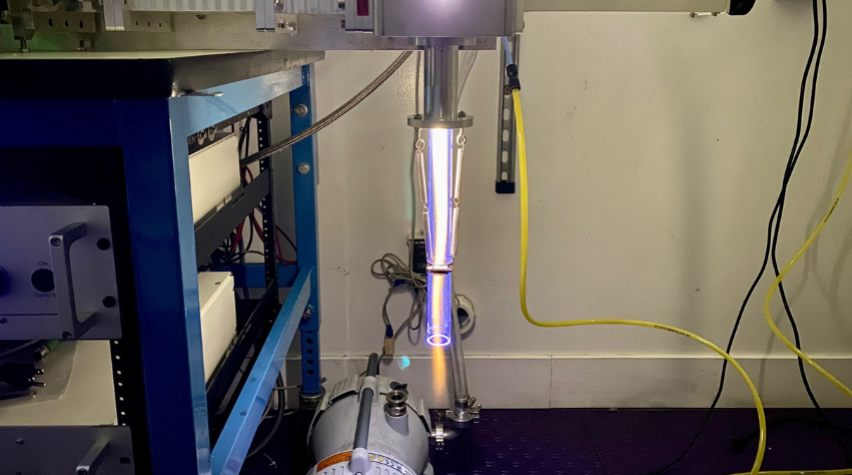
As reports of intense extreme weather events continue to dominate headlines, the need for concerted efforts to decrease greenhouse gas (GHG) emissions is clear. The recent decarbonization roadmap released by the DOE has underlined the need to prioritize decarbonization efforts within the petroleum refining and chemical manufacturing industries, since together they represent 37% of the energy-related CO2 emissions in the U.S. industrial sector.
Process electrification, particularly when combined with the use of renewable power, can be a valuable tool for decarbonizing the chemical process industry. As engineers look for ways to incorporate process electrification with renewable power, there’s been a renewed interest in reactors using advanced energetics such as microwaves (MW). Commercially, microwaves are currently used for separations such as drying in the food industry. Several recent RAPID projects have extended the use of microwaves to reactor heating, helping to pave the way towards commercialization.
MW reactors and decarbonization
Using MW heating instead of conventional heating gives improved energy efficiency. Energy requirements can be reduced by using MW’s capability for targeted heating – heating a catalyst surface rather than the entire reactor and its contents. MW heating can also improve reaction selectivity which minimizes energy-intensive downstream separations.
The rapid heating produced by microwaves reduces processing time and energy required. This rapid heating also enables the use of intermittent renewable power sources like wind and solar, further contributing to decarbonization efforts.
MW reactors in modular process intensification
Process intensification can be used as a tool to help with decarbonization. MW heating has several characteristics that can help with process intensification and enable smaller modular systems, allowing deployment for distributed feedstocks such as stranded natural gas or biomass. The improved reaction selectivity afforded by MW heating enables similar yield from lower throughput rates, giving the same production rate from a smaller system. MW heating also provides higher turndown ratios and a smaller footprint than traditional conventional heating approaches, facilitating smaller more intensified systems.
How MW reactors are different
MW heating depends on the dielectric properties of the materials and hence offers the possibility of selective heating, allowing energy to be directly delivered to the reacting species and/or susceptor. For catalytic systems, this selective heating can create a temperature differential between the gas and solid phase, changing reactor performance by localizing reactions in one phase and minimizing side reactions in the other phase. This can also reduce catalyst fouling and degradation.
Unlike conventional heating, which relies on conduction and convection from hot surfaces to heat a reactor’s contents, MW heating can be used to provide volumetric heating, evenly heating the entire volume of a flowing liquid or suspension. This minimizes thermal decomposition and allows viscous products to be heated without fouling.
RAPID’s work advancing microwave reactors
Although MW technology can clearly support decarbonization goals, more research is needed to better understand how to best design MW reactors. In-situ temperature measurement challenges in a MW environment limit current understanding. Currently catalysts and reactors need to be designed together for each application – a more generalized approach still needs to be developed. Using funding from the DOE, RAPID supported two research projects to improve understanding of MW reactors as well as demonstrate improved energy efficiencies for the studied reactions.
Researchers at West Virginia University, in partnership with the University of Pittsburgh, Shell, and National Energy Technology Laboratory have demonstrated the continuous lab-scale upgrading of natural gas to olefins and aromatics. Compared to conventional thermal reactor systems, the energy efficiency improvements shown with their MW reactor enable economically feasible smaller modular systems. This would allow implementation at both stranded gas sites with a smaller modular system as well as at large scale natural gas conversion plants by using a larger number of modular systems.
Another project was carried out by researchers at the University of Delaware. The first part focused on producing bio-products from biomass using a continuous MW reactor. The lab-scale conversion of glucose to para-xylene was studied. Computational fluid dynamics (CFD) modeling and Technoeconomic analysis (TEA) work were used to optimize the reactor size and energy operating costs. The study demonstrated that modular manufacturing of biomass was both technologically and economically feasible at a crude-oil price of $90/barrel. A second part of this project, done by the University of Delaware in partnership with Rutgers University and Raytheon Technologies, also combined experimental work with modeling. This project focused on using MW technology for several multi-phase systems (gas/solid and liquid/solid). The efficient separation of 5-hydroxymethylfurfural (HMF) from an aqueous mixture of biomass sugars using a periodic temperature swing process with MW heating was shown. Using a MW-absorbing monolith whose channels were filled with catalyst pellets, dry reforming of methane was demonstrated with good conversion (86%) and lower temperatures than conventional systems. Additionally, propane dehydrogenation was shown with this technology, resulting in improved selectivity (98%) and reduced catalyst coking.
The use of MW energy instead of conventional fossil-fueled heat for chemical reactors shows great promise in helping to meet current decarbonization goals. Although more research is needed, RAPID-supported research projects have helped to fill in the gaps to better understand how to exploit this new form of heating.
Learn more RAPID projects and join the process intensification community today.