Saudi Aramco just invested $30 million in Siluria, a startup that could radically change the petrochemical business. The deal comes with a transformative technology which, like many others, poured out of professor Angela Belcher's Biomolecular Materials Group at MIT, where she's engineered an army of viruses to jump through nano-hoops.
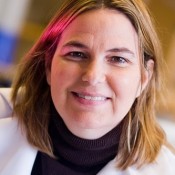
Other than the pricey virus snapped up by the Saudis (press release), some of her other viruses power batteries or collect electrons in solar cells more efficiently. She's so prolific that she received the $500,000 Lemelson-MIT Prize last year, honoring her for improving the world through invention. Accepting the award, she spoke about finding inspiration (peering down to the nano-level) in nature's ability to create materials, like the DNA-programmed abalone growing its own shell.
A long coveted process
Other than face time with Angela, what did Aramco get for their hefty investment? With the world drowning in natural gas, Siluria says that it has opportunely solved one of the hardest and most profitable problems in petrochemistry by using technology from Belcher's lab: the oxidative coupling of methane (OCM) into ethylene.
Since methane is cheaper than naphtha or ethane normally converted by steam cracking, the startup has turned a $200-per-ton molecule into a ubiquitous $1200-per-ton chemical money machine. Who hasn't used plastic bags, bottles, boxes and containers? Ethylene is the most widely produced organic compound in the world, with global production around 107 million tons in 2006. (Every landfill is a steam cracking museum.)
Since Saudi Arabia is already a large producer of industrial chemicals, Siluria's method will allow the country to produce ethylene at low cost while supplying a hedge from the volatile prices of conventional feedstocks.
Struggling during the 80s and 90s
Why was Siluria able to crack the code, when some of the world's biggest petrochemical makers struggled for years to perfect OCM but could never compete with tried-and-true method of steam cracking. Their catalysts didn't have the right selectivity, activity rates, or petered out too quickly. So after an initial gold rush in the 80s and 90s, everyone eventually walked away from the unsolved problem.
After twenty years, a scientific revolution, and Belcher's advanced bio-mimicry, Siluria can grow metals and metal oxide crystals on biological templates. (Time travel back to the 80s and try to explain that to frustrated OCM researchers, and you'd be pegged for an visitor from area 51.) The metals coating the virus form a nanotube called a "hairball," which gives the catalyst an increased surface area to limit reactions to temperatures 200 to 300 degrees below current steam cracking methods.
Guido Radaelli, Siluria's vice president of engineering, explained to Chemical and Engineering News that the company had matched the selectivity and conversion results of past efforts. But they'd done it at lower temperatures, much higher pressures, and catalyst lifetimes measurable in years rather than months.
"What is different now," Dr. Tkachenko, a co-founder of Siluria, told the New York Times, "is that Angie's biosynthetic technology allows us to grow these catalysts in a bottom-up synthetic way into novel shapes -- nanowires -- which in turn, allow us to create unique surface morphologies."
Siluria also speeds up the discovery process by using high-throughput screening tools to refine its catalysts. The company claims to have screened about 70,000 catalysts over the last few years, while 80s researchers would have been lucky to do one a month.
Becoming a viable commercial enterprise
The company has been producing ethylene using OCM at pilot scale in its San Francisco for at least three years. At the same time, Siluria also produces liquid fuels in a pilot facility in Hayward, California.
With the two pilots in place, in 2013 Siluria named Ed Dineen the company's new CEO. Dineen, as a former COO at LyondellBasell, one of the world's largest chemical producers, was hired to quickly turn the small startup into a viable commercial enterprise.
Quickly afterwards, Braskem, the Brazilian petrochemical maker, began building a demonstration unit for Siluria at a site in La Porte, Texas. Braskem's support also includes operational services and capital, providing Siluria with $50 million in savings over the life of the agreement.
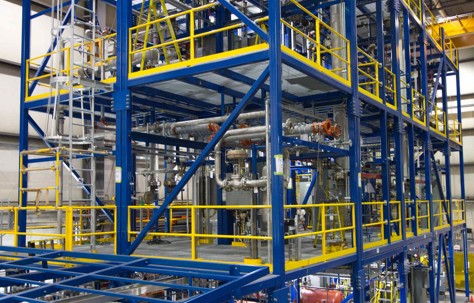
The modular plant will produce 1 ton of ethylene per day once it's in operation. Siluria claims it has a second catalyst that can convert ethylene to liquid fuels such as gasoline, diesel, or jet fuel. Those claims will also be tested at the Texas facility.
Dineen thinks that the mature technology will produce gasoline for about $15 a barrel, plus the cost of natural gas. "As long oil is eight times more expensive than gas, we'll have an advantage," he says. The Hayward facility and the Braskem La Porte OCM demonstration are the last scale-ups steps before commercialization.
Siluria is also partnering with the German engineering firm Linde, a major supplier of steam cracking technology. The companies have formed teams, which integrate their respective technologies and collaborate at the Braskem plant. Afterwards, Linde will market the technology to the ethylene industry.
Far reaching
Because Siluria's processes can be easily added to existing facilities, Dineen plans to pitch improved performance to the 300 ethylene plants around the world. He's also targeting the 600 US gas processing plants to upgrade their products. Obviously, with Saudi Aramco as the first example, China and the Mideast could use Siluria's technology too. Finally, Dineen likes to point out that the "140 billion cubic meters per year" of natural gas that are currently flared around the world are low-hanging fruit.
"The implications of Angela Belcher's work are only beginning to be realized, and yet the applications already appear to be far-reaching," Evelyn Hu, co-founder of Belcher's two companies, explained about the Lemelson-MIT Prize to MIT News.