(45c) Multi-Scale Modelling of a Structured ZoneFlowTM Reactor Coated with a Rh-Doped Ni Catalyst for Steam Methane Reforming
AIChE Annual Meeting
2022
2022 Annual Meeting
Catalysis and Reaction Engineering Division
Multi-Scale Modeling
Monday, November 14, 2022 - 8:36am to 8:54am
Steam methane reforming is the most widely practiced process for production of hydrogen and syngas. The endothermic reactions are carried out in a multi-tubular fixed bed reactor, facing limitations related to heat transfer, pressure drop and intra-catalyst diffusion. The structured ZoneFlowTM reactor is an annular reactor offering lower pressure drop and significantly better heat transfer performance than standard pellets. A multi-scale one-dimensional heterogeneous model of the reactor is developed using scale-bridging strategies and is validated experimentally. The intrinsic reaction kinetics of a commercial Rh-doped Ni catalyst coating is measured in a specifically designed micro-packed bed reactor. The Langmuir-Hinshelwood-Hougen-Watson approach is adopted to derive rate equations and the parameters are estimated by non-linear regression. The intra-catalyst diffusion limitations are accounted for using a pseudo-continuum description of the thin coating. The pressure drop and heat transfer coefficient between the tube wall and the gas are measured in a 1 meter long reactor under cold and hot flow inert conditions, with air flow rates ranging between 70 and 330 Nm3/h and furnace temperature between 100 and 500°C. Correlations for the friction factor and the Nusselt number are derived and the parameters estimated using non-linear regression. Thermal conduction in the ZoneFlowTM structure is modeled using a correlation derived from 3D numerical simulations and radiative heat transfer is accounted for. The developed reactor model is coupled with independently measured intrinsic kinetics and finally validated using data from steam reforming pilot plant tests. A 4 m long reactor is suspended in an electrical furnace and experiments carried out at 8 and 28 barg, with natural gas flow rates from 10-25 Nm3/h and steam-to-carbon ratio from 2-3. The rigorously validated model is finally used to perform reactor optimization and scale-up and the performance is discussed and compared with that of a conventional packed bed.
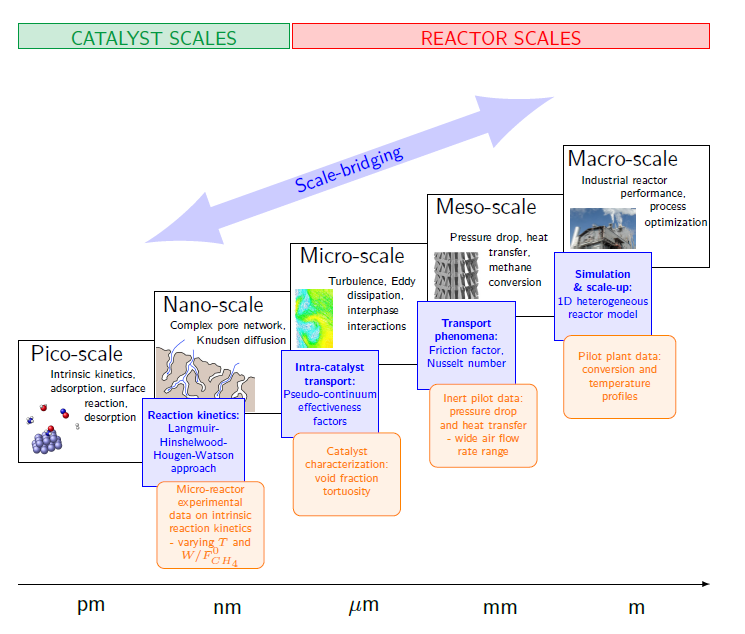
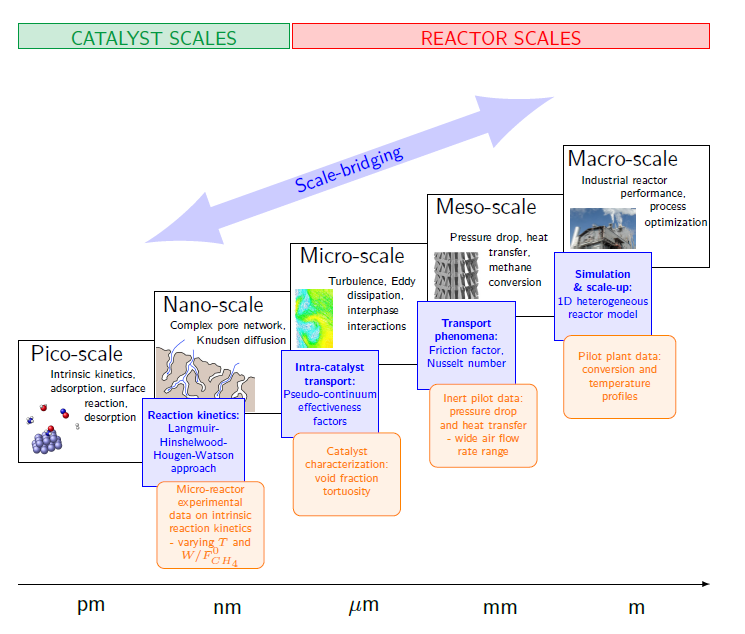