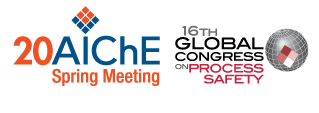
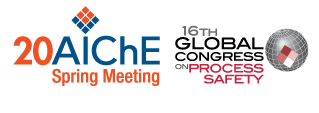
Increased environmental awareness and concern over emissions have driven an industry-wide trend toward implementing totally enclosed ground flares (TEGFs) in both new and existing plants. TEGF systems utilize a refractory lined combustion chamber to minimize noise, obscure flames, and prevent radiation outside of the enclosure, and they provide smokeless combustion and high turndown capabilities via staged headers and an array of burners. These features make them an attractive alternative to more conventional flaring systems when facilities are located near populated areas or in environmentally sensitive areas, or when a smaller footprint is desired.
While the multi-stage design of TEGFs allows for efficient, smokeless operation over a wide range of flows, the physical constraints of the enclosure may limit overall capacity. This makes them well-suited as supplements to higher capacity elevated flare systems for lower pressure day-to-day flaring activities. The more granular turndown capabilities of the multistage design introduces significant complexity to the control and operation of flare systems, however, especially when used in conjunction with elevated flares. As these systems are designed and implemented, it is important to ensure that they can be operated and controlled within the full range of design, which requires a transient analysis of the staging and de-staging of the system.
This paper will discuss the use of dynamic simulation to validate the design of TEGFs and associated control systems. Transient scenarios including both planned releases (e.g. maintenance) and emergency releases were simulated to demonstrate methods to validate the staging and de-staging capabilities of a TEGF as well as the load-sharing and flow distribution when TEGFs are paired with elevated flare systems. Of particular concern was ensuring that a TEGF can stage and de-stage within its design capacity without diverting flow to the elevated flare.
Specific control considerations for the staging and de-staging of TEGFs that will be discussed include valve timing, stage sequencing, delays, override functions, and relative staging setpoints for the TEGF and any parallel systems. Additionally, the impact of high temperature de-staging and the design of rupture pin bypass valves will be discussed.
While the multi-stage design of TEGFs allows for efficient, smokeless operation over a wide range of flows, the physical constraints of the enclosure may limit overall capacity. This makes them well-suited as supplements to higher capacity elevated flare systems for lower pressure day-to-day flaring activities. The more granular turndown capabilities of the multistage design introduces significant complexity to the control and operation of flare systems, however, especially when used in conjunction with elevated flares. As these systems are designed and implemented, it is important to ensure that they can be operated and controlled within the full range of design, which requires a transient analysis of the staging and de-staging of the system.
This paper will discuss the use of dynamic simulation to validate the design of TEGFs and associated control systems. Transient scenarios including both planned releases (e.g. maintenance) and emergency releases were simulated to demonstrate methods to validate the staging and de-staging capabilities of a TEGF as well as the load-sharing and flow distribution when TEGFs are paired with elevated flare systems. Of particular concern was ensuring that a TEGF can stage and de-stage within its design capacity without diverting flow to the elevated flare.
Specific control considerations for the staging and de-staging of TEGFs that will be discussed include valve timing, stage sequencing, delays, override functions, and relative staging setpoints for the TEGF and any parallel systems. Additionally, the impact of high temperature de-staging and the design of rupture pin bypass valves will be discussed.
Presenter(s)
Once the content has been viewed and you have attested to it, you will be able to download and print a certificate for PDH credits.
If you have already viewed this content,
please click here
to login.
Language
Pricing
Individuals
AIChE Member Credits | 0.5 |
AIChE Pro Members | $19.00 |
AIChE Graduate Student Members | Free |
AIChE Undergraduate Student Members | Free |
Computing and Systems Technology Division Members | Free |
AIChE Explorer Members | $29.00 |
Non-Members | $29.00 |