Sections
The worst industrial accident involving ammonia occurred in Dakar, Senegal, in 1992. This article presents an analysis of the incident and its resulting consequences to help prevent future ammonia incidents.
Understanding and managing the hazards of pressurized anhydrous ammonia is extremely important to prevent significant accidents. Many incidents have occurred in the chemical process industries (CPI) while producing, transporting, and using anhydrous ammonia. The Dakar accident in Senegal, West Africa, is the worst industrial accident involving ammonia in terms of fatalities (1). The day after the Dakar incident, “Cloud of Death” was the headline in the local newspaper, and many news reports were published in U.S. newspapers describing the drastic consequences of the accident (2). This article describes the incident and presents an analysis of the consequences. It is important to review the details of the accident to derive lessons that all stakeholders can utilize.
Of course, the worst industrial accident was the Bhopal disaster (3), which involved the release of highly toxic methyl isocyanate gas on Dec. 4, 1984, in India. This industrial disaster caused thousands of deaths and injuries, which resulted in significant changes to industrial process safety and the implementation of stricter safety regulations worldwide (4). Although not as severe, the Dakar accident deserves similar attention as the worst industrial accident involving ammonia.
Understanding the hazards of pressurized gases (e.g., ammonia, chlorine, etc.) and the consequences of hazardous events can lead to good decisions for minimizing process risk. This has been continuously emphasized for numerous industries by the Center for Chemical Process Safety (CCPS) (5, 6), the U.S. Chemical Safety and Hazard Investigation Board (CSB) (7), and other organizations for a variety of different hazardous chemicals.
Ammonia basics
The demand for ammonia production, storage, transport, and use is expected to increase by 10 million m.t. per year. Today, nearly 80% of the roughly 180 million m.t. per year of ammonia produced is for use in the fertilizer industry, with the remaining 20% used in a wide range of other applications. Nearly all of this ammonia is considered gray ammonia because it is produced using energy-intensive processes that emit carbon dioxide (CO2) to the atmosphere. Most countries have established decarbonization goals to minimize or eliminate CO2 emissions in the next few decades.
Although many consider hydrogen to be the fuel of the future, most hydrogen is currently produced via steam-methane reforming, which produces CO2 emissions. The demand for hydrogen is expected to increase over the coming decades, but significant challenges remain in hydrogen production and safe long-distance transport. Ammonia will have a role in the future hydrogen economy because it has a high capacity for hydrogen storage and can be liquefied under mild conditions, allowing for easier storage than hydrogen. Thus, very large quantities of liquified ammonia will be produced, transported, and handled worldwide and later cracked into hydrogen. Ammonia is considered easier to handle than hydrogen and is an ideal hydrogen and energy carrier to meet future global energy needs. In addition to being a hydrogen carrier, ammonia could be used as maritime fuel (for ships and barges) and potentially also used for electric power generation.
The expected global ammonia production rate in 2050 is 500 million m.t., almost three times the current rate. To produce this amount of ammonia while adhering to decarbonization measures, most of the CO2 emitted from the process would need to be captured and sequestered (thus creating blue ammonia). That ammonia could then be cracked into hydrogen at receiving terminals (thus creating blue hydrogen). Producing more sustainable green ammonia would require an ammonia synthesis process based on electrolysis — such technologies are not currently economically viable, but may become more so in the near future.
Hence, the safe production, storage, and handling of liquified ammonia are essential for all stakeholders. Learning from an incident like Dakar can help prevent such incidents from happening again.
The Dakar accident
On Mar. 24, 1992, Senegal in Western Africa experienced its worst industrial accident at a peanut oil processing facility (operated by Sonacos SA) near the Dakar port (Figure 1). Anhydrous ammonia, which was used to detoxify the product made at the facility, was stored in a portable tank commissioned in 1983 and repaired via welding in 1991. The weld repairs were made on cracks detected on the tank’s surface. An overpressure inside the tank led to its catastrophic failure, releasing 22 m.t. of pressurized ammonia (1).

