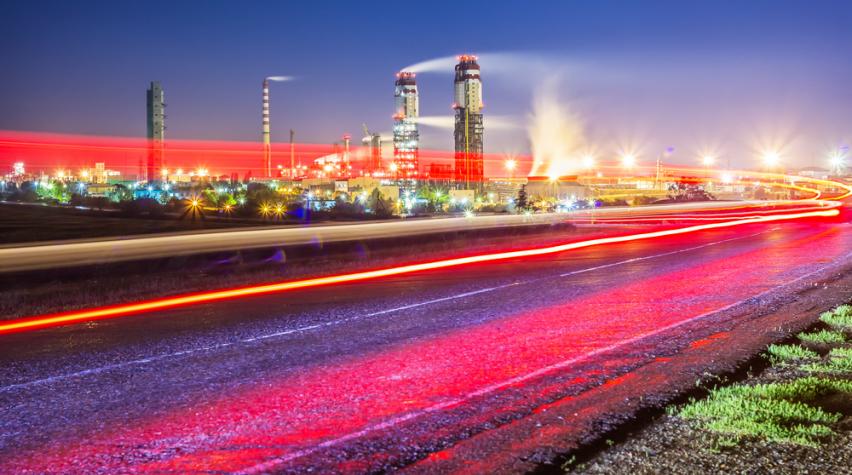
This article originally appeared in the November/December 2018 issue of the Nitrogen+Syngas magazine.
The annual Ammonia Safety Symposium is organised by AIChE’s Ammonia Safety Committee and is dedicated to improving the safety of plants that manufacture ammonia and related chemicals, such as urea, nitric acid, ammonia nitrate, and methanol.
Attendees, including plant safety personnel, plant managers, and process engineers representing a spectrum of nitrogen-fertilizer-based industries, all participate in the symposium, where they share technological advances and discuss strategies for improving plant safety, maintenance, and management. Ammonia industry leaders and practitioners describe how their organisations avoid or manage potential plant accidents, and present solutions to a variety of safety engineering problems.
This year, from September 16th to 20th, 400 delegates from more than 30 countries and 120 companies attended the 63rd Ammonia Safety Symposium at the Sheraton Centre in Toronto, Canada. The Toronto weather was ideal for outside activities and encouraged many people to visit Niagara Falls, 120 kilometres away. Haldor Topsoe’s outing also included a boat ride on Lake Ontario, which gave people a close-up view of the Canadian National (CN) Tower and views of the Toronto skyline.
The alchemy of air
The keynote speaker, Thomas Hager of the University of Oregon and the author of a book called The Alchemy of Air, described how, in his words, “three men turned a table top prototype into a city-sized factory in just four years.” The speech attracted a lot of interest among the audience as it recapped the history of the invention of synthetic ammonia production. Tom described how Fritz Haber and Carl Bosch were the two chemists who invented the ammonia process, a way “to turn air into bread,” built factories the size of small cities, made enormous fortunes, helped engineer the deaths of millions of people, and saved the lives of billions more. The third of the trio was Alvin Mittasch, who helped to develop the catalysts for the reaction.
Tom – and the global ammonia industry – believe this was the most important discovery ever made. One can’t think of another that ranks with it in terms of life and death importance for the largest number of people. In the simplest terms, their discovery keeps alive nearly half the people on Earth. Most people do not know the names of either the men or their invention, but we should thank them every time we take a bite of food.
Their work lives today in the form of giant factories, usually located in remote areas, that drink rivers of water, inhale oceans of air, and burn about 2% of all the world’s energy. If all the machines these men invented were shut down today, more than two billion people would starve to death. Think of it this way: inside your body, every protein molecule, every cell, and every stitch of DNA includes atoms that are there because of this invention. Half of the nitrogen in your body is synthetic, the product of a Haber-Bosch factory.
Tom dived deeply into the history, and said that 80% of the atmosphere around us is nitrogen, but we cannot use a single atom of it. We breathe it in and out all day long without incorporating any of it. Atmospheric nitrogen is inert, a dead molecule, because it exists in the form of two N atoms very tightly bound to each other with triple covalent bonds. In this form, the nitrogen is unavailable for use by living organisms (with the exception of a few groups of bacteria).
To get into our bodies, to nourish us - and nitrogen is essential for nutrition; it is the fourth most common element in our bodies; proteins and nucleic acids depend on it - the atmospheric nitrogen must be "fixed," the two N atoms torn apart and reforged into new molecules with other elements, mostly oxygen, carbon or hydrogen. Nitrogen fixation is a difficult, energy-intensive, and critical process. Haber and Bosch figured out how to do it at an industrial level in 1913.
The same basic process they discovered 105 years ago is used today in scores of huge ammonia plants around the world that produce a flood of synthetic nitrogen fertilizer. That fertiziler feeds the crops that feed the animals that feed you. Thanks to the Haber-Bosch factories, a bit of the almost limitless supply of natural nitrogen from the air is purified, processed, chemicall altered, made into fertilizer, and eventually ends up on your plate. That's why half the nitrogen in your body is synthetic.
The work of Haber and Bosch changed the chemical industry. Haber-Bosch turned Malthus on his head. Haber-Bosch is the reason our grocery shelves (in the US, at least) are groaning, more people aren’t starving, and we are able to have a population explosion at the same time as an obesity epidemic.
