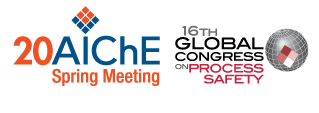
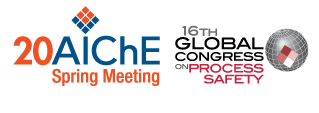
Title: Use of Live Barrier Health Models to Proactively
Manage Risk
Rae-Ann Joseph
Michelle Aquing-Bissoon
Atlantic LNG Company of Trinidad and Tobago
Keywords:
Barriers, Safety critical equipment
The
goal of every chemical plant should be to ensure it is well designed, safely
operated and properly maintained. In order to do this, it must demonstrate its
assets are safe i.e. secure from threat of danger, harm, or loss[1]. Process Safety management accomplishes
this by focusing on the prevention of uncontrolled releases of hazardous materials
through the use of barriers.
The
Center for Chemical Process Safety (CCPS)[2]
defines a barrier as a control measure or grouping of control elements that on
its own can prevent a threat from developing into a hazardous scenario
(prevention barrier) or can mitigate the consequences once it has occurred
(mitigation barrier). Barrier
Management is a systematic approach for assessing and monitoring identified
barriers to ensure they are functional, effective and available when called
upon to prevent or mitigate against hazardous scenarios.
This paper focuses on the
management of safety critical equipment barrier health to ensure facility
hazards and risks are properly managed, and to provide assurance that the
facility is safe to operate. This assurance can be demonstrated by using the
following steps to establish a real-time Barrier Health Model which focuses
primarily on physical barriers e.g.
pressure relief devices:
1. Develop Bow ties for
major accident scenarios (potential for one or more fatalities) using the
facilitys Hazard Identification studies.
2. Identify and categorize
hardware barriers identified in Bow ties using the eight barrier groups
outlined in the International Association of Oil and Gas Producers (IOGP)
Report 415 Supplement: Standardization of Barrier Definitions e.g. Ignition
control, Shutdown Systems.
3. Conduct barrier
effectiveness assessments using work orders, mechanical integrity inspection
results, root cause failure analyses, records of temporary impaired conditions
and relevant risk studies etc.
4. Use the data collated
to ascertain the barriers health as effective, partially effective or impaired
and use visualization tools connected to a computerized maintenance management
system (CMMS) to provide a comprehensive risk profile e.g. a Swiss Cheese
Barrier Model, or Bow Ties. For instance the figure below shows barrier
groups for Process containment and Detection systems as partially effective
(yellow), while Shutdown systems is impaired (red).
5. Assess the cumulative
risk to the facility. This is critical because individually, the barrier degradations
may not seem significant enough to prevent the consequences of a major
accident. However, when the defects (holes) in the relevant barriers line up,
there may be no effective protection in place between the hazard and a major
accident or undesired consequences.
6. Use a risk based
approach to evaluate the criticality of barrier impairments and develop
remedial plans to reduce the cumulative residual risk posed by impaired
barriers.
7. Continuously track and
monitor barrier health using well-defined metrics and take corrective action
and proactive measures to address impairments in a timely manner.
A live barrier model approach helps to provide a
clear picture of the facilitys barrier health, increased awareness of the
importance of safety critical equipment and an informative real-time tool to
support risk based decision making while operating and maintaining the
facility.
Example of a Live
Swiss Cheese Barrier Health Model
Presenter(s)
Language
Pricing
Individuals
AIChE Member Credits | 0.5 |
AIChE Pro Members | $19.00 |
Employees of CCPS Member Companies | Free |
AIChE Graduate Student Members | Free |
AIChE Undergraduate Student Members | Free |
AIChE Explorer Members | $29.00 |
Non-Members | $29.00 |