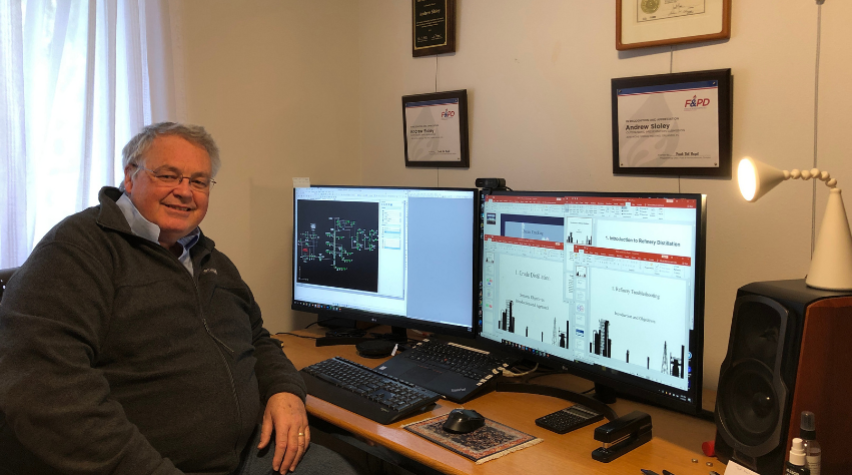
Welcome to the latest in a series of AIChE blog posts profiling process engineers, a diverse group of professionals spanning multiple industries and regions. In this series, we profile process engineers who work in a wide range of fields, including petrochemicals, pharma, bulk chemicals, food, or any process-intensive industry.
Are you a member and process engineer interested in being profiled? We’d love to hear from you via this volunteer opportunity. Please also check out our online discussion group specifically for process engineers. You can find out about these initiatives and join our efforts by visiting aiche.org/process-engineers.
This month, we introduce you to Andrew Sloley, Director at DGI. He discusses the path that led to his career in process engineering, challenges in the fuels and petrochemicals industry, and the importance of his work.
Tell us a bit about your work as a process engineer.
For me, process engineering blends a variety of skills from many different fields. My work has been focused in the fuels and petrochemicals arena, and has included mechanical design of equipment, thermodynamics, economics, statistics, data analysis, and technology evaluation. Very little of it can be done by rote; instead, it requires a deep understanding of how things work and how to balance competing technical and economic objectives.
Effective process engineering requires knowing both the process and the equipment used to implement the process. The process defines the physical and chemical requirements of the transformation.
Over the last 40 years, I’ve worked mainly on complex distillation and separation systems. This spans the range from technology development through equipment design, fabrication, and installation. I've dealt with all the elements of the systems: process sequence, distillation towers, control configurations, fired heaters, heat integration exchangers, reboilers, condensers, associated equipment including pumps and drums, and the detailed design of all parts of these equipment items.
Most of the processes I’ve worked on are refinery crude distillation units; main fractionators and gas plants for FCC units, hydrocrackers, delayed cokers, and visbreakers; refinery light ends units including alkylation and polymerization; and other refinery units including lubricants, aromatics, hydrotreating, sour water, and amine processing.
Intermittently, I’ve also done work that involved steam cracking, electronic chemicals, biofuels, depolymerization and recycling, reactive distillation, and new technology evaluation.
Currently I’m focused on creating and teaching training courses for engineers and plant operators. My courses include Crude Distillation, Plant Troubleshooting, Steam Cracking and Light Olefins, and Refinery Distillation. After four decades in the industry, I’m motivated to share what I’ve learned.
Why did you become a process engineer?
I had no grand vision or sudden revelation about working in process engineering. In my junior year of high school, I decided to become a chemical engineer. It was more a spur-of-the-moment decision than a calculated plan. It didn't involve much thought. After university, my concept of the work shifted from engineering with chemistry to engineering with processes. Fortunately, I liked the work, and I was also good at it.
