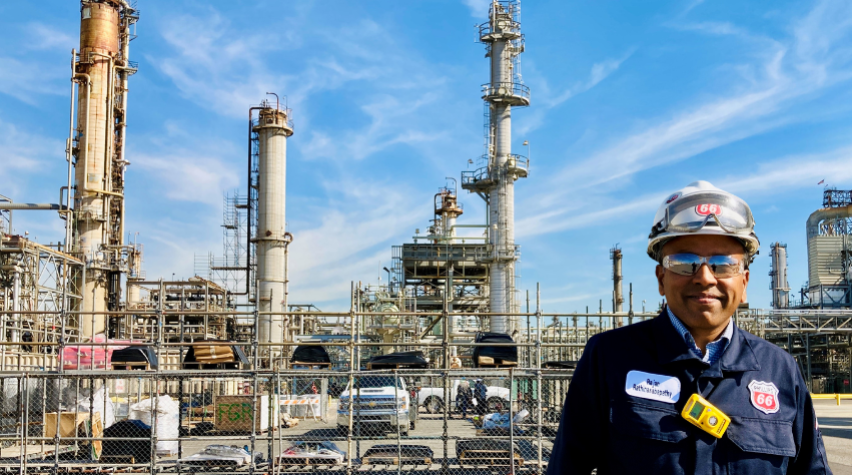
Welcome to the latest in a series of AIChE blog posts profiling process engineers, a diverse group of professionals spanning multiple industries and regions. In this series, we profile process engineers who work in a wide range of fields, including petrochemicals, pharma, bulk chemicals, food, or any process-intensive industry.
Are you a member and process engineer interested in being profiled? We’d love to hear from you via this volunteer opportunity. Please also check out our online discussion group specifically for process engineers. You can find out about these initiatives and join our efforts by visiting aiche.org/process-engineers.
This month, we introduce you to Rajan Rathinasabapathy, Process Optimization / Process Control Engineer at Phillips 66. He discusses the path that led to his career in process engineering, overcoming challenges, and the importance of his work.
Tell us a bit about your work as a process engineer.
I started my career as a unit engineer at Bharat Petroleum, Mumbai, but was also trained as a field operator and DCS operator for contingency purposes. This helped me achieve a solid foundation in process and optimization. After my time at Bharat Petroleum, Mumbai, I went back to grad school (UCLA) to learn newer technologies to solve challenging issues in process engineering.
As a research student, I built a diagnostic localization prototype to diagnose process faults. I went on to become an advanced process control (APC) support engineer at Honeywell. There, I learned and supported APC for a wide customer base of oil-sands, refining, fertilizers, mining, pulp and paper, semiconductors and more, learning different processes along the way.
Rajan at Royce Hall, UCLA
In my current role as Process Optimization Engineer at Phillips 66 Los Angeles Refinery, I build advanced process control applications (multi-variable model predictive controllers) and inferential models for various refinery processes to optimize the units resulting in additional benefits. To perform my job successfully, it requires integrating a variety of skills such as chemical engineering, process engineering, data analytics, controls, modeling, programming, and IT, as well as working with a wide variety of experts that include but aren’t limited to operators, cross-functional team of engineers, researchers, and vendors.
Listening to webinars, reading industry magazines, being an active member of the AIChE Engage community, and continuous learning helps to broaden my perspective, and truly helps make a difference in my work.
Identifying the right optimization opportunities and automation objectives is more critical than automation itself, placing us process engineers in the driver’s seat, as domain experts.
Why did you become a process engineer?
I grew up in Sivakasi, India, a small town filled with cottage matchbox and fireworks manufacturers. My family operated a matchbox business, and I was always surrounded by different chemicals like sulfur, phosphorus, potassium chlorate, wax, etc. Chemical engineering was a natural choice for me due to my early exposure to different kinds of chemicals along with my interest in math.
