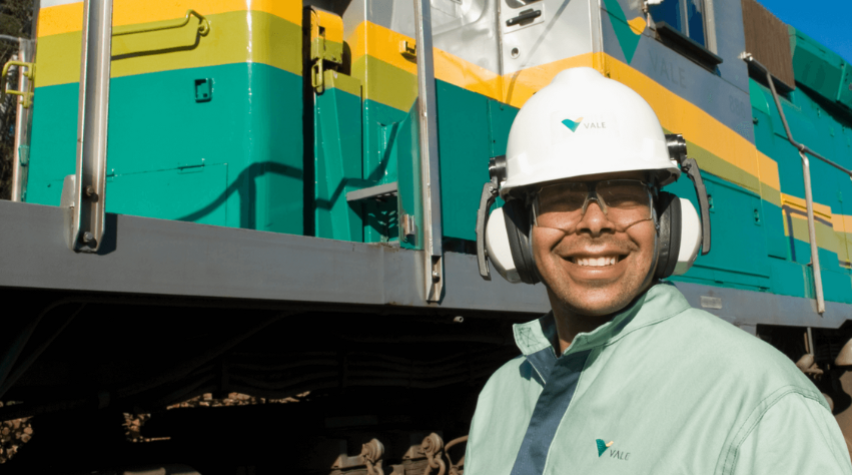
Disclosure: This post is sponsored by Vale.
Vale S.A. is a multinational corporation headquartered in Brazil, and it is one of the largest mining companies in the world. Established in 1942 as Companhia Vale do Rio Doce, Vale has grown into a global leader in the production of iron ore, nickel, and other minerals, playing a crucial role in the global mining industry. The company operates in over 30 countries and is recognized for its significant contributions to the steel industry through its vast iron ore reserves. Additionally, Vale is involved in logistics, energy, and steelmaking activities, positioning itself as a diversified player in the global market.
Eduardo M. Francisco is the Chair of AIChE/CCPS’s Committee on Mining, Metals and Metallurgy and a global leader in process safety, a keynote speaker, and a conference chair member for the 10th CCPS Latin American Conference on Process Safety, taking place from September 18–20, 2024 in Barranquilla, Colombia. Topics covered include leadership and culture in process safety, emerging topics, cyber risks, and process safety technologies, among others. You can learn more about LACPS programming on the conference website.
Below, hear from Eduardo about the important role of process safety management in the mining industry.
What are some key elements of process safety management (PSM) in the mining industry?
Key elements of PSM in the mining industry include the following:
- Process hazard analysis (PHA): Systematically identifying and evaluating hazards. For example, assessing the risks of chemical leaks during ore processing.
- Operating procedures: Developing detailed procedures for safe operations. For instance, specific guidelines for handling explosives in underground mining.
- Mechanical integrity: Ensuring the proper maintenance of equipment. An example is routine inspections of conveyor belts to prevent mechanical failures.
- Emergency response planning: Preparing for potential incidents. For example, creating evacuation plans for workers in case of a mine fire.
- Management of change (MOC): Reviewing and managing safety implications of any changes. For instance, assessing the safety impact when introducing new mining machinery.
These elements work together to prevent accidents and ensure a safe working environment.
Can you provide an example of how process hazard analysis (PHA) is applied in the mining industry?
An example of PHA in the mining industry can be seen when assessing the risks associated with using cyanide in gold extraction. During the PHA process, the company would identify potential hazards such as cyanide leaks or accidental spills. The analysis might reveal that a spill could occur if the storage tank is overfilled or if the transfer hose fails. To mitigate these risks, the company might implement controls such as level sensors to prevent overfilling, regular inspections of hoses, and secondary containment measures. By conducting a PHA, the company can proactively address potential hazards and prevent incidents.
How does the management of change (MOC) process apply to introducing new technology in a mining operation?
When introducing new technology, such as automated drilling systems, the MOC process ensures that all potential safety impacts are evaluated before implementation. The process includes:
- Risk assessment: Identifying hazards new technology might introduce, such as increased risk of equipment malfunctions or worker exposure to moving machinery.
- Updating procedures: Revising operating and maintenance procedures to incorporate new technology, ensuring safe operation.
- Training: Providing training to operators and maintenance staff on the new system, focusing on safe operation and emergency response.
- Communication: Ensuring that all stakeholders, including workers and management, are aware of the changes and understand their roles in maintaining safety.
If a mining company decides to use autonomous vehicles for ore transportation, the MOC process would assess the impact on worker safety, update traffic management plans, and ensure all personnel are trained in how to interact safely with the new vehicles.
How does proper mechanical integrity management in PSM prevent accidents in the mining industry?
Proper mechanical integrity management ensures that all equipment used in mining operations is maintained in good working condition, reducing the likelihood of mechanical failures that could lead to accidents. For example, consider the case of a high-pressure steam boiler used in a mineral processing plant. Regular inspections and maintenance of the boiler’s pressure relief valves, piping, and structural components are essential to prevent catastrophic failures like explosions. By following a strict mechanical integrity program, the mining operation can identify and repair potential issues before they result in an accident, ensuring the safety of workers and the surrounding environment.
What role does employee training play in emergency response under PSM, and can you provide an example from the mining industry?
Employee training is critical for effective emergency response under PSM, as it ensures that workers know how to react promptly and correctly in the case of an incident. For example, in an underground mining operation, a fire outbreak is a severe risk. Employees must be trained on how to use fire suppression equipment, evacuate safely, and assist in the rescue of coworkers if necessary. A well-trained team can quickly implement the emergency response plan, reducing the impact of the incident, protecting lives, and minimizing damage to equipment and the environment. A mining company might conduct regular fire drills, teaching workers how to reach safe zones and use a breathing apparatus in the event of smoke or gas release.
Learn more about the 10th CCPS Latin American Conference on Process Safety.
Eduardo M. Francisco
Eduardo M. Francisco is a global leader in process safety, with more than 37 years of expertise in process engineering and process safety management in different industrial segments like chemical, mining, metals and metallurgy.
Disclosure: This post is sponsored by Vale.