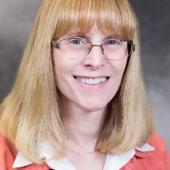
This session will focus on recent trends in Process Safety including the use of technological advances to increase workplace safety, developing/modifying standards for scale-up of new one-of-a-kind processes, and identifying potential scale-up risks at the bench scale to enable better route selection and safer commercialization.
Session Chairs:
- Pranav Karanjkar, Dow
- Liz Moore, RAPID
Tentative Schedule:
tIME (edt) | PRESENTATION | SPEAKER |
---|---|---|
3:00 PM | Mechanistic Understanding Guides Impurity Control Strategy for CELMoD API Reaction | Geoffrey Purdum, BMS |
3:30 PM | Technology Advances to Drive Workplace Safety | Kathy Kas, Dow |
4:00 PM | Achieving Large-Scale Success from Small-Scale Lessons | Esther Wilcox, NREL |
Abstracts:
Mechanistic Understanding Guides Impurity Control Strategy for CELMoD API Reaction
Geoffrey Purdum, Bristol Myers Squibb
Cereblon modulators are prevalent throughout BMS’s portfolio, including IMiDs® and CELMoDs®. These molecules bind to cereblon through a glutarimide ring, which is responsible for the highly-potent nature of these compounds. To minimize the number of high-potent steps, the synthetic sequence of these compounds has been designed to install the glutarimide ring in the final chemical transformation via an acid-catalyzed deprotection and cyclization. In this presentation we will highlight reaction studies on model systems utilizing in-situ process analytical technologies (PAT) coupled with kinetic analysis and design of experiments (DoEs) to gain a mechanistic understanding of the desired and undesired reactions. Key findings from these studies indicate that the deprotection has a second-order dependence on catalyst concentration and that the undesired reactions largely stem from accumulation of isobutylene. Controlling the fate of isobutylene is critical for the development of a robust impurity control strategy. We utilized these findings to build predictive models based on mechanistically-derived equations for various portfolio assets, enabling a robust strategy to control isobutylene-related impurity formation to ensure API meets quality standards.
Technology Advances to Drive Workplace Safety
Kathy Kas, The Dow Chemical Company
Confined space entries and elevated work are two of the most hazardous practices in the chemical industry. According to data collected by the U.S. Department of Labor, 148 fatalities occurred during confined space entries in 2018; in 2020, 805 fatalities were attributed to falls to a lower level. As part of its breakthrough Manufacturing 4.0 initiative, The Dow Chemical Company has been employing devices such as Unmanned Aerial Systems (UAS or “drones”) and robotics to eliminate the need for employees to enter confined spaces or conduct elevated work. Since piloting these robotic tools in 2016, the need for over 6,000 confined space entries have been eliminated at Dow. In addition to internal equipment inspections, UAS are also being used to inspect towers and pipelines – eliminating the need for elevated work - and miniature submarines are used to conduct underwater inspections. The role of robotics in safety is continuing to expand beyond gathering visual data; robots are now equipped with sophisticated tools for gathering samples and non-destructive data, enhancing the ability to monitor environmental performance and ensure mechanical integrity.
The benefits of UAS and robotics in reducing human risk, enhanced data collection, and improving productivity are quite clear; however, the hazards of these technologies need to be carefully evaluated to ensure that the devices can be used safely in specific applications. This paper discusses potential risks that should be considered when evaluating the suitability of a UAS or robot for a particular application and provides guidance on leveraging hazard recognition tools and training to the site and corporate levels.
Achieving Large-Scale Success from Small-Scale Lessons
Esther Wilcox, National Renewable Energy Laboratory
Application of codes, standards, and best practices are necessary, yet not always sufficient mitigate safety risks associated with new technologies. When selecting technologies for scale-up and commercialization, focus is often placed on the positive results and successes of bench-scale research. In order to identify and mitigate safety hazards during scale-up, it is essential to fully understand the efforts that went into achieving the bench-scale success, as well as near misses and lessons learned associated with the research.
This presentation will provide specific examples of near misses and lessons learned from bench-scale experiments and how those can be applied to improve safety, operability, and data quality at pilot scale and beyond. It will also offer guidance for how to obtain that vital information regardless of technology and how to identify opportunities for improvement during the scale-up process.