $19.00 |
Fuels and Petrochemicals Division Members | Free |
AIChE Graduate Student Members | Free |
AIChE Undergraduate Student Members | Free |
AIChE Explorer Members | $29.00 |
Non-Members | $29.00 |