As a chemical engineering intern at a heavy chemicals plant, I found the process work to be very exciting, easy to follow, and a lot of fun. My internship led to my first job as a process engineer in a refinery. Eventually, my interest in process engineering evolved and encompassed related fields of process control, APC, modeling, optimization, process automation, data analytics, fault detection and diagnosis, and incident investigations.
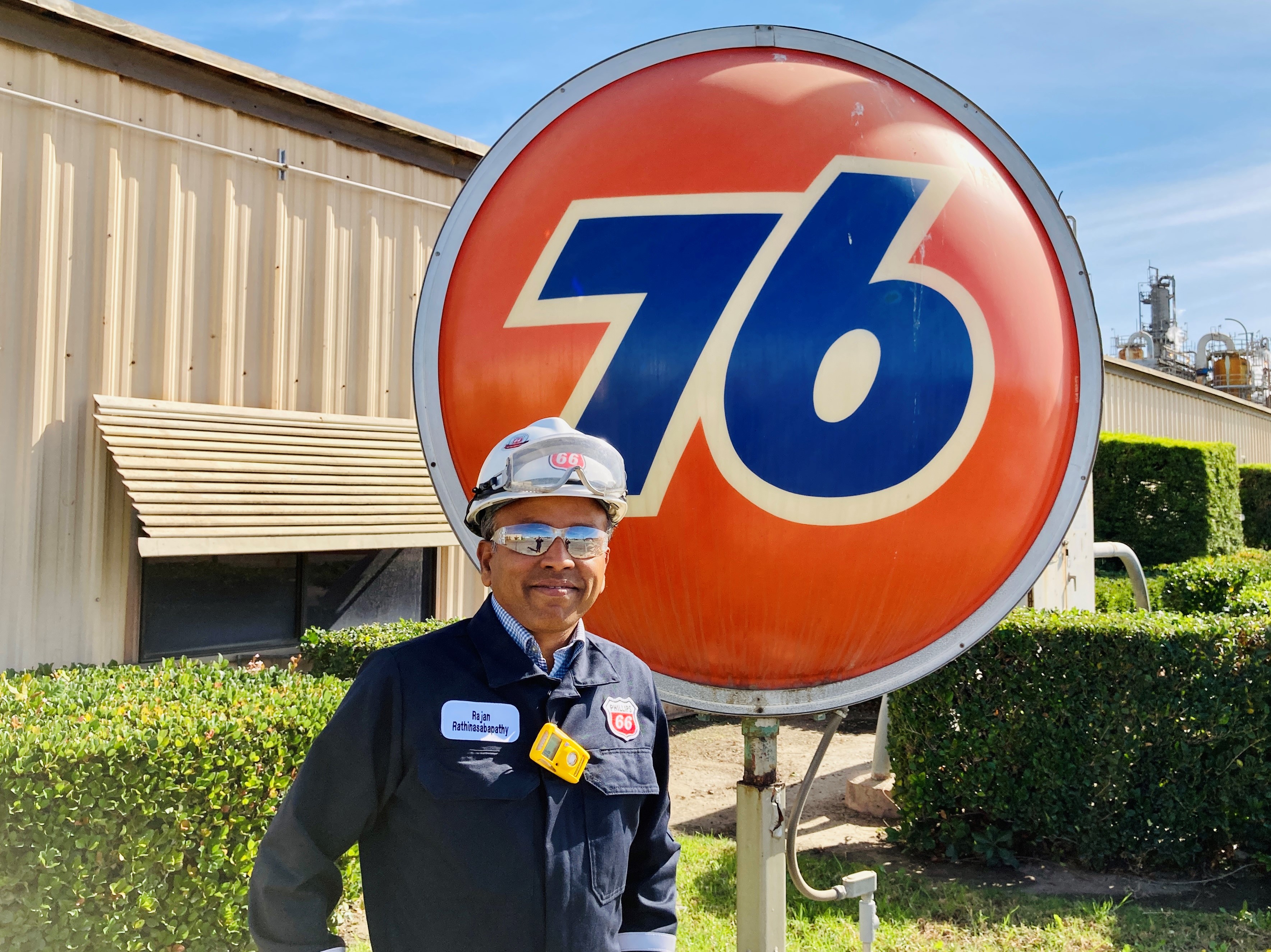
What were some of the biggest challenges you faced in your role as a process engineer?
