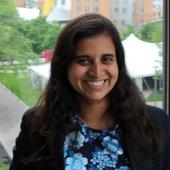
Session Chair:
- Pranav Karanjkar, Dow
Abstracts:
Mixing Liquids of Disparate Viscosities via Drum Tumble
Nate Stelzer, Dow; Margaret Hwang, Dow
Drum or pail tumbling is a common unit operation used to blend low viscosity fluids and/or solids. In this unit operation raw materials are loaded into a vessel which is turned end-over-end until a homogeneous mixture is achieved. This unit operation can be employed to eliminate cleanouts or avoid scenarios where contamination is a concern. Tumble mixing is also a convenient option for mixing at a pilot scale or preparing pre-mixed components prior to addition into a larger vessel.
The primary disadvantage to tumble mixing is the limited amount of mixing power that can be imparted to the vessel contents. This limitation results in longer blend times for higher viscosity products. In systems with high viscosity ratios among the raw materials, homogeneous blend time increases as the viscosity ratio increases. Both scenarios are particularly challenging for tumble mixing because there is no agitator to forcibly interlace raw material phases.
This poster highlights techniques that can be used to reduce blend time in systems with high viscosity ratios. Recommendations are made for selecting optimal rotation speed and mixing process. A case study is discussed which utilized these techniques to improve batch homogeneity during the scale-up of a new commercial product.
This poster highlights techniques that can be used to reduce blend time in systems with high viscosity ratios. Recommendations are made for selecting optimal rotation speed and mixing process. A case study is discussed which utilized these techniques to improve batch homogeneity during the scale-up of a new commercial product.
Smart Sourcing of Complex Raw Materials
Lisa Berrie, Dow
Consistent growth of silicone MQ resin intermediates over the past 70 years eventually drove the development and installation of a new production plant for these critical materials. MQ resins can be produced by either the ethyl silicate route or the sodium silicate route. MQ resin materials were historically sourced from North America. Market trends indicated a need to diversify the supply chain, and new production was established in Asia.
A critical technical risk for the project was the qualification of local raw material suppliers to retain a manufacturing cost advantage. Qualification of many of the raw materials was straightforward due to ample supply and well-defined quality characterization requirements. However, a select raw material required significantly more focus due to its contribution to final product quality.
This poster summarizes the approach taken to identify, qualify, and implement a local supply of this critical raw material in Asia. The global, cross-functional team identified potential suppliers and down selected to the top candidates through a collaborative screening process between procurement and R&D. These materials were tested in various R&D labs across the globe and resin product samples were tested in application. The team audited the top suppliers’ production processes and documentation practices and performed a gap analysis. Finally, material from the top supplier was trialed on the historical process to validate performance at full scale.
The new process started up successfully, immediately producing high quality MQ resin intermediate. This process development example demonstrates the importance of early stage resource investment and open collaboration across functions and geographies.
Development and Scale-up of a Crystallization Process for a Kinetically-Unfavorable Polymorph
Yamini Krishnan, Corteva Agriscience; Navraj Hanspal, Corteva Agriscience; Nicole Hough, Corteva Agriscience; Paul Larsen, Corteva Agriscience; Christian Lowe, Dow AgroSciences; Patrick McGough; Abraham Schuitman, Corteva Agriscience; Joe Wei Corteva Agriscience
This work describes the development and scale-up of a crystallization process to isolate a thermodynamically stable but kinetically unfavorable polymorph of a small organic agrochemical prone to oiling. The process involves simultaneous addition of solution and antisolvent into a slurry of the desired polymorph. For this system, the process is more robust to feed variation than a traditional antisolvent process and affords suitable polymorph control, recovery, cycle time, and purity. However, the process produces a thick, but shear-thinning slurry of fine, needle-like particles that is challenging to mix well. Mixing analysis tools, including both the Fluid Mixing Processes (FMP) Design Guide and computational fluid dynamics simulations were utilized to enable successful scale-up of this mixing-sensitive process from lab to pilot plant.
Development and demonstration of an ultra-high-temperature continuous racemization process
Kiersten Campbell, Snapdragon Chemistry
Herein we describe a continuous flow process for the thermal racemization of an undesired atropisomer to facilitate recovery of the desired form from the racemic mixture. A kinetic model was developed with the ability to predict the degree of racemization at varying temperatures. The high activation energy for the process required it to be carried out over 300°C under continuous flow conditions using a superheated solvent stream at >20 bar back pressure. Process safety was a key factor in the reactor design due to the extreme operating conditions and a potential thermal event observed during the characterization work. The process was demonstrated in a lab-scale (~100 mL) tubular reactor before being scaled up to a custom-built pilot-scale (~1 L) reactor that processed >15 L of feed in a day. Following the reaction, the product was recovered via cooling crystallization as a high purity racemic material suitable for further processing.
Islatravir Crude Isolation Development and Scale-up: Late-Stage Shift from Filter Dryer to Centrifuge to Mitigate Risks from Enzyme Filtration
Brittany Dobson, Merck & Co., Inc.; Margaret Miller, Merck & Co., Inc.; Daniel Bishara, Merck & Co., Inc.; Matthew Gunsch, Merck & Co., Inc.; Michelle Cleary, Merck Sharp & Dohme; David Bell, Merck Sharp & Dohme; Aisling Prendergast, Merck Sharp & Dohme; Ivan Lee, Merck & Co., Inc.; Darryl Chang, Merck & Co., Inc.; Sandra Robaire, Merck & Co., Inc.; Nick Rogus, Merck & Co., Inc.; Ted Furman, Merck & Co., Inc.; Gregory Hughes, Merck & Co., Inc.; Elizabeth Fisher, Merck & Co., Inc.; Kevin Maloney, Merck & Co., Inc.; Junyong Jo, Merck & Co., Inc.; Paula Archbold, Merck Sharp & Dohme
Islatravir is a nucleoside reverse transcriptase inhibitor small molecule targeted for HIV. Islatravir is synthesized through a biocatalytic cascade using nine enzymes and has a single isolation. As such, the filtration was known to be challenging from the start of process development due to the presence of enzymes and proteins. Denatured enzymes can settle and clog the filter, resulting in elongated filtration times and limited rejection of residual proteins. Reducing enzyme loading levels and adding a filter aid were explored during early development to improve filtration efficiency in the filter dryer. These process modifications resulted in initial success as the process was scaled up from bench scale to the pilot plant. During further scaleup, the filtration progress became significantly slower, requiring days to complete the filtration. This highlighted both operational and quality risks long term for the process. This led to the decision to pursue a late-stage process change from a filter dryer to a centrifuge. This prompted the team to