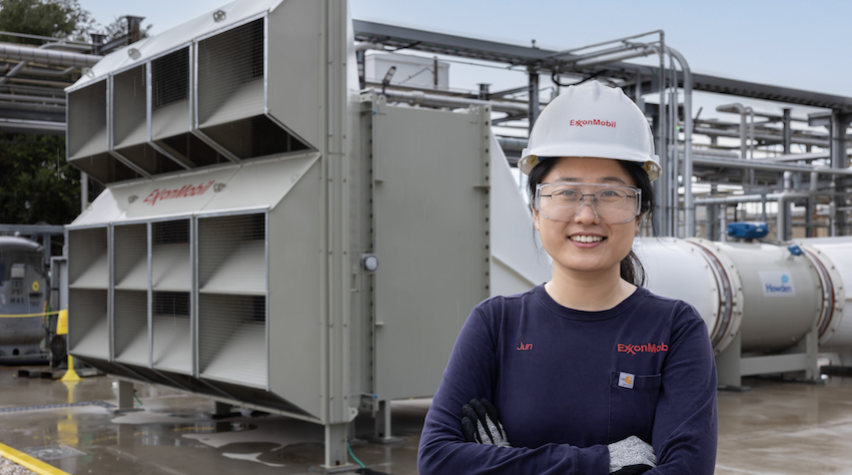
The theme of this year’s ChemE Cube Competition™, powered by RAPID Manufacturing Institute® and ExxonMobil, is once again direct air capture. The 4th Annual ChemE Cube Competition will take place October 27 and 28 in San Diego, CA, during the 2024 Annual Student Conference (ASC) where 18 teams will compete.
ExxonMobil has invested in a direct air capture pilot project at their facility in Baytown, Texas, to create a scalable and economically viable solution. Jun Shi, lead process researcher at ExxonMobil’s direct air capture pilot, shares the lessons learned (so far).
Disclosure: This post is sponsored by ExxonMobil and reflects their views, opinions, and insights.
I’ll never forget where I was on Valentine’s Day this year. That’s the day we started up the direct air capture (DAC) pilot at our manufacturing site in Baytown, Texas.
I’m the lead process researcher for this project, which is directly supported by about a dozen ExxonMobil scientists, engineers, researchers, and operators.
We were eager with anticipation that February morning as we finalized our checklist and initiated start-up. Moments later, when control room monitors showed the unit was working as planned – removing carbon dioxide (CO2) molecules directly from the air – we all burst into cheers.
We were excited because negative-emission solutions like DAC could play a big role in meeting the world’s net-zero goals. Now, with our pilot up and running, the team could embark on its bigger mission: to improve DAC technology and – most importantly – bring down its cost.
For a chemical engineer like me, it’s thrilling to tackle a real-life challenge with potentially huge benefits for society. I’m excited to share some of what we’ve done and learned so far.
What we’ve done
For those unfamiliar with DAC, here’s how it works: powerful fans suck in ambient air, which is passed through a “filter” that captures CO2 molecules. The processed air is then sent back into the atmosphere. And the filter is later regenerated – meaning the captured CO2 is extracted, and it’s ready to go to work again.
So while the world advances emissions solutions like low-carbon hydrogen, carbon capture and storage, and low-emission transportation fuels (all of which ExxonMobil is working on), DAC holds the promise of removing the CO2 those solutions may not be able to reach. One of my colleagues likens it to the “clean-up hitter” in baseball.
What we’ve learned
Since February, our DAC pilot team has been hard at work performing process studies that have produced useful data and insights about what we believe is our unique approach to DAC. While it’s still early days, these findings are an important first step – because success here could be a springboard to direct air capture at a much larger scale.
Here are four things I can share:
- Working as expected. So far, the unit’s CO2 capture performance has aligned with our expectations. That’s good, because it gives us more confidence in our process and our fundamental understanding of the active material we’re using to capture the CO2. Our pilot has run successfully through all kinds of conditions, including near-freezing temperatures, heavy storms and hot Texas summer days.
- Ambient conditions matter. With the pilot running continuously, we’ve learned how much things like temperature, humidity – even pollen count – impact performance. That’s why we do a pilot: while ExxonMobil’s been researching DAC for years, some things can only be learned by getting out of the lab and into the real world.
- Opportunities ahead. We’re testing all the novel components of our DAC platform, from the active material (the key component in the “filter” capturing CO2), to mechanical and engineering design, to process operating procedures and strategies. We’re already seeing opportunities for optimization.
- We’re moving fast. Our pilot was built quickly – less than a year from concept selection to completion. And we’re accelerating our learning cycles by addressing DAC’s two main challenges (active material improvement and process development) in parallel. This should result in faster progress.
What’s ahead
It’s good we’re moving fast on DAC.
As our CEO Darren Woods has said, DAC is the “holy grail” of emissions technologies, but to be commercially viable its cost needs to come down – by at least 50 percent from today’s range of $600-$1,000 a ton. The key challenge is that atmospheric CO2 is very dilute: you need to process about 2,000 metric tons of air to capture just 1 metric ton of CO2.
But what if we could find a way to do it more efficiently?
That’s why at its heart, DAC’s an engineering challenge. And it’s one reason why I think this is an amazing time to pursue an engineering career.
Solving the world’s energy and climate challenges will require minds skilled in chemistry, material science, engineering, and process development.
The challenges that today’s generation of young engineers tackle in their careers might differ from traditional chemical engineering problems, but the fundamentals are the same – and the opportunities to make a difference are huge.
Learn more about how ExxonMobil is accelerating society’s path to net zero by scaling up emissions solutions for key industries.
Learn more about Direct Air Capture.
Learn more and follow ExxonMobil’s Low Carbon Solutions on LinkedIn.
While you’re at the Annual Meeting or Annual Student Conference (ASC), don’t forget to join us live in San Diego, CA, to watch the teams compete.
Disclosure: This post is sponsored by ExxonMobil and reflects their views, opinions, and insights.