Then came the early 1980s, which were brutal for the process industries. Consolidations and cutbacks were common. Most of my fellow students from university as well as the cohort of my peers from when I first started working, left the chemical and process engineering field before 1990. Luckily, good fortune favored me. I had a job that continued to provide steady and exciting work throughout that period.
All along, I’ve continuously been learning new skills to apply along with the old ones as the industry changes. The challenge facing engineers today is integrating sensible renewables and low-carbon efforts with existing processes.
What were some of the biggest challenges you faced in your role as a process engineer?
The continuing challenge in process engineering is balancing the economics of investment versus results. This balance largely effects every engineer’s role.
Science is about what’s possible and engineering is about what’s sensible. In this case, sensible means what people are willing to pay. For process engineering, the balance lies between the investment and operating costs versus the product yield (value and rate), all the while considering socially acceptable and legal constraints around safety and the environment.
The continuing challenge in the fuels and petrochemicals businesses, both for fossil feeds and renewables, is getting bulk commodities to market at an acceptable cost. This requires reduced investment, higher capacity, integration of new feeds, reduced emissions and discharges, and improved reliability. The industry is making ongoing attempts to incorporate renewables into fuel processing. Bio-renewables have attracted most of the effort, but their viability remains an open question.
Recently, I’ve become involved in the quest for sustainable plastics by way of technical support for depolymerization processes. Feeds such as polyethylene (polyethene), polypropylene (polypropene), or polystyrene are depolymerized back to monomers or shorter chain molecules. This helps to close the recycling loop and reduces waste plastics in landfills. Improving the operating reliability of these processes is extremely challenging but it also provides great personal satisfaction.
How is your work as a process engineer critical to your particular job assignment or industry?
I think my current work in both training and consulting adds great value to the industry. The average age of engineers working in fuels and petrochemicals continues to increase. Recruiting new engineers to an “old” industry is challenging. My training courses give me the opportunity to pass along some of my experience to a new generation of professionals as well as to plant operators. Modern plant operators are required to know so much more than their colleagues of yesteryear. They need a solid understanding of both the processes and the equipment they operate, and I feel I can contribute.
For the fuels and renewable industries, process engineering is critical. Our work transforms a feed to desirable products that improve the quality of everyone’s life.
My own work involved processes based more on physics (thermodynamics, distillation, energy efficiency, separations) than on chemistry.
Effective process engineering requires both knowing the process and selecting (or designing) the equipment to implement the process. The process defines the physical and chemical requirements of the transformation. Equipment capability defines what a piece of equipment can do—and what it can’t. Good process engineering designs a set of processes, then selects equipment capable of implementing the process requirements, or at least equipment with capabilities that substantially overlap the requirements of the process. I like to think I’ve been successful in this.
What do you think was most important about what you did as a process engineer?
The fuels and petrochemicals industry that I have worked in for decades doesn’t enjoy much public favor. But it is and will remain central to our lives for decades to come. In these large industries, even small improvements have dramatic benefits. For example, even a 1% improvement in the energy efficiency of a large refinery unit saves more energy, and reduces environmental impact more, than anything else does except perhaps the largest modern renewables plants.
I’m proud to say that I’ve helped build and operate many more-efficient units. My work on improvement projects over the years, as well as the training I continue to provide for engineers and operators, has played a part in improving operations in many plants, and consequently in improving life for everyone.
Connect with Andrew on AIChE Engage
Join the Community of Process Engineers
Process Engineer Perspective Talks (PEP Talks)
AIChE has launched new series of virtual presentations called Process Engineer Perspective (PEP) Talks, which will feature perspectives of process engineers on topics relevant to other process engineers. Join us every second Thursday of the month to get to know your fellow process engineers. Attendance is free.
The Community of Process Engineers is brought to you by Scott & Karen Love. Their support enables the AIChE Foundation to advance process engineers at every stage of their career allowing them to Do a World of Good.
AIChE Foundation – Doing a World of Good Campaign