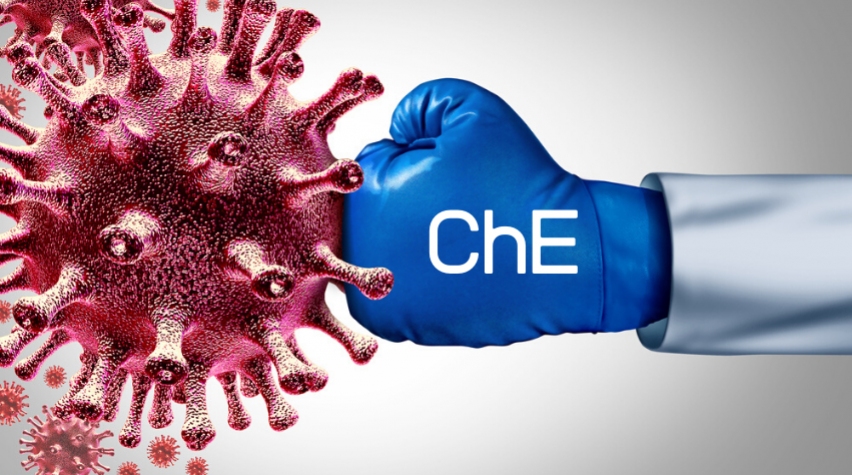
The current COVID-19 pandemic has doubtlessly given all of us reason to reflect on many aspects of our lives. I have thought about friends and family and their well-being during this crisis, as well as the little things we all take for granted, like trips to the grocery store or having dinner in a restaurant.
I have also been considering what makes AIChE so special to me. It is each and every one of you — our members, volunteers, leaders, engineers, scientists, researchers, educators, professionals, and the many others who are diligently working to inspire our safe, connected, and inclusive community — all united to meet society’s current challenge, the coronavirus. There are many stories of these valiant efforts. Here are a few I’d like to share with you.
The project team from our RAPID Manufacturing Institute at the Univ. of Pittsburgh is using their research facilities to make hand sanitizer from donated chemicals. On a large scale, Huntsman is repurposing its coatings and adhesives facility in Alabama, and Dow Chemical re-engineered a plant in Germany to make hand sanitizer, adding to production from BASF, Lubrizol, Arkema, and P&G.
Chemical engineers in labs and plants have donated personal protective equipment (PPE) to medical personnel across the country who have desperate need for it. The Chemical and Biological Engineering Dept. at New York Univ. gave thousands of latex gloves and hundreds of masks to the Brooklyn Hospital Center. AIChE donated 3,000 travel-size bottles of hand sanitizer to Bellevue Hospital’s healthcare workers.
Additionally, RAPID and its members are working to help a team at Clemson Univ. build the supply chain for modular sterilization systems that can be rapidly deployed to medical facilities. 3M is producing 166.5 million N95 masks within the next three months to distribute across the U.S. Chemical engineers at companies such as Carbon and Stratasys are using their 3D printing technology to make PPE.
Our Center for Chemical Process Safety (CCPS) created a list of guidelines for managing process safety in the shadow of the COVID-19 pandemic. Based on the 20 elements of risk-based process safety, these guidelines address manufacturing needs while taking into account the current disruption and threats to process safety and operational resources such as people, materials, and equipment.
Pharmaceutical and biological engineers are also helping produce faster and cheaper diagnostic solutions, repurposing and developing new drugs to treat patients, isolating antibodies against the present coronavirus, and testing new vaccines. Janssen Research & Development and Moderna are accelerating the development of potential vaccines, while a team at the Wyss Institute is developing a surrogate non-COVID coronavirus for use in studies.
Meanwhile, services companies such as Ginkgo Bioworks and Twist Biosciences have offered their platform to help support technology development. And universities are putting research on hold and shifting their focus to COVID-19. In the upcoming May CEP, you can read an article that describes such work underway at Rensselaer Polytechnic Institute (RPI).
These are just a few examples of AIChE’s aspiration of chemical engineers Doing a World of Good. We can all be very proud of how our profession is working tirelessly to help solve this current crisis.
As we look for a resolution to this situation, while we all practice social distancing, it is my wish that each and every one of you stays safe and healthy.
This post is adapted from the guest editorial for the upcoming May Issue of CEP Magazine. You might also consider reading Cindy Mascone’s editorial for the April issue.