▲Figure 1. The Senegal ammonia incident occurred at a peanut oil mill near the Dakar port (1).
The debris from the tank explosion pierced process equipment (e.g., a hose) containing liquid ammonia under pressure. A two-phase flow of ammonia fluid (vapor plus liquid as a fine aerosol) formed a dense vapor cloud and spread over a significant distance, resulting in injuries and fatalities. The dense plume settled over the oil mill, nearby offices, and adjacent restaurants where people were present at lunchtime. 41 people died immediately, and many others were transported to the nearest trauma center. Ultimately, the incident caused 129 fatalities and 1,150 injuries.
Most of the injuries and fatalities resulted from inhalation of ammonia at concentrations that caused respiratory lesions, edema (fluid buildup) in the lungs, and skin/eye irritation. Near the release location, many fatalities resulted from direct skin exposure, cold burns, and inhalation of high concentrations of ammonia. Fortunately, nearby schools were closed because of the Ramadan holidays, and restaurants were less crowded. Otherwise, the number of fatalities and injuries could have been much higher. Frequent overfilling of the tank, which was authorized to hold 17.7 m.t., was one of the primary causes of the incident noted in the reports.
Process operation and incident details
Peanuts and peanut oil were among the top commodities exported from Senegal in the 1990s. At the peanut oil mill in Dakar, anhydrous ammonia was used to detoxify the peanuts before peanut oil extraction. Anhydrous ammonia was brought daily to the mill by a road truck from a fertilizer company nearby that stored large quantities of cold liquid ammonia in spheres. The tank was then placed at the mill for use as a storage vessel since no other storage tanks were present.
The ammonia tank that exploded had a diameter of 2.2 m, a wall thickness of 11 mm, and a volumetric capacity of 33.5 m3(8). It was constructed of annealed hardened steel. The tank was built by a French company in 1983 and certified as compliant with regulations. From 1983 to 1991, the tank truck was frequently overfilled beyond the authorized filling limit of 17.7 m.t. The overfilling led to overpressure and crack formation that was detected in 1991 during a maintenance inspection. Maintenance workers welded the tank to repair the crack. After the repairs, the truck continued to be overfilled. The day before the incident, the tank was filled with 22,180 kg (22.18 m.t.) of liquid ammonia under pressure and was placed at the mill.
Around 1:30–2:00 PM (during shift change), on Mar. 24, 1992, the tank suddenly burst open along the middle, with the two portions propelled in different directions. The collision from the tank into nearby buildings caused significant damage and debris (Figure 2). The chassis and axle from the truck were found up to 200 m away beyond the facility boundary. Anhydrous ammonia from the tank was released almost instantaneously, and heavy, dense clouds spread well beyond the facility into the industrial and residential neighborhoods. The debris caused the failure of a hose connected to the process vessel, with the discharge continuing for at least 30 min.

▲Figure 2. The exploding tank split into two pieces that were propelled in different directions. These images show the front of the tank from view 1 (left), the front of the tank from view 2 (center), and the rear of the tank (right) (1).
Weather conditions. During the time of the accident, the temperature was 26°C, the wind speed was 4 m/sec, and the wind direction was north (i.e., blowing north to south) (8). These weather conditions were used for the consequence analysis.
Medical treatment. On Apr. 2, 1992, U.S. Ambassador Katherine Shirley declared a disaster and requested emergency respiratory and cardiac monitoring equipment purchase. Pulse oximeters and electrocardiogram (ECG) machines with accessories were procured and immediately dispatched to Senegal. The equipment was donated to the intensive care unit at Dakar’s trauma center, where victims seriously injured by the accident were treated. Nine days after the equipment was received, U.S. Agency for International Development (USAID) and Senegal representatives met with the trauma center staff and were informed that the equipment was the difference between life and death. Of the more than 400 patients admitted to the center, only 31 remained under treatment. In mid-April, the total death count from the accident was 129 people.
The patients treated for minor skin lesions developed pulmonary edema in the trauma center. Most people killed near the tank explosion and release were in semi-confined locations (mills, restaurants, damaged buildings, and the streets nearby). Among the injured were emergency responders that were ill-prepared to deal with an event of this magnitude.
