Reboilers, particularly those that use inlet steam control (ISC), can suffer from control and maintenance issues related to condensate backup. Observe these key design considerations to help debottleneck underperforming reboilers.
Reboilers that use an inlet steam control (ISC) valve arrangement can significantly improve the economics and control of certain distillation tower installations, particularly those with short time constants or broad load variability. ISC valve systems are intended to expose the full surface area of a reboiler to steam for effective heat transfer, which enables operation at lower steam pressure. Operation at lower pressure can reduce fouling, as well as corrosion that occurs when tube bundles are flooded. ISC valves improve control by enabling rapid adjustment of steam pressure to match process demand changes. The alternative, an outlet condensate control (OCC) valve arrangement, slowly varies the condensate liquid level to adjust the amount of reboiler surface area heated by steam (1).
To achieve economic and control benefits, reboilers with ISC valves have to overcome potential operational pitfalls that can create bottlenecks in the system’s drainage and hinder process operation, including:
- insufficient pressure to discharge condensate into the return header upon startup, under low demand, or when the tube bundle is relatively clean
- design uncertainty regarding the reboiler drainage system (e.g., specifying the steam trap, pump/trap, level pot/control valve combination, or electric pump)
- insufficient understanding of balance requirements for level pots or pump/trap reservoirs that can cause reboiler evacuation issues, such as stall, backup, hammer, and corrosion.
Reliable reboiler systems require timely, almost instant condensate drainage from the steam space (Figure 1). Reboilers equipped with ISC and OCC valves have been known to experience condensate backup that can lead to corrosion, tube bundle damage, and condensate sewering (i.e., condensate discharged to the sewer rather than the condensate return). These issues may occur in both horizontal and vertical reboilers. In addition, horizontal systems are prone to channel head gasket leaks.
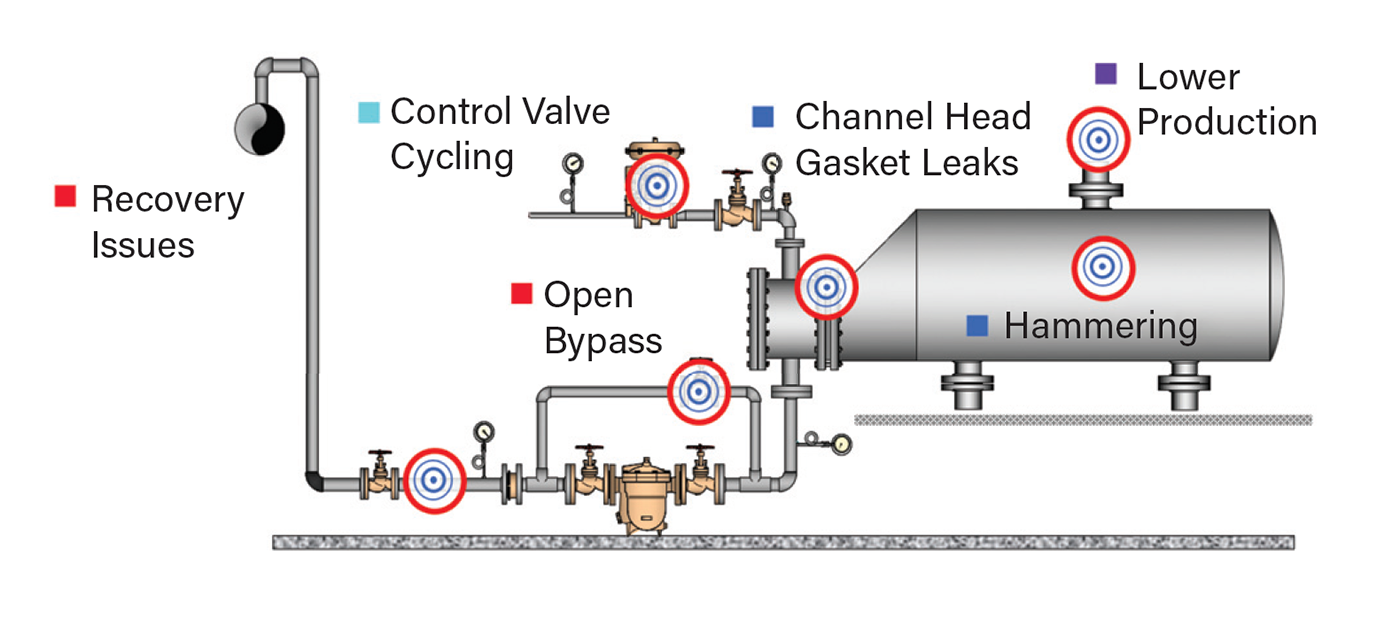
▲Figure 1. Reboilers that are improperly drained can experience multiple reliability issues, which can create system bottlenecks
Many of these problems can be avoided or mitigated through proper condensate drainage design. Reboilers that experience operational issues have often been improperly designed or installed, requiring corrective action to realize improvement. This article explores some reboiler operational issues related to condensate drainage, evaluates why certain problems occur, and provides key design considerations necessary to optimize reboiler performance.
Would you like to access the complete CEP Article?
No problem. You just have to complete the following steps.
You have completed 0 of 2 steps.
-
Log in
You must be logged in to view this content. Log in now.
-
AIChE Membership
You must be an AIChE member to view this article. Join now.
Copyright Permissions
Would you like to reuse content from CEP Magazine? It’s easy to request permission to reuse content. Simply click here to connect instantly to licensing services, where you can choose from a list of options regarding how you would like to reuse the desired content and complete the transaction.