This article outlines the steps used in a case study to troubleshoot a caustic scrubber that could not consistently meet design specifications.
Wet and dry scrubbers are used extensively in the chemical process industries (CPI) for separation and purification of gas streams, product recovery, and pollution control. The most common type of wet scrubber is a packed-bed counterflow scrubber (Figure 1). In this system, the contaminated gas stream is fed to the bottom of the tower and the solvent is fed to a liquid distributor at the top of the tower. The liquid flows down the column over the packing and the gas moves counter-currently up the column. The gas-liquid contact in a packed column is continuous, and column performance relies heavily on maintaining good liquid and gas distribution throughout the packed bed. Therefore, liquid distribution is an important consideration in packed column design. At the top of the packing, mist eliminators or demisters are used to capture liquid droplets.
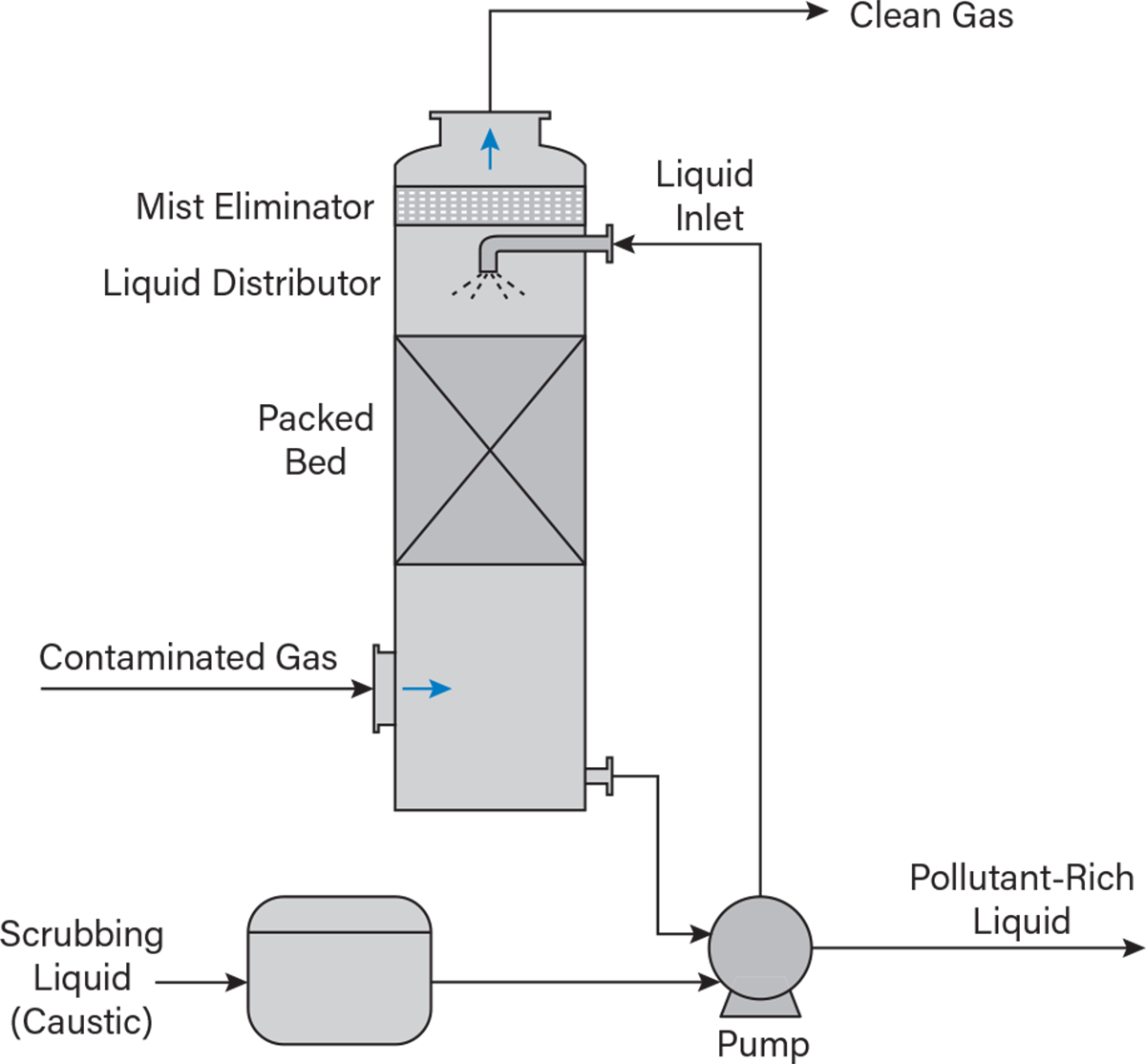
▲Figure 1. In a packed-bed caustic scrubber, the liquid flows down the column over a packed bed and the contaminated gas stream moves counter-currently up the column.
Wet scrubbers use a liquid solvent to remove unwanted chemicals from a gas stream via chemical or physical absorption. Physical absorption occurs when the absorbed compound dissolves in the solvent and chemical absorption occurs when there is a chemical reaction between the absorbed compound and the solvent. Liquids commonly used as solvents include water and sodium hydroxide (NaOH). When caustic is used as a solvent in a scrubber, it is called a caustic scrubber. As a strong base, caustic is an excellent scrubbing agent to remove acid gases like hydrogen chloride (HCl). In the case of HCl absorption, caustic reacts with HCl in the tower to form sodium chloride (NaCl) and water, which is removed at the bottom of the tower.
Removal efficiencies for gas absorption vary for each pollutant-solvent system based on the particle size distribution of the waste gas stream and the type of scrubber. Most scrubbers have removal efficiencies greater than 90%, and packed tower scrubbers may achieve efficiencies as high as 99.9% for some pollutant-solvent systems.
This article describes the troubleshooting steps and approach taken to understand why a caustic scrubber could not meet its design specifications. This article also provides suggestions to address common challenges associated with caustic scrubbers, including thermodynamic and hydraulic limitations, liquid distributor maldistribution, and aerosol formation.
Would you like to access the complete CEP Article?
No problem. You just have to complete the following steps.
You have completed 0 of 2 steps.
-
Log in
You must be logged in to view this content. Log in now.
-
AIChE Membership
You must be an AIChE member to view this article. Join now.
Copyright Permissions
Would you like to reuse content from CEP Magazine? It’s easy to request permission to reuse content. Simply click here to connect instantly to licensing services, where you can choose from a list of options regarding how you would like to reuse the desired content and complete the transaction.