A detailed study (9) revealed that the victims were between three months and 74 years old. The cause of death for many victims was identified as the aftereffects of pneumopathy (pulmonary infection, bronchiectasis, and pulmonary fibrosis). The intensity of lesions and mortality was proportional to the quantity of inhaled ammonia per m3 of air.
Primary cause of incident: Overfilling
A systematic root cause analysis of the Dakar accident shows that multiple causal factors (related to design, operation, hazards management, etc.) were behind the incident. However, one primary cause (overfilling) is apparent and has resulted in and continues to cause numerous incidents worldwide.
Understanding the hazards of overfilling and determining the filling ratio for a variety of containers (cylinders, tanks, etc.) to avoid incidents like the Dakar accident has been widely recognized (10–12). Overfilling of high-pressure compressed (or liquified) gases can result in overpressure and loss of containment.
Filling ratio. The filling ratio is the ratio of the volume of the liquid gas in the receptacle to the total volume of the receptacle (12). For high-pressure liquified gases (like anhydrous ammonia), the filling ratio is determined such that the settled pressure at 65°C does not exceed the test pressure of the pressure receptacle. The minimum test pressure typically required is 1 MPa (10 bar). If relevant data are not available for high-pressure liquified gases, the maximum filling ratio is determined as follows:
where dg is the gas density (at 15°C and 1 bar) in kg/m3 and Ph is the minimum test pressure in bar.
Table 1 shows the published maximum filling ratios for anhydrous ammonia (12). Pressure testing is typically done every five years for ammonia receptacles. For a tank (or any other receptacle) containing anhydrous ammonia under pressure, it is best to ensure that the filling ratio does not exceed 0.53. The tank in the Dakar accident was probably overfilled to a filling ratio of 0.99 before the day of the accident.
Consequence analysis
An analysis of the consequences of the ammonia releases during the incident on Mar. 24, 1992, can be done using the available release and weather data. The Emergency Response Planning Guideline (ERPG) concentrations published by the American Industrial Hygienists Association (AIHA) (13) can be used to determine the acute toxicity effects. The ERPG-2 and ERPG-3 concentrations for ammonia are 150 ppm and 1,500 ppm, respectively. ERPG-2 is a concentration above which irreversible injuries can occur. Severe injuries and potential fatalities can occur based on exposure time at concentrations above ERPG-3.
The probability of fatality can be determined using specified level of toxicity (SLOT), significant likelihood of death (SLOD), and dangerous toxic load (DTL) data published by the U.K. Health and Safety Executive (Table 2) (14).
Around 22 m.t. of ammonia were instantaneously released when the tank exploded. In addition, the loss of containment from a hose connected to the process tank continued for a significant period. The PHAST process hazard analysis software by DNV was used to model the release and dispersion of the heavy gas cloud from the two scenarios: instantaneous release of 22 m.t. and continuous release from hose failure (15).
The maximum footprint generated by the instantaneous release of 22 m.t. is shown in Figure 3. The injury concentrations (ERPG-2) extend to around 4,200 m with a width of about 4,000 m. The distance that the ERPG-3 zone extends is about 1,500 m, the zone within which serious injuries and fatalities might have occurred. The visible portion of the plume would only extend up to 900 m, much less than the zone within which injuries can occur. Figure 4 shows an estimate of distances for the higher probability of fatalities. Up to a distance of almost 200 m, the probability of fatality is 100%. This probability decreases to 0.1% by 500 m, primarily because the exposure time is shorter for an immediate release.
