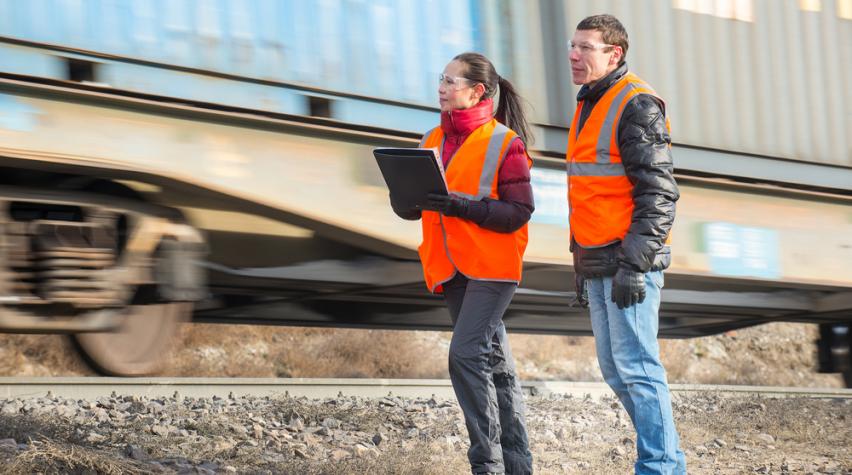
Every chemical engineer knows that seemingly small mistakes or temporary lapses in judgment can have serious consequences.
Young professionals can be especially prone to error because we lack industrial experience, yet want to prove ourselves professionally. Many of us enter the workplace with a sense of infallibility, secure that our college education has endowed us with the ability to think quickly and rationally, and jump into any team, plant, or project. Eventually we learn that maintaining a sense of vulnerability is key to avoiding process safety incidents.
For some of us, the opposite is true — we believe that, as rookies, we don’t have the prerogative to speak up if we feel that something is unsafe. Overcoming our fear of confrontation and learning how to identify and speak up about unsafe practices or conditions will not only make us better engineers, it may save lives.
In this column, four experienced, successful chemical engineers share some mistakes that they made at the start of their careers, to show how even the most rational decisions and actions can result in process safety incidents and near misses.
How can you apply the lessons learned from these incidents in your career?
Lesson #1
What works in the lab won’t always work in the plant
Kathleen Kas, P.E.,
Process Safety Expertise Leader,
The Dow Chemical Company
At a previous employer, a new agricultural intermediate process was running at a scale of 6,000 gal for the first time. The process included a water wash of the organic phase, followed by a phase separation to remove salts from the batch.
Unfortunately, the batch had formed an emulsion and the phases would not separate. This problem had occurred a few times in the lab, and had been remedied by the addition of potassium carbonate salts, which increased the density of the aqueous phase and broke the emulsion. I took a sample from the commercial vessel, brought it to the plant lab, and added potassium carbonate, and the phases separated.
The issue occurred during the midnight shift, when experienced staff members were not available and resources were limited. I decided to try the solution that had worked so well in the lab to break the emulsion so that the batch could proceed. I instructed the operator to open the manway of the vessel and add several bags of potassium carbonate.
Shortly after the material was added, the batch began to swell and material started to “burp” out of the top of the vessel. The operating staff retreated to a safe distance as the material oozed along the floor, then solidified due to the cooler ambient temperature. It took the crew hours to shovel the material off the floor.
Lessons learned: I did not take into consideration the differences between operating a process at the lab scale and at the plant scale. In this case, the mixing in the commercial vessel was less efficient than it was in the lab-scale vessel, so, when the salt was dumped into the commercial vessel, it went straight to the bottom. Large carbon dioxide bubbles then formed at the bottom of the vessel, forcing material up from the top. This had not been observed at lab scale because of better mixing and slower addition of the salt.
What should you do?
1. Understand the fundamentals of scale-up. Parameters such as mixing and heat transfer change as a process is scaled. It is important to take those changes into consideration when designing different-sized processes.
2. Conduct a management-of-change review. The practice of adding salt to break the emulsion had been practiced in the lab, but not reviewed at the plant scale. Because the event occurred during the midnight shift, expert input that would likely have identified the potential for this type of event was not available, and a decision was made to proceed rather than to wait until technical experts could review the change. Avoid troubleshooting and creating procedures “on the fly,” because there may be unforeseen consequences.
Lesson #2
Ensure that supply is off before disconnecting the hose
Tim Olsen,
Technical and Business Consultant
Emerson Automation Solutions
Early in my career, I learned process operations on pilot plants. At these plants, the air and nitrogen supply hoses were connected with a quick-connect fitting, so that disconnecting the hose automatically shut off the supply.
Shortly after training in the pilot plants, I was transferred to a refinery and asked to help load catalyst on two reactors. Nitrogen was used to spin the catalyst loader and prevent air from poisoning the catalyst. Unfortunately, the nitrogen hose was connected to the catalyst loader with a universal Chicago-coupling-style fitting, not a quick-connect.
Once the catalyst loading was completed, I disconnected the 100-psi nitrogen hose from the loader, thinking the connection would be automatically shut off. Because the connection did not shut off, the nitrogen hose began whipping around violently. The hose could have easily hit someone and injured any one of the 20 people who were on top of the reactor with me. There was no place to hide to avoid the whipping hose.
Eventually, one person pinched the hose to prevent it from injuring anyone (which itself was an unsafe action) while someone else turned the source off below. No one was hurt, but this was a near miss.
Lessons learned: Even though this was a near miss with no injuries, we still had to file a safety report. My word of advice, similar to lockout-tagout procedures, is to make sure that the source is turned off before disconnecting any auxiliary supply connection such as nitrogen or air. Also, realize that pilot plants are smaller in size, so equipment and asset functionality can be different than they would be in a full-scale commercial processing facility.
Lesson #3
Make accident prevention part of every design phase
Amanda Scalza,
Production Manager
My passion for safety began during my first few weeks as a full-time engineer, when I caused an accident. My coworker and I had been tasked with working on a fermentation-filtration experiment skid, which held about 50 gallons of fermentation broth. We were using the skid to test the ability of a filter to separate solids from the broth. We set up the system and secured the lines, then started up the pump. Liquid quickly started shooting out at high pressure, and we realized that a line had been disconnected. We fished through the slippery fermentation liquid and hit the emergency stop button, preventing further loss of containment.
At least 20 gallons had been released into the lab, and had already started to flow down the drain into the sewer. I instantly worried that this fermentation broth might still contain alcohol, and that it could harm the public water supply or even pose a fire hazard. No safety datasheet (SDS) was available, so the team decided that this was a safe method of disposal. I was lucky that all I had to worry about was a long day of cleanup. The company I worked for did not have a near-miss reporting system in place, so the situation was hardly noticed. This also meant that others in the organization lost an opportunity to learn from my mistake.
Lessons learned: The situation occurred because of inexperienced operators and because we failed to do a full system review or walk-through prior to startup. The system designer, however, was successful in his thoughtful placement of the emergency stop buttons.
Process engineers, product designers, and researchers all have an important responsibility in preventing accidents. It is vital to design with the operator at the forefront of every decision to create a successful process or product. It is equally important to ensure that the operators understand how to operate the equipment, and know what to do if it fails.
Lesson #4
Don’t be afraid to speak up
Mike Moosemiller,
Sr. Principal Consultant
BakerRisk
A reboiler on a distillation column was being removed for maintenance. Its removal required two maintenance people to work on an elevated deck to knock out bolts from the flange on the column to free the reboiler. The flange, which weighed several tons, could come free and fall onto the workers, so its weight was supported by a crane.
I was not associated with this operation, and had only been working in the refinery — my first — for two weeks.
I was watching from a distance while several plant supervisors were next to the crane operation. Although I knew nothing about crane operations, it seemed odd that the crane was pulling so hard on the flange that its rear tires were off the ground. (The nearby plant supervisors were facing away from the wheels and may not have known that they were elevated.) Because I was the least experienced person observing the operation, I continued to watch, but did not engage the plant staff about whether the crane operation was proper.
Once all but two of the bolts that held the flange in place were removed, the final two bolts sheared due to the stress of the highly torqued crane. The flange flew up in the air and landed on the backs of the workers who had turned away from it, knocking them to the deck. The flange rebounded and came back down just as one of the workers had staggered back to his feet, hitting him again. The workers were subsequently taken away by ambulance to a hospital, and, fortunately, did not sustain serious injuries.
Lessons learned: If something doesn’t seem right, then there is a reasonable chance it isn’t — even if everyone else seems comfortable with it. Don’t let your seniority blind you to what is wrong or your lack of experience prevent you from speaking out if something doesn’t look right. If something isn’t right, it isn’t right whether you are an employee of the facility or not. Speak up!
This article appears in the November 2017 issue of CEP. Memebers can read teh current issue and find years of back issues in the archive at www.aiche.org/cep