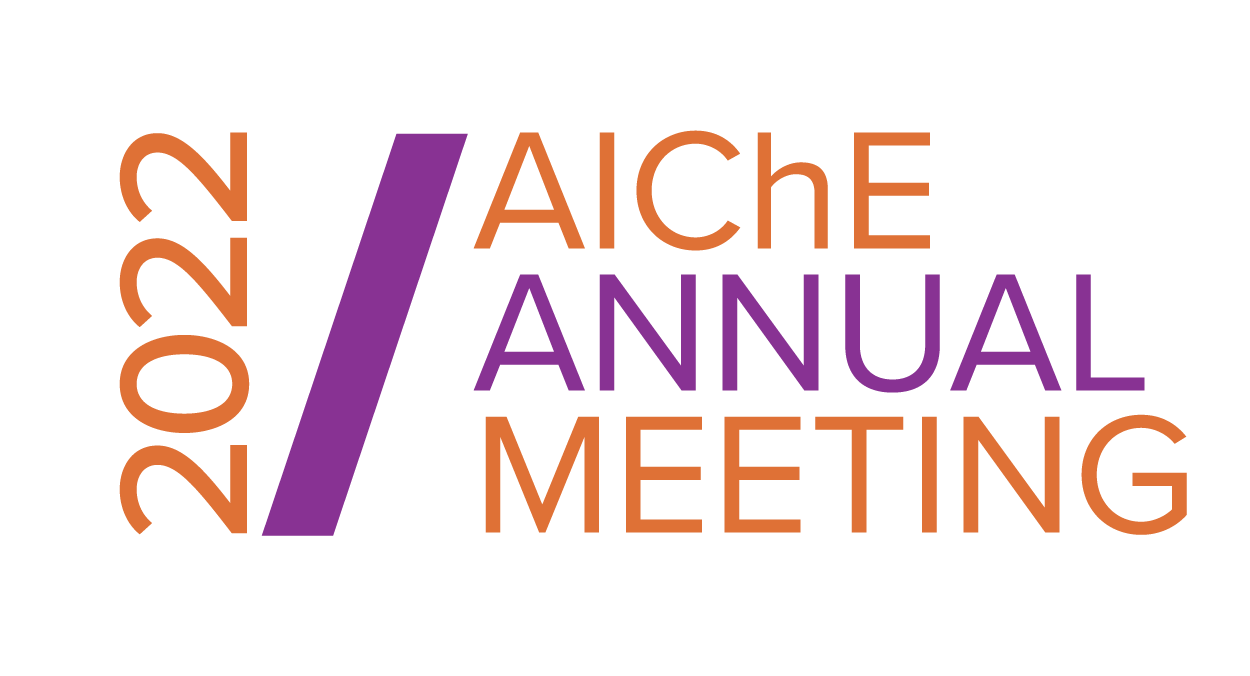
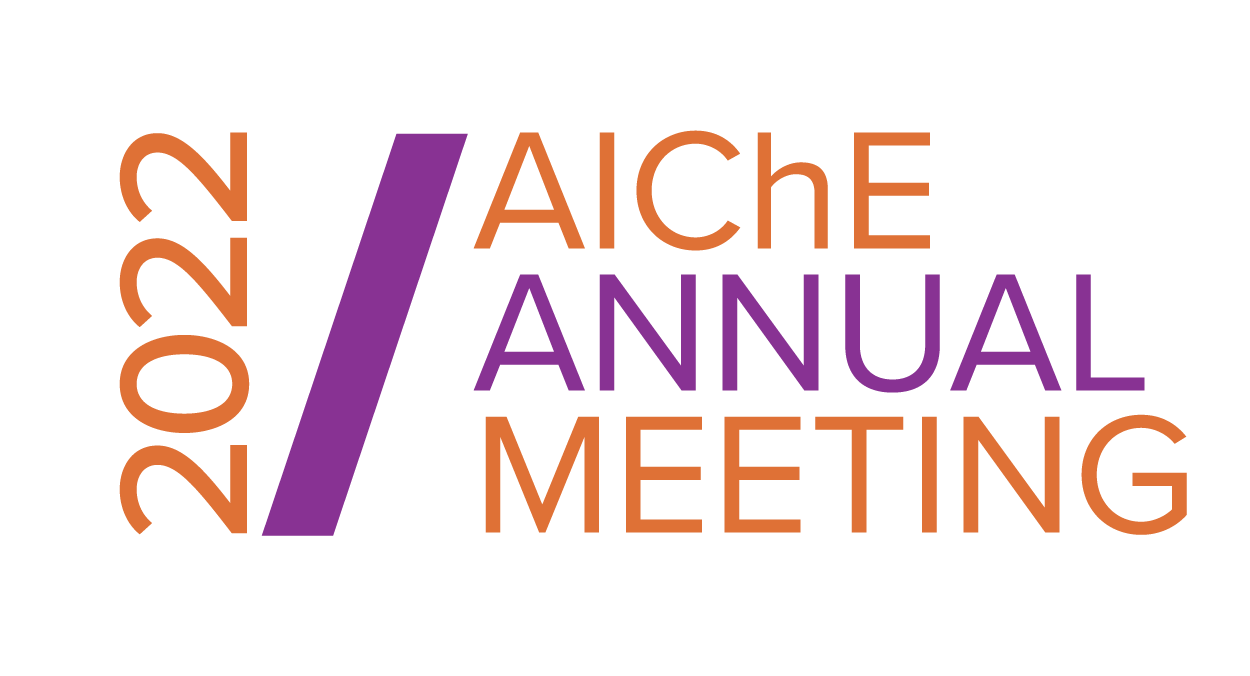
Reducing the energy intensity of molecular separation was Identified as one of the big challenges by the National Research Council 2006 report for achieving the development of a sustainable future chemical enterprise. Distillation has been and continues to be the most common method to separate a variety of molecular mixtures in chemical and petrochemical industries. Nevertheless, In this work, we systematically compare the power requirements of membrane and in recent years there has been an increasing interest in replacing distillation processes with membrane based processes with the claim that they have the potential to improve energy efficiency by tenfold. distillation processes for binary liquid and gaseous hydrocarbon mixtures where the desired product component is more permeable and also more volatile. We first provide a shortcut method calculation to compare the efficiency of heat pump and steam driven distillations. Then, power requirements of heat pump distillation and membrane separation are compared on an equivalent power basis. We find that both membranes and distillations have preferred energy efficient domains. Distillation generally requires lower power when either high component recoveries are needed (at all tested product purities), or high purity product streams with modest recoveries are needed. For a high purity product at modest recoveries, membranes have a potential to provide energy benefits for highly enriched feeds, especially those composed of close boiling components. Additionally, when feed concentration is moderate to high and product recovery and purity are modest, membranes are likely to show modest efficiency gain. On the other hand, distillation outperforms membranes under many situations and often the reduction in energy consumption is substantial.
Presenter(s)
Once the content has been viewed and you have attested to it, you will be able to download and print a certificate for PDH credits.
If you have already viewed this content,
please click here
to login.