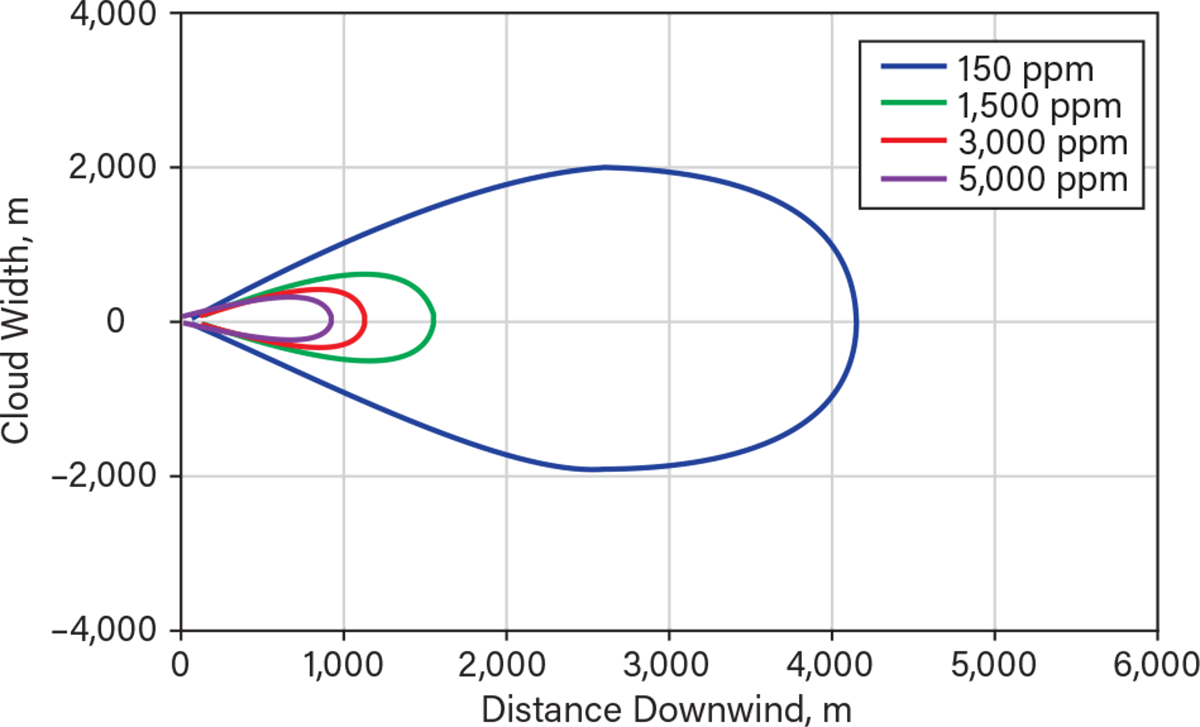
▲Figure 3. This model shows the maximum predicted footprint for various concentrations when 22 m.t. of anhydrous ammonia is instantaneously released. The extent shown is for neutral atmospheric conditions and a windspeed of 4 m/sec that was present on Mar. 24, 1992, when the incident occurred.

▲Figure 4. The predicted probability of fatality eventually decreases with distance for the instantaneous release of 22 m.t. of anhydrous ammonia. The distances shown are for neutral atmospheric conditions and 4 m/sec windspeed.
The maximum footprint generated by the continuous release from a 3-in. hole (e.g., hose failure) is shown in Figure 5. The plume is narrower (less than 1 km), but the injury concentrations (ERPG-2) extend to almost 5 km. The distance to ERPG-3 is less than 1,500 m — i.e., where there might have been serious injuries and fatalities. The visible range would have also been around 900 m. Figure 6 shows a model of the probability of death vs. distance downwind. Up to a distance of almost 400 m, the probability of fatality is 100%.
