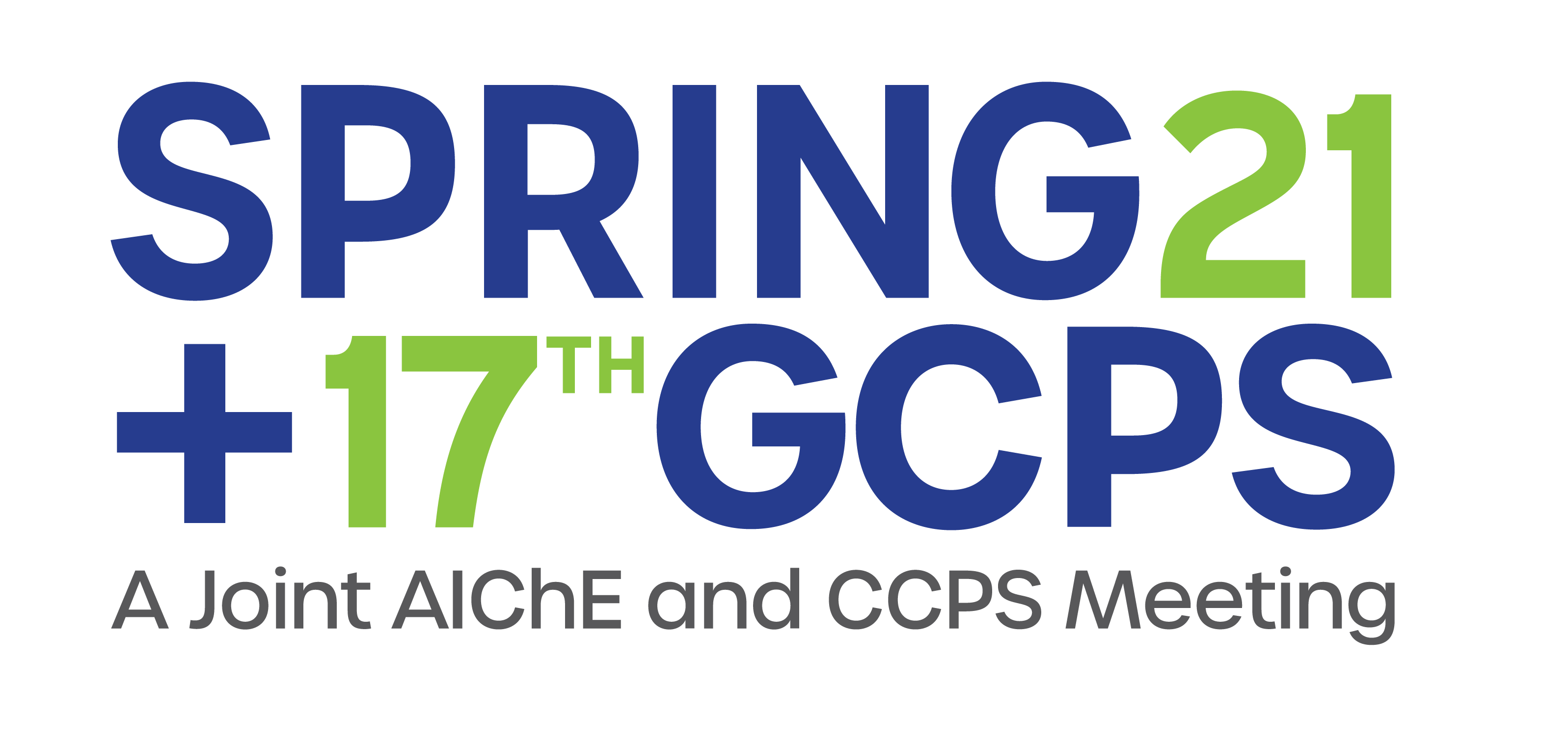
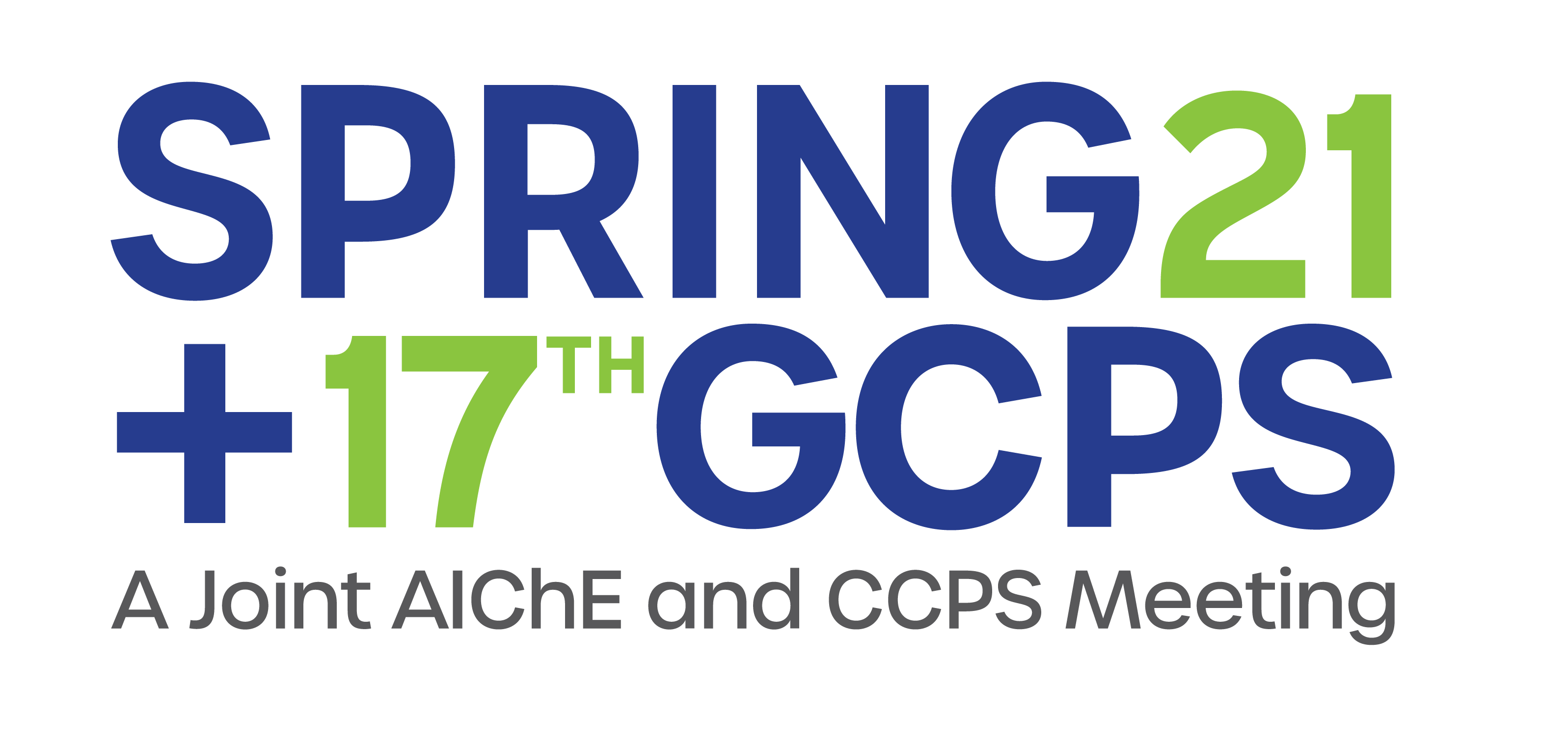
However, in a personâs professional life, it is common to have a significant portion of oneâs day composed of filling out paperwork and performing hands-on tasks. Although work instructions, procedures, and policies for everyday tasks are now available electronically, a field employee needs access to a computer to view, access and print documents. This limits the productivity and effectiveness of employees since it forces them to access all information at a single access point or having them carry around paperwork that can easily be damaged by work conditions and the environment. One limitation is unexpected equipment failure. In such cases, it is rare that employee would have all technical information readily available to help troubleshoot in the field immediately, except for minimal visual HazCom labels and warnings. This decreases overall process efficiency by inadvertently creating restraints â specifically, having to go back and collect all required paperwork- on the employee which can be overcome with everyday technology.
Understanding how so much information is instantly available outside of work is important to replicate that level of access and ease in the workplace. At Rain Carbon Inc., our mission is to be âa progressive industrial company committed to collaborative science-driven innovations that result in safe, reliable and efficient operations to ensure outstanding results for our customers, partners, employees and investors.â With this as our guide, a new system was implemented to target several areas: safety, reliability, information availability and efficiency.
At our Candiac advanced materials site in Quebec, Canada, integrative software was implemented in 2017 as a pathway to achieving the companyâs mission. This software provides instant access to process information through phones, tablets and computers, including work instructions, policies, procedures, ability to complete round check sheets and work permits, action assignment and tracking, picture and video capability, report unsafe conditions and incidents, equipment malfunctions, and the management of workforce skills. The capabilities provided by the software have proven to be most effective when used on mobile devices as it allows for information to be accessed directly from any location within the plant helping us improve in all the below points:
- Enhancing site management by providing a live view of notices, work requests and unsafe conditions to immediately communicate and respond to the situation at hand;