Almost all my work is data centric and relies on good, clean process data. A big challenge I often come across is that the good quality data needed to model or diagnose an issue is not always readily available. The availability of the right instruments at the right location with the right data quality is a challenge, especially in legacy sites. Incomplete or incorrect data can lead to poor modeling and prolonged investigation with incomplete diagnosis and resolution.
It is important to create the good quality data that we need by testing the process, ideally in a controlled operating environment, taking samples that we don’t typically take and spending a good amount of time cleaning the data.
Another process data challenge is bringing all the different types of data together. There are different types of process data, fragmented and scattered in different places – for example, P&IDs, data sheets, design manuals, LIMS, data historians, DCS, operator logs, PLC logs, field activity logs, miscellaneous excel sheets, and control narratives – and sometimes the data only exists in someone’s memory. Bringing the data together is a challenge, but necessary. When brought together, the results are rewarding.
Another data challenge is the extensive number of variables and their interaction in the real world. There may be unmeasured disturbances or activities, and the available data can be deceiving or lead to unexpected and surprising correlations with baffling causes and effects. The experience, tools, and the current data don’t always help right away.
A deep dive is needed for these challenges, which help us learn even more about the subject. Situations like these present the need to consult SMEs from different backgrounds, test the process units to generate new data, analyze and verify different theories, and solve new problems. This definitely keeps our work interesting.
Identifying the next big optimization opportunity is another big challenge. Small problems can lead to big returns, but the challenge is unearthing them, which may require more of an artistic approach than technical. Sharing knowledge, mentoring, training young engineers and operators, working with interns, etc. are all efforts that have helped me uncover new perspectives, new ideas, and new opportunities.
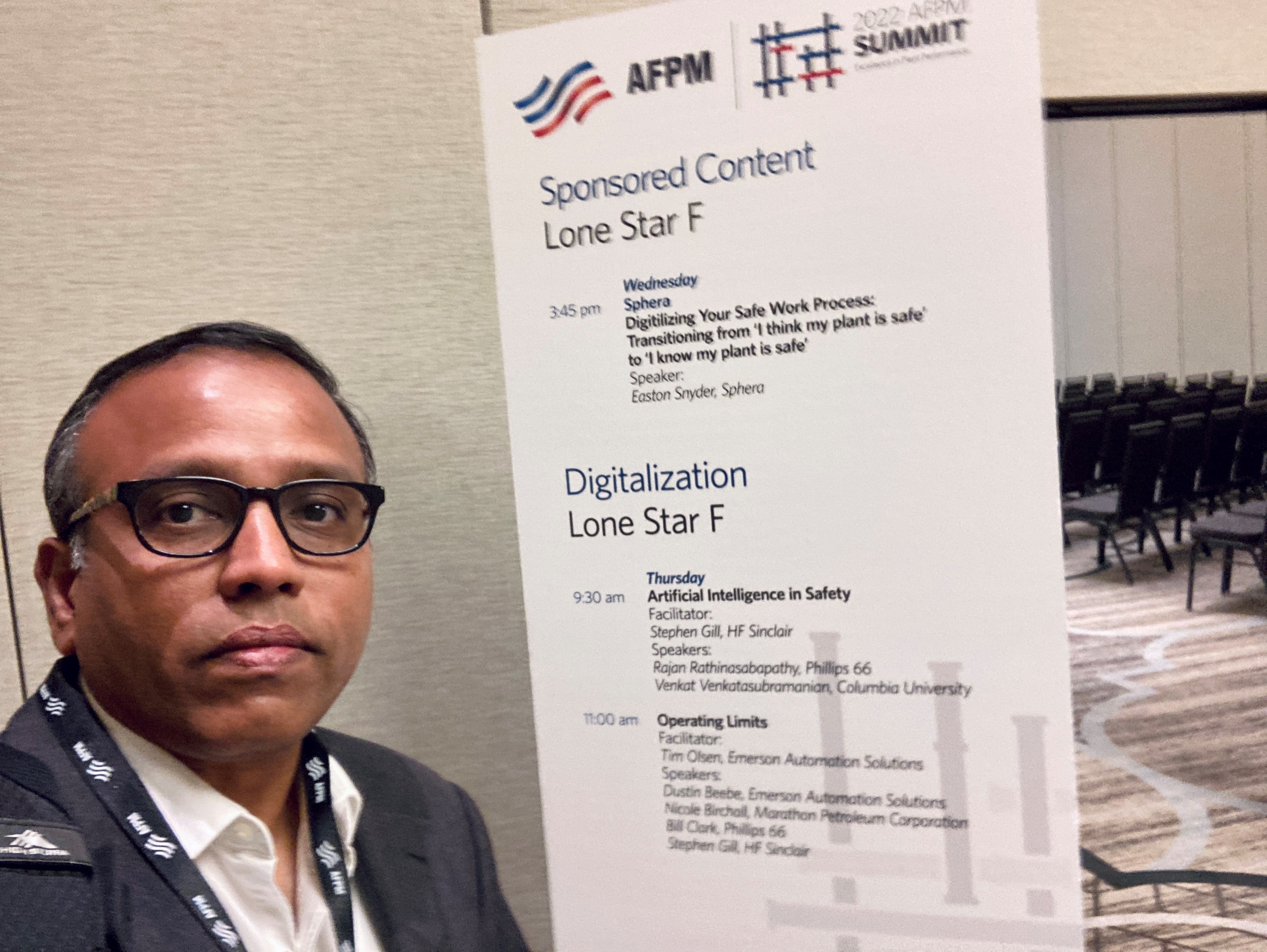
How is your work as a process engineer critical to your particular job assignment or industry?