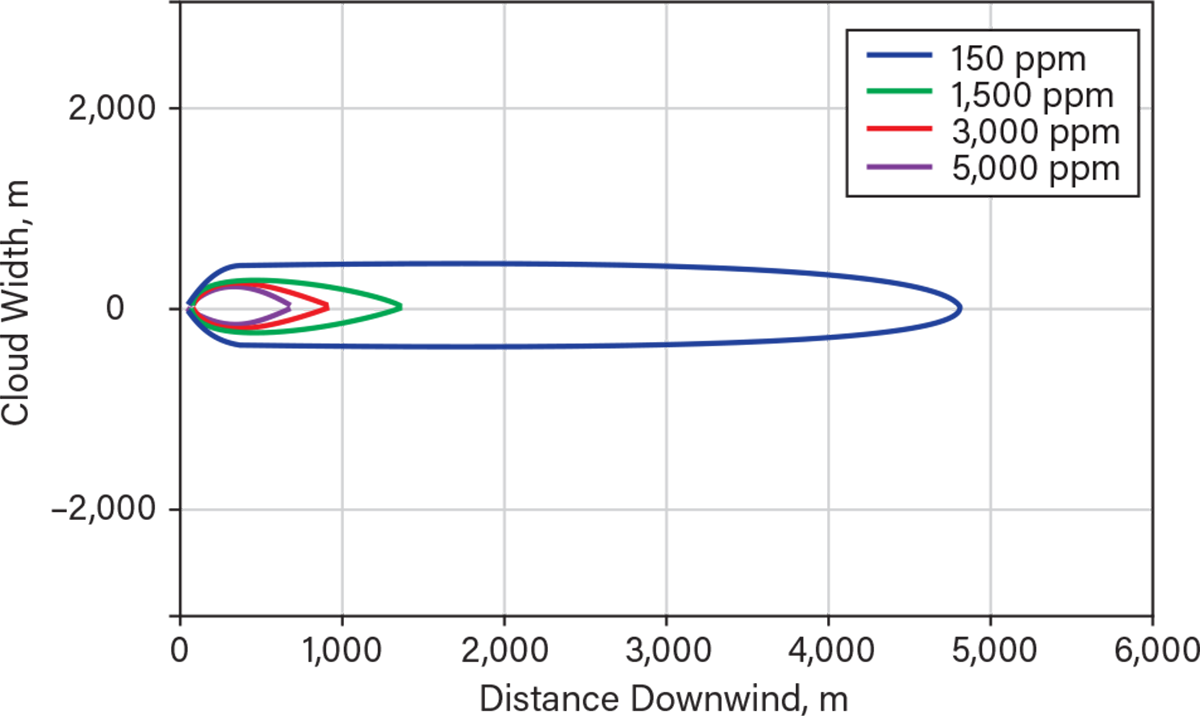
▲Figure 5. This model shows the maximum predicted footprint of various concentration when anhydrous ammonia is continuously released from a 3-in. hose. The extent shown is for neutral atmospheric conditions and 4 m/sec windspeed.
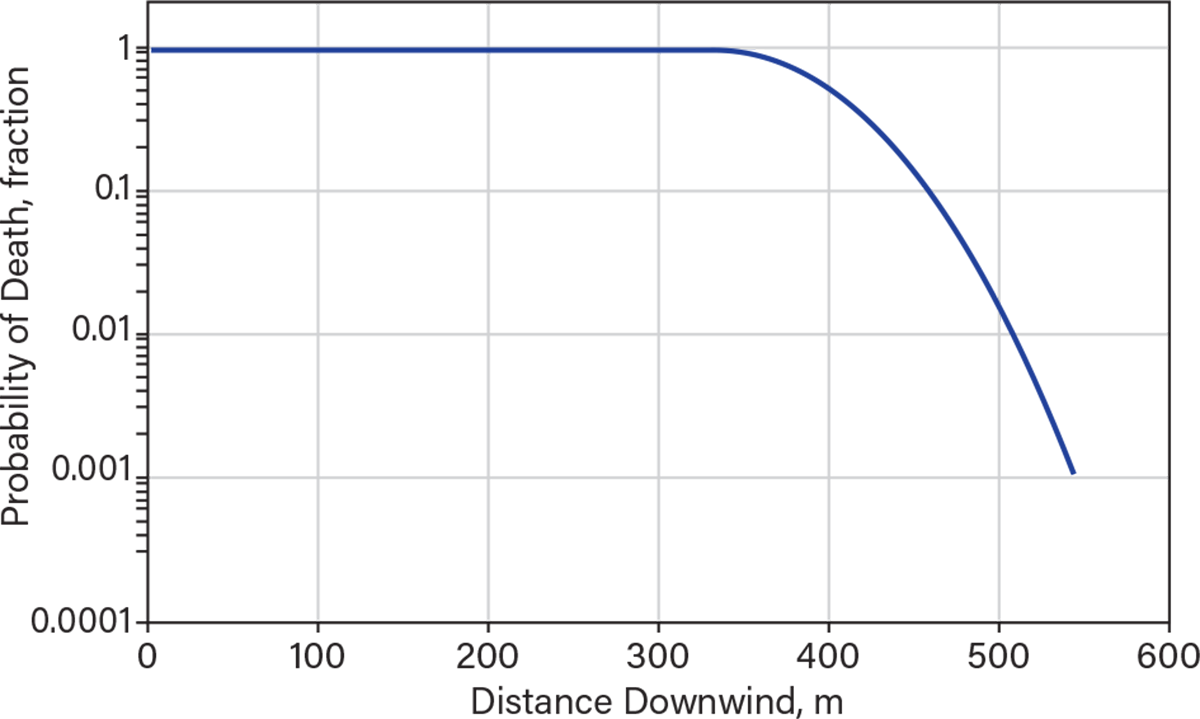
▲Figure 6. This model shows the predicted probability of fatality vs. distance for the continuous release of anhydrous ammonia from a 3-in. hose. The distances shown are for neutral atmospheric conditions and 4 m/sec windspeed.
Based on the proximity of the population near the oil mill that has been reported, it is not surprising that 1,150 people were injured and there were 129 fatalities. Because of a religious holiday (Ramadan), the population was much lower in the surrounding area, especially in nearby schools and restaurants. If this incident had occurred any other day, the injuries and fatalities would have been higher. Using the PHAST model, the number of fatalities that could have resulted from the releases is as high as 700, with the wind blowing out of the north. However, the incident would have been much worse if the winds were persistently blowing toward the residential population north and east of the oil mill.
Lessons learned
A detailed analysis of the causal factors can only be done using evidence (preserved/protected) and related data from the day of the accident. After 30 years, it is almost impossible to reconstruct all the details based on limited data currently available in public literature. However, some general lesson categories (related to technology, operations, management, etc.) and generic causes can still be extracted. Table 3 summarizes lesson categories and high-level causes that can be broadly leveraged to prevent such incidents from happening.
The main learnings from the Dakar accident highlight the need to:
- ensure an understanding of the hazards of anhydrous ammonia under pressure
