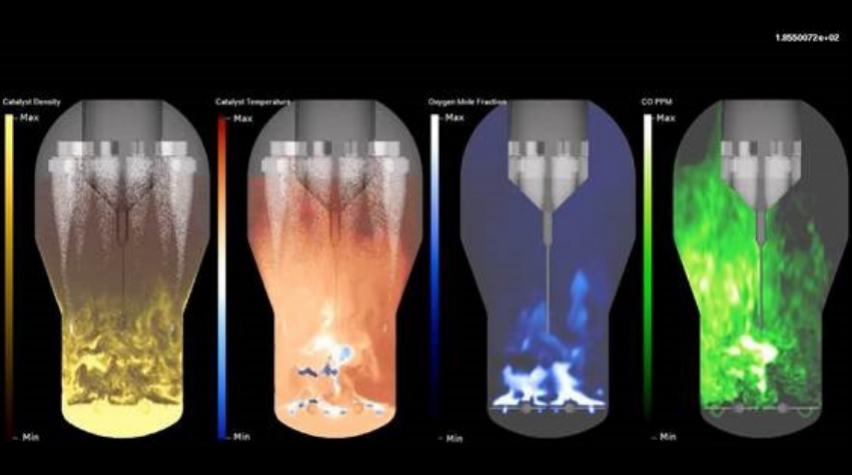
Disclosure: This post is sponsored by CPFD and reflects their views, opinions, and insights.
Fluidization XVI is the 16th iteration in a series of conferences aimed at tackling challenges and successes with the design and operation of fluidized beds and fluid-particle systems. This conference will bring together world renowned experts in the field to help bridge fundamental research on fluidization, emerging applications of fluidization, and novel fluidization technologies. I had a chance to interview Peter Loezos prior to this year's conference to discuss current developments, challenges, and the future of fluidization technology.
What are the most exciting developments you have seen recently in fluidization technologies?
Recent shifts in the refining and petrochemicals market have spurred the development of innovative technologies to meet this changing landscape. Among these shifts are the projected increase in demand for petrochemicals and the relatively slow increase in demand for fuels. As a result, many refiners are pushing FCCU operations towards higher light olefin yields, requiring a revamping of the existing units and the deployment of new technologies to meet these challenges. While nearly all major licensors offer FCC technologies supporting the production of light olefins, novel approaches like the Lummus Technology SRDC (Single Regenerator/Dual Catalyst) platform represent innovative solutions to address these market challenges.
This secondary reactor technology combines novel hardware designs that create an optimal reaction environment while decoupling catalyst/additive functionalities from the primary riser. Through the application of traditional fluidization principles, the unique SRDC hardware can selectively concentrate an additive in the secondary reactor while keeping within all practical design guidelines. Technologies like SRDC represent a wonderful example of traditional fluidization engineering re-imagined to meet the demands of the future. Innovative approaches coupled with industrial know-how combine to develop a truly step-out technology.
Traditional technologies are being adapted to fluidized platforms to capture the inherent advantages of CFB systems. Consistent with the trend towards petrochemicals production, established technologies for the production of on-purpose propylene are facing challenges from processes like the Dow PDH (propane dehydrogenation) process. Supported by catalyst development advances, this process overcomes shortcomings of fixed bed technologies, including the need for multiple reactors, and has potential capital cost advantages. An excellent example of fluidization technology applied to advance traditional approaches.
Innovations in fluidization technology like the Lummus SRDC platform and DOW PDH process demonstrate that there are many new horizons in what some consider to be a mature field. The shifting role of the FCCU will drive new innovations in the field of fluidization, while traditional processes may be re-adopted on fluidized platforms to overcome inherent limitations. By continually pushing the envelope and looking at fluidized technology through unique perspectives, many advances are yet to be realized.
How does CPFD help to solve the challenges in this field?
CFD analysis has proven to be an invaluable tool for helping refiners address evolving challenges in the field. For FCCU revamps geared towards petrochemicals production, the entire circulation loop must be re-evaluated for higher catalyst circulation rates and the impact of changing feedstocks. These evaluations include riser, riser termination device (RTD), stripper, standpipes and regenerator sections. CPFD’s Barracuda Virtual Reactor software is routinely used to successfully mirror the refiner’s current FCCU operation and predict the impact of operational and hardware changes. With higher circulation rates, regenerator residence times will be reduced and vapor/catalyst mixing characteristics altered.
These changes can result in higher CO and NOx emissions with associated afterburn in the dilute phase and cyclone system. Barracuda Virtual Reactor is used to baseline the current regenerator operation and model the impact of proposed modifications on regenerator performance, allowing for successful post turnaround outcomes and avoiding costly shutdowns and rework. The software will successfully predict erosion patterns in the RTD system and identify circulation constraints in the stripper/standpipe design to enable successful modifications. Through the evaluation process, a "digital twin" can be developed, such that changes in operating conditions and hardware can be studied in a rapid and cost-effective manner.
New approaches to meet growing petrochemicals demand will require novel technology development and certainly push the boundaries of current fluidization know-how. CPFD’s simulation tools coupled with our process, fluidization, and industrial experience allow for the cost-effective development of new technology platforms where the inherent risk of scaling up these processes can be mitigated. New designs can be rapidly evaluated using our software, identifying the most promising candidates and appropriate scale for pilot and/or cold flow testing. The effect of scale-up is then evaluated through simulation, coupled with existing pilot and cold flow data, to ensure successful commercialization.
Whether considering modifications for a unit turnaround or the development of a new technology platform, CFD analysis is a critical component to reduce risk and shorten the development timeline/cost. CPFD will provide support through all phases of the project,supplying simulation support and industrial know-how to ensure a successful turnaround or a first-of-its-kind technology deployment.
How do you think the Fluidization conference series can help serve the fluidization community?
The conference series is invaluable in bringing together members of the fluidization community to share their unique knowledge and build collaborations. Holistic advances in technology and know-how can only be made by sharing the experience of researches and industrial professionals. This combined knowledge serves as the foundation from which to advance fluidization technology and address future challenges in a manner that is both innovative and commercially relevant.
You can still register for the 2019 Fluidization XVI conference, taking place from May 26-31 in Guilin, China. Learn more here.
Peter Loezos
Peter Loezos currently serves as Vice President of Operations at CPFD Software LLC with 18 years of experience in the development and commercialization of new processes for the refining and petrochemical industries. Throughout his career, he has worked on the development of a broad range of technologies, including FCC, MTO, desulfurization process, alkylation processes, coking applications and biomass conversion. Previous experience includes technology development roles in ExxonMobil, SABIC and Lummus Technology, where he had a specific emphasis on fluidization engineering. He holds a PhD in Chemical Engineering from Princeton University, where his research included the development of CFD sub-grid models for gas-particle flow applications.
Disclosure: This post is sponsored by CPFD and reflects their views, opinions, and insights.