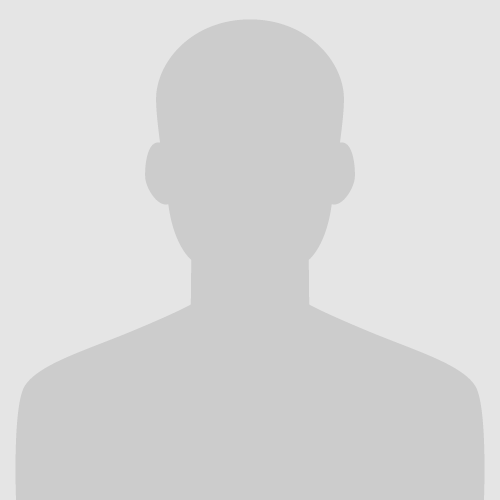
Session Chairs
- Bill Hollar, SABIC
- Deboleena Chakraborty, The Dow Chemical Company
Session Description
Incorporation of new process technology into existing and new chemical plants often requires substantial development efforts to insure success. At the same time, the new process technology can be the key enabler for the global chemical industry to continue to optimize costs, improve flexibility and achieve desired environmental performance and sustainability targets. This session will focus on the challenges and opportunities associated with process development. Approaches to improve the speed and robustness of new technology implementation will be discussed.
*All session and speaker information is subject to change pending finalization
Schedule:
TIME | PRESENTATION | SPEAKER |
3:00pm | Quick-fire Process Development Case Studies – Five Lessons Learned | Stacie Santhany, The Dow Chemical Company |
3:30pm | Development of Separation Processes and Applications using Hollow Fiber Membranes: Challenges and Opportunities | Robert Crowder, Pentair |
4:00pm | Contextual Approaches to Process Development for Products Development, Process Improvements, and New Process Development | Ramesh Rameswaran, SABIC |
Abstracts:
Quick-fire Process Development Case Studies – Five Lessons Learned
Stacie Santhany, The Dow Chemical Company
As a process research engineer, all chemical engineering disciplines merge upon us to make us most effective in our roles. This gives us opportunities to become deep technical experts narrow in certain fields of chemical engineering or to become ‘expert generalists’ that work across disciplines to bring it all together. In this talk, five lessons learned will be discussed in a quick fire manner that spans across Reaction Engineering, Solids Processing, Process Modeling, Economics, and Technology Transfer. With appropriate time, cost, and expertise everything can be done with a high level of success. Those three constraints are not always available to us in this fast pace world, which can lead to some lessons learned.
Development of Separation Processes and Applications using Hollow Fiber Membranes: Challenges and Opportunities
Robert Crowder, Pentair
Membrane systems can offer an effective alternative to more conventional unit operations. The fact that membranes work differently than older technologies can give them advantages in certain applications. Understanding how and when to use membranes will lead to more productivity, and fewer failures. To that end we will briefly look at three diverse membrane applications and understand the challenges and opportunities of each.
The first application is that of waste water treatment with an anaerobic membrane bioreactor (AnMBR). Membrane systems can handle higher strength waste water with a smaller footprint and a higher purity filtrate than conventional settling ponds. In addition, anaerobic MBRs produce a useful byproduct. The challenge is that sizing and pretreatment of the system must be done carefully to ensure a good outcome. In addition, some waste streams are more suited for an AnMBR than others.
The second application is that of beer filtration. Membranes provide benefits vs diatomaceous earth filtration in terms of cutoff, contamination, and scalability. Here the challenge is to understand the cleaning cycle and the transmembrane pressure during that cycle and operate these systems in a way to ensure longer periods of time between cleanings, leading to longer membrane life and higher productivity.
The third application is quite different from the first two. This involves a gas separation membrane used for drying compressed air or other gases. In this case the opportunity presented by membranes over pressure swing adsorption or refrigerated dryers is that of smaller footprint, simpler operation, and scalability for point of use. Membranes are not invulnerable, however, so care must be taken to avoid fouling or rupture. In this use, differences in operation and pretreatment can mean the difference between years of productive output and a short, marginally productive life.
Contextual Approaches to Process Development for Products Development, Process Improvements, and New Process Development
Ramesh Rameswaran, SABIC
Approaches to process development vary with the specific need. For example, when developing a new performance product for market introduction the focus is on getting the correct formulation and efficacy of the product for the intended application. In general, these products are low volume, high margin materials. Therefore, process development activities for such products primarily focuses on maintaining product performance. Cost of producing the material is a secondary concern. For initial market introduction, process development work will focus on utilizing existing in-house or external equipment (toll manufacturing).
On the other hand, a new process development for a commodity material will center mostly on process economics. In general, the market dictates the product value (price of the material, raw material price, and utility costs. Process efficiency becomes the key focus of such process development programs.
Process improvement activates lies between the two. Typically, for a commodity material, the priority will be identifying value killers. Again, the majority of activities will be about reducing raw material cost and /or reducing energy cost and reliability improvements with minimal capital investment as improvements to the process. Whereas, for performance products, as long as, the performance of the product can be maintained, raw material efficiency, processing efficiency etc. can become the focus.