- properly design fail-safe equipment and their appropriate utilization in production, transportation, and handling
- train operators and emergency responders on possible abnormal situations
- conduct frequent hazard reviews, audits, and assessments aimed at minimizing process risk.
In addition to the primary cause (i.e., overfilling) noted previously, there were many failures in all the categories listed in Table 3: technical; operations; facility/corporate leadership; government oversight; and industrial standards. These are all important for the safe operation of ammonia facilities globally.
An industrial standards organization for ammonia might improve process safety performance in all jurisdictions, particularly in developing countries. For example, institutes exist for other chemicals like chlorine (e.g., the Chlorine Institute, Eurochlor).
In Senegal, anhydrous ammonia continues to be used in large quantities since it is needed to detoxify agricultural commodities (i.e., nut oils) to eliminate aflatoxins. The demand is high and likely to increase over time. However, even two decades after the incident, one Senegalese newspaper called ammonia a “formidable and indispensable killer” (16). As the production and use of anhydrous ammonia increases dramatically in the next few years, lessons from Dakar and other incidents can be effectively used and leveraged to improve the perception of ammonia and promote its safe handling everywhere.
In summary
The Dakar accident that took place on Mar. 24, 1992, is among the worst industrial accidents involving ammonia because it caused 129 fatalities and more than 1,000 injuries. The analysis of the ammonia release scenarios presented in this article demonstrates that under different circumstances, the number of fatalities could have been as high as 700, with the normal daytime population within 500 m of the oil mill.