- Increasing employee involvement in safety due to higher visibility and lower response times to address unsafe acts/conditions;
- Reducing redundancies of having to go back and forth between paper and electronic work; and
- Decreasing unplanned downtime by providing all relevant technical information instantaneously enabling employees to address deficiencies without delay.
Rain Carbon has pushed forward with innovation and technology by implementing QR codes for all equipment linked to the integrative software solution. This adds a significant amount of efficiency to work processes on the shop floor. When unplanned work is to be performed, the employee can take any mobile device with the software installed on it and scan the QR code on the respective equipment. This will take the employee to a screen with all necessary information regarding the respective equipment, including the work permit and list of materials needed to perform the work in question. A process that would, in most cases, take a matter of hours is reduced to a few minutes and a couple of taps.
Although reliability and efficiency have increased since the system was implemented at the Candiac facility, the most significant improvement has been observed in safety. Prior to implementing this software, safety walks were completed in an electronic or printed version of a Word document, safety incident notifications would be accomplished through phone calls and emails, and near misses would be recorded in a separate system. The centralization of reporting and the enhanced information availability highly encouraged employees to report all safety items with the backing of a more engaged management group, thus enhancing employee safety. Reporting increased with the introduction of the program by 772% on the first year and by 2,150% on the second year. Similarly, during that timeframe, near misses decreased by 40% and first aid cases by 33% compared with the current year.
Results:
From 2017 to 2019, there was a clear increase in reporting after the implementation of the software. Through management support and commitment, we can see a clear decline from 2019 to 2020 YTD of overall identified items, increasing the quality of work and safety across the site.
Implemented in 2017, the program has significantly improved the safety performance of Rain Carbonâs Candiac site by engaging management and ensuring all safety items are properly communicated and addressed with as little downtime as possible.