Process optimization helps in an efficient process, reducing energy footprint, reducing process variance, and improving production rate and product quality, resulting in economic benefits and other non-tangible benefits. A process needs to be well understood comprehensively – including field operations – to be effectively controlled and optimized, even when there are ongoing disturbances to the process.
As a process optimization engineer, I play a critical role in identifying process optimization opportunities, testing the unit, verifying the opportunities, and modeling the process. Hands-on process control skills help to distinguish what’s possible vs. practical vs. sustainable and help to automate the identified big opportunities. These efforts are not just about economics. I am proud that with my work, I help the unit operation to be safe, reliable, and energy efficient with reduced emissions, helping the environment.
APC is a no-capital (except for the software and engineer cost), high-return investment. The big process improvements we make with little to no capital exemplifies the critical work we do.
What do you think is the most important about what you do as a process engineer?
Identifying the right optimization opportunities and automation objectives is more critical than automation itself, placing us process engineers in the driver’s seat, as domain experts. Building an APC controller is easy, but building a reliable and sustainable APC controller is very challenging. Without a good working controller, operator confidence is eroded, and the applications get turned off, which results in losing the optimization opportunity entirely.
Identifying the right process optimization opportunity, modeling only the right/required variables, and building a simple and easily understandable controller are key to reliability and success. Operator awareness, engagement, and continuous training make the success sustainable, creating value by combining process, data, and automation skills in improving processes.
Connect with Rajan on AIChE Engage
Join the Community of Process Engineers
The Community of Process Engineers is brought to you by Scott & Karen Love. Their support enables the AIChE Foundation to advance process engineers at every stage of their career allowing them to Do a World of Good.
AIChE Foundation – Doing a World of Good Campaign