It has been well argued (4) that accidents like those that occurred in Bhopal, India, and Dakar, Senegal — both developing countries — can also occur in developed countries, even with their more robust regulations and industry standards. Thus, it is essential to continue developing and implementing standards for safe designs, operations, and governance and improving process safety performance at facilities in the CPI, particularly anhydrous ammonia storage and handling facilities as they become more commonplace in the future.
Literature Cited
- French Ministry of the Environment, “Explosion of an Ammonia Tank. Mar. 24, 1992, Dakar,” www.aria.developpement-durable.gouv.fr/wp-content/files_mf/A3485_ips03485_002.pdf (1992).
- The Associated Press, “60 Killed as Truck Carrying Ammonia Explodes in Senegal,” The New York Times, www.nytimes.com/1992/03/25/world/60-killed-as-truck-carrying-ammonia-explodes-in-senegal.html (Mar. 25, 1992).
- Eckerman, I., “The Bhopal Saga. Causes and Consequences of the World’s Largest Industrial Disaster,” Universities Press, Hyderabad, India (2004).
- Gupta, J. P., “The Bhopal Gas Tragedy: Could it Have Happened in a Developed Country?” Journal of Loss Prevention in the Process Industries, 15, pp. 1–4 (2002).
- Atherton, J., and F. Gil, “Incidents That Define Process Safety,” CCPS, John Wiley & Sons, Hoboken, NJ (2008).
- Center for Chemical Process Safety, “More Incidents That Define Process Safety,” CCPS, John Wiley & Sons, Hoboken, NJ (2020).
- Joseph, G., et al., “Lessons After Bhopal: C.S.B. a Catalyst for Change,” Journal of Loss Prevention in the Process Industries, 18, pp. 537–548 (2005).
- FACTS Hazardous Materials Accidents Knowledge Base, “1050 Chemical Accident in Senegal with Ammonia Anhydrous,” www.factsonline.nl/free-example/11050/chemical-accident-in-senegal-with-ammonia-anhydrous (1992).
- Woto-Gaye, G., et al., “Death from Ammonia Poisoning: Anatomo-Pathologic Features,” Dakar Medical, 44 (2), pp. 199–201(1999).
- Code of Federal Regulations, “49 CFR 173.301– General Requirements for Shipment of Compressed Gases and Other Hazardous Materials in Cylinders, UN Pressure Receptacles and Spherical Pressure Vessels,” 49 CFR 173.301, https://www.ecfr.gov/current/title-49/subtitle-B/chapter-I/subchapter-C/part-173/subpart-G/section-173.301 (2023).
- Code of Federal Regulations, “49 CFR 173.314 – Compressed Gases in Tank Cars and Multi-Unit Tank Cars,” 49 CFR 173.314, https://www.ecfr.gov/current/title-49/subtitle-B/chapter-I/subchapter-C/part-173/subpart-G/section-173.314 (2023).
- United Nations Economic Commission for Europe, “ADR: European Agreement Concerning the International Carriage of Dangerous Goods by Road,” UNECE, Geneva, Switzerland (2016).
- American Industrial Hygienists Association, “2020 Emergency Response Planning Guidelines (ERPG) & Workplace Environmental Exposure Levels (WEEL) Handbook,” AIHA, Falls Church, VA (2020).
- U.K. Health and Safety Executive, “Toxicity Levels of Chemicals,” https://www.hse.gov.uk/chemicals/haztox.htm (accessed May 2023).
- DNV, “DNV PHAST Model (Ver. 8.23),” https://www.dnv.com/software/services/phast/index.html (accessed May 2023).
- ENQUÊTE+, “Une Catastrophe Nationale à L’Epreuve du Temps,” https://www.enqueteplus.com/content/accident-de-la-sonacos-du-24-mars-1992-une-catastrophe-nationale-%C3%A0-l%E2%80%99%C3%A9preuve-du-temps (2014).
Copyright Permissions
Would you like to reuse content from CEP Magazine? It’s easy to request permission to reuse content. Simply click here to connect instantly to licensing services, where you can choose from a list of options regarding how you would like to reuse the desired content and complete the transaction.