Comments
June, One more item to add to your list of chemical engineering contributions was from a married couple in Columbus, Ohio having a family dinner conversation (probably best to google "Kevin Hommema" for details). Kevin Hommema, Engineer in Principal Research with Battelle Memorial Institute, and his wife Dr. Laurie Hommema, Family Physician with Ohio Health Hospital Network, were having a dinner conversation. Dr. Hommema was telling her husband about her workday and how they were experiencing a shortage of N95 face masks. The face mask shortage could be solved by a process Kevin recalled from his work and he told her of a Vaporized Hydrogen Peroxide (VHP) process that could clean the masks 20 times or more for reuse. It was studied by Battelle Memorial Institute. After Dr. Hommema and Kevin brought the VHP process application to their respective employer's attention they were able to have the process validated by the FDA in a very short time of two weeks from their dinner conversation. Boston Hospital was one of the first hospitals to purchase the process in early April to clean and reuse 80,000 N95 face masks per day thereby eliminating the face mask shortage in the short term. Hope this helps add to your list of contributions. Take care and be safe, Joe Yurko
Hi Joe, I'm John Vasko, AIChE's director of communications. I'll be sure to pass along your excellent comment to June. It's an excellent story of how a simple dinner conversation and chemical engineering innovation led to an improvement for many healthcare workers. I will also link to your comment from the our Engage discussion on this. Thanks again.
Thank you June for sharing the excellent contribution of Chemical Engineers. It made me proud of being a future chemical engineer. I still have a lot to learn and create Stay safe!
Thank you June for sharing the excellent contribution of Chemical Engineers. It made me proud of being a future chemical engineer. I still have a lot to learn and create Stay safe!
Iam Rama, worked as Head of plant operations at IG Petrochemicals Limited. Due to Corona virus, everywhere people are restricted to houses or respected living places, which might be leading to loneliness and boredom. In order to keep morale high and maintain health – Yoga and pranayama is the best idea. It will avoid boredom or loneliness which will help in times like this. Also, it is known to control Blood pressure and sugar levels. I have 28 years experience in fertilizer (Ammonia and Urea) and also 2 years in petrochemicals (Phthalic anhydride) industries. I will try to clear the doubts/queries to the best of my knowledge in the areas of Operation, Production, Technical Services, Incident investigations, MOC modifications etc. Regards,
As a chemical engineer we are trained in kinetics and mass transfer. I have also had training in statistics and modeling which are areas where I believe the epidemiologist have borrowed some of their ideas from in the past. One of the things I started getting intrigued about was why the models they were using was so far off. Yet there also seemed to be considerable debate about how effective the plans were to isolate the majority of the country and to flatten the curve. Yet I seemed to reflect back to my studies of kinetics and realized there seemed to be some similarities between the tactics being employed and the way we view chemical reactions, particularly with respect to mass transfer. Now I am sure there a lot of practicing engineers and professors out there that will correct this emeritus member if I am wrong. But my analogy is: In the case of normal exposure to the virus by a society where no massive effort to quarantine a large part of the population in stay at home orders (like Sweden has done). This would be like a plug flow reactor. Hypothetically the contact is products with reactants (transmitting person to susceptible person) and progresses until there is a smaller and smaller amount of reactants (portion of the population that either has caught the virus and has symptoms or is asymptomatic, or has somehow avoided to catch it. Due to the high rate of reaction (transmission) their is a high rate of contagion.) A secondary reaction can take place where some undesirable side products are made. (Death comes to those unable to fight it off) The final product desirable product is a population that generally starts building up a certain amount of herd immunity. It is viewed that if certain rate of reaction is exceeded, then too much of the undesirable side product is made as the facilities to handle it are exceeded. The limited reaction case is where a certain amount of reactants are withheld for a period of time. This is to allow the facilities needed to handle the secondary reaction to match the output that is generated. (flatten the curve). However, by holding back the amount of reactants the amount of desirable product is too small. SO after the initial reaction is starting to die down, and the secondary reaction is being minimized the additional reactants that have been withheld are now being added to the reactor. The major difference between this sort of process and the plug flow reactor is that now there are a number of contagious persons, some asymptomatic that are well mixed through the reactor (the community).But also there are more immune people mixed throughout which may reduce transmission. This is now what we often refer to as a mixed flow reactor. Now it is well known in the chemical engineering community that at low conversions a mixed flow reactor is superior to a plug flow reactor. But at high enough conversions the plug flow reactor is superior. In this case superior means more efficient needing less volume to complete the reaction. In the case of the viral contagion, more efficient is bad. The conversion rate (transmissibility) seems to be rather high. It would be good if it results in more people being exposed and more getting healed and obtaining immunity. But generally this will mean too many to be treated and more undesirable side reactions (too many deaths). So what seems to be the desirable path would be the less efficient mixed flow reactor. This seems to be the path that is being followed by the epidemiologists today. Maybe they are right and although it will result in a second or third wave, the total number of deaths may not be as high as just the single plug flow model. Any discussion?