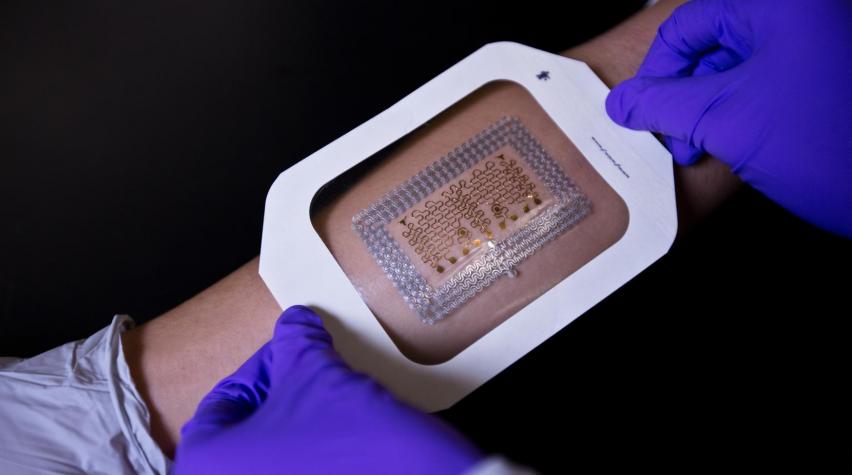
A team of researchers has invented a new method that reduces the manufacturing time of wearable electronic health monitors from several days to 20 minutes.
Led by Assistant Professor Nanshu Lu at the Cockrell School of Engineering at The University of Texas at Austin, the team’s work is a repeatable “cut-and-paste” method that should prove compatible with roll-to-roll manufacturing, which is used for creating devices from a roll of flexible plastic.
The great promise of the devices is that if inexpensively made, they will allow patients to use them more frequently, potentially catching more heath issues earlier.
How the manufacturing works
Unlike the current methods, the UT team’s methods do not require a clean room, wafers and other expensive equipment. Rather, they rely on freeform manufacturing, which is similar to 3-D printing but is a process in which material is removed, instead of added.
Pre-fab, industrial-quality metal on polymer sheets are first cut with an electronic mechanical cutter to create patterns on the sheet. Unneeded metal is then removed, and the electronics are printed onto a polymer adhesive.
Cheaper manufacturing and better results
In tests the researchers conducted, the patches picked up stronger body signals than existing medical devices, including an ECG/EKG. The team also found that their patch conforms almost perfectly to the skin, minimizing motion-induced false signals or errors.
For more information about these wearable electronics and the researchers’ work, see the UT press release.