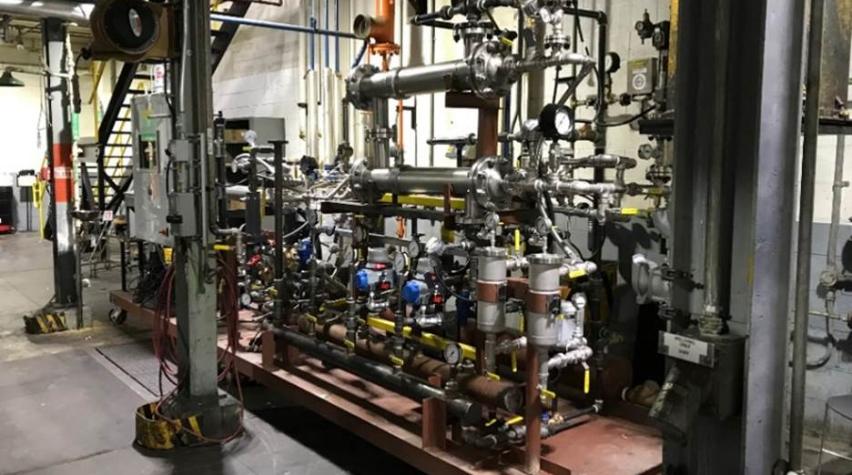
Photo copyrighted by Lubrizol Corporation.
The Lubrizol Corporation and the University of Pittsburgh, both RAPID Manufacturing Institute® members, worked together on a RAPID project to convert one of Lubrizol’s key legacy processes for chemical dispersants from batch to continuous while incorporating the principles of modular process intensification. The project team succeeded in building a continuous process production module about the size of a shipping container.
We discussed the project with Glenn Cormack and Nico Proust of the Lubrizol Corporation to learn more about its accomplishments and their experience working on this project with the University of Pittsburgh.
What are some of the challenges associated with implementing continuous processing?
The first challenge is to assess chemical feasibility, including a study of reaction kinetics, evaluation of reaction safety, and understanding of product quality requirements.
Then, engineering hurdles are studied, including heat transfer efficiency (heating or cooling), diffusion limitations (static/dynamic mixing, emulsion stability, viscous laminar flows), residence time requirements, stripping requirements, electrical/controls standardization for the unit to operate in any plant/country of destination.
Financial viability of the project/unit is another challenge - cost analysis, revenue analysis (with sensitivity analysis), Net Present Value and Return On Investment calculations must be conducted. Financial viability needs to be revalidated frequently during the entire project!
What were some of the key accomplishments of this partnership?
The University of Pittsburgh established the detailed reaction kinetics for the dispersant reaction and completed the lab-scale batch-to-continuous process transition.
Lubrizol completed the advanced engineering design of a modular manufacturing unit the size of shipping container. We built, commissioned, and deployed the modular manufacturing unit to one of our plants.
The modular unit was compared to a standard 30,000-gallon batch reactor system akin to the ones currently operated by Lubrizol around the world. The modular unit led to an overall capital efficiency gain of 66%. These gains were made possible mainly by reducing the overall utility requirements such as hot oil heating systems, cooling systems and batch filtration capabilities.
Furthermore, the intensified design of the modular unit allowed for efficient heat recovery and process condition optimization which led to a 24% reduction in energy intensity. The modular unit is fully operational and is producing commercial material for Lubrizol.
What are some other benefits of modular design in manufacturing?
There are many advantages, ranging from safety and supply chain, to capital risk and energy consumption.
For example, modular designs are inherently safer because they minimize both the unit size and quantities of chemical under reactive conditions. In addition, they help moderate operating risks because they combine unit operations and automating controls.
In terms of financial gains, modular designs often help reduce capital requirements and operating expenses, compared to full-size units. Further gains can also be made in energy consumption (heat recovery, improved heat transfer), emissions (no nitrogen purging necessary in liquid-full pipes), and waste generation (optimized process).
As for supply chain advantages and improved manufacturing logistics, modular designs allow for portable manufacturing units to be deployed and operated regionally, and units can also be repackaged and redeployed to other locations as needed.
There are also rewards to be had in corporate finance because modular designs can be used to de-risk corporate investments through incremental capital expenditure commitments to better time market growth and regionalization.
How will/has this project contributed to Lubrizol’s process development? Can these findings be translated to other organizations?
This project has established a successful precedent for the application of Process Intensification and MCPI principles at Lubrizol. It led to the creation of a new team at Lubrizol, the Process Innovation team. One of the main missions of the team is to identify opportunities within Lubrizol where Process Intensification could be leveraged to deploy new CAPEX-efficient capacity for rapidly-growing product lines, or deliver significant efficiency improvements to large scale processes; all this to support Lubrizol on its ongoing journey towards sustainable manufacturing. Furthermore, we believe this mission is clearly transferrable across the specialty chemicals industry as we are already experiencing interest from suppliers, customers, and even competitors to team up with Pitt and Lubrizol and help them translate these advances to some of their product and technology lines.
How did RAPID facilitate the collaboration between the University of Pittsburgh and Lubrizol?
The relationship between Lubrizol and University of Pittsburgh started in 2014 and was an attempt to create a paradigm shift in the way Lubrizol engaged with our university partners. Lubrizol and Pitt Engineering faculty set up many opportunities to engage across all of Lubrizol's business units and disciplines of the Swanson School of Engineering.
In 2017, when RAPID was founded (with Pitt being a founding member), Lubrizol and Pitt engaged with the RAPID team to execute a first-of-its-kind project to look at process intensification in the specialty chemicals industry. The joint relationship between Pitt and Lubrizol really flourished with RAPID's support. The project set a precedent for how Lubrizol and Pitt engage on pre-competitive research not just between the two organizations but with the larger RAPID technical community and beyond.
Prior to the RAPID project, Lubrizol did not meaningfully participate in governmental research solicitations, but through RAPID's guidance our knowledge and comfort with this type of research has dramatically improved. In late 2021, Lubrizol and Pitt renewed their original research alliance for a second time, adding an additional $1M in collaborative research funding.
Learn more RAPID projects and join the process intensification community today.