Safety
The key safety related papers were:
Failure of HP boiler feed water pump
A catastrophic failure occurred in the main high-pressure boiler feed water pump train in an ammonia plant. The direct cause of the failure was flow reversal from the boiler feed water system and/or the steam drum, to the turbine driven high pressure boiler feed water pump. The paper presented the sequence of events and associated root causes that resulted in the failure of the pump as well as recommendations to prevent a re-occurrence. The consequence of failure of a high-pressure BFW pump train can be significant in certain situations. Safeguards for existing systems and procedures governing pump operations should be evaluated in light of this incident.
Hot spots in refractory lined equipment
Refractory lined equipment is typically used in high temperature processes in the chemical processing industry. Degradation of refractory over time commonly leads to the development of hot spots at the pressure boundary, which may present a serious risk to the structural integrity of the equipment and can even lead to a catastrophic failure. Significant hot spots were detected on the refractory lined outlet piping system of a steam methane reformer (SMR) plant.
Extensive fitness for service analyses were performed to study the impact of hot spots on the structural integrity of the piping system and to establish the safe operating limits. External cooling was applied to control the piping temperature. Rigorous temperature monitoring and inspection procedures were implemented to ensure the plant was operated within the safe limits established by above analysis.
The SMR plant was successfully operated over a year with the presence of hot spots on the outlet piping system until the refractory lined piping was replaced. The successful experience demonstrated that the state of the art engineering analysis, robust monitoring and inspection procedures and a strong culture of operational discipline are essential components for safe plant operation in case an unexpected situation arises.
Rupture in high pressure drain line
This paper highlighted a critical leak incident that occurred in one of the high pressure pipes of the urea plant during an emergency shutdown, and how the situation was analysed to prevent the re-occurrence of similar incidents in the urea plant. Lessons learned were:
- Inspecting and monitoring operating conditions of the high pressure lines periodically are critical to ensuring safe operation.
- Periodically inspect insulation on high pressure pipes to ensure it is in good condition and has good sealing.
- Avoid any source of chloride in urea high pressure lines to avoid stress corrosion cracking.
- Time and money spent on inspection and maintaining the vessel in healthy condition will always be paid back and achieve the goal of preventing accidents and improving safety at the plant.
- Emergency preparedness – an emergency response team (ERT) should be available.
Urea reactor top head and diaphragm failure
During the process of urea production, multiple compounds will form that are highly corrosive to standard metals under existing process conditions. Thus, it is imperative to use the correct materials when constructing piping and vessels. When a leak developed on the head of a high pressure urea reactor in a urea plant, the cause was the failure of the diaphragm that protected the pressure containing reactor bolted head cover. The diaphragm was found to have been constructed with 316 stainless steel, rather than the correct 317L.
The diaphragm corroded and developed a pinhole leak after extended exposure to active corrosion from the top of the reactor. The failure of the diaphragm allowed the carbon steel bolted head cover to be exposed to carbamate, resulting in significant corrosion to the cover. The MTR (material test requirements) from the OEM shop that had repaired the head after the 2010 incident indicated that the diaphragm was the correct grade of stainless steel. Checking the diaphragm with a PMI tester before installation could have prevented the most recent incident.
Over-firing of primary reformer
In early 2015, when an ammonia plant was performing a hot restart, an uncontrolled and rapid increase in flue gas temperature was noticed in the primary reformer. After natural gas feed was introduced to the primary reformer, it was observed that a rupture of several catalyst tubes had occurred and the plant was tripped immediately. The company requested Haldor Topsoe A/S to take the lead technical advisor role in a thorough root cause analysis, performed to identify the reason(s) for the tube rupture incident.
The incident with ruptured tubes not only impaired plant capacity utilization until the re-tubing of the furnace, but more importantly, the leaked gas from the ruptured tube could have resulted in unsafe conditions. Following this incident, an automated over-firing protection (OFP) management system which provides four elements of protection against over-firing of primary reformer tubes was developed.
The over-firing protection management system (OFP) addresses both local and global causes of primary reformer catalyst tube over-heating. The current system does not allow fuel header pressure increase during startup and enforces a symmetric burner ignition pattern. During startup, these two protection elements not only help avoiding catalyst tube overheating but also ensures better heat distribution inside the furnace. Moreover, double protection elements of duty and bridge wall temperatures (BWT) limitation ensure parity in duty input and duty uptake by adjusting fuel flow to the burners based on maximum estimated duty for the primary reformer at a particular capacity.
Reformer post combustion problem
After a plant revamp, poor combustion in the radiant section of the primary reformer was observed largely as indicated by measured carbon monoxide (CO). Flame patterns were irregular, including flickering with visible flame impingement on the reformer catalyst tubes. Apart from low methane conversion, poor combustion in the radiant section was also causing post combustion in the convection section where the oxygen was in excess. The post combustion was raising the convection coils’ temperature too high, close to their operating limits, and thus limiting plant load.
After fabrication and installation of new burners as per the original revamped design, post combustion issues were resolved and provided significant safe operating margins. The reliability and life of the reformer has been improved in terms of lower tube metal temperatures, and elimination of post combustion which could lead to severe failures. A significant gain was also observed in furnace thermal efficiency and methane conversion.
Round table session
On the fourth day of the symposium, a roundtable session covered industry incidents, safety-related systems and the Fertiliser Industry Safety Information Analysis and Sharing Program.
The 2019 Symposium will be in San Francisco, USA, from September 8th to 12th.