
The U.S. Space Shuttle Challenger exploded 73 seconds after launch from Cape Canaveral, FL, on Jan. 28, 1986 (Images 1 and 2). The Challenger was destroyed and all seven crew members perished. The immediate cause was a leak of hot gas from a joint in the solid fuel rocket boosters. The hot gas impinged on the hydrogen fuel tank, causing it to rupture and explode. The primary and secondary O-rings that sealed adjoining segments of the boosters both failed due to low temperatures on the launch day. The primary seal had failed on several previous launches, but in each prior instance, the secondary seal successfully preserved the solid fuel rocket integrity. These primary-seal failures were near misses, but were not deemed serious enough for investigation.
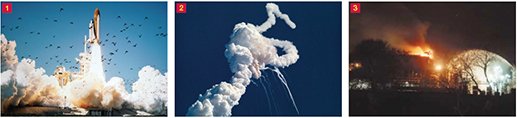
Failure to report and investigate near misses has been a factor in process industry incidents as well. On Apr. 8, 1998, a runaway reaction overpressurized a 2,000-gal batch reactor at a plant in Patterson, NJ. The explosion and fire (Image 3) injured nine workers — two seriously. Operators were unable to control the batch temperature using existing procedures and available cooling methods. Operators had been unable to control the temperature below the specified maximum during six previous batches, but the temperature did not rise high enough to trigger a runaway reaction. These near misses were not investigated.
Did you know?
- Investigators of major process safety incidents often find that there were previous warnings and near misses. If these had been reported and investigated, and the findings implemented, the major incident may have been prevented.
- Incidents highlight problems to be fixed, but it is certainly preferable to learn from near misses, where no injuries occur and damage is not significant.
- Near misses cannot be investigated if they are not reported. Near misses cannot be reported if they are not recognized as near misses or if their significance is not understood.
- Operating a process safely requires process control. If you are unable to control the process within specified safe operating limits for any critical process safety parameter, recognize and report this as a near miss.
- Successful activation of any safety device or backup device should be considered a near miss. What if the safety or backup device had failed?
What can you do?
- Understand your plant’s incident and near miss reporting and investigation process. If your plant doesn’t have such a system, advocate for its implementation.
- Report all near misses, including failure to control your process within safe operating limits and operation of safety or backup systems.
- Don’t assume shift logs, instrument records, or other process data are sufficient for communicating near misses. Plants generate a lot of data, and these events might be overlooked. If you recognize a near miss, it is your responsibility to make sure management is aware of it.
- If you are not sure if something is a near miss, report it anyway. Always think of the worst-case scenario to help identify a near miss.
- Volunteer to participate in investigations of near misses and incidents at your plant.
Your plant is talking to you through near misses — are you listening?
©AIChE 2018. All rights reserved. Reproduction for non-commercial, educational purposes is encouraged. However, reproduction for any commercial purpose without express written consent of AIChE is strictly prohibited. Contact us at ccps_beacon@aiche.org or 646-495-1371.
Copyright Permissions
Would you like to reuse content from CEP Magazine? It’s easy to request permission to reuse content. Simply click here to connect instantly to licensing services, where you can choose from a list of options regarding how you would like to reuse the desired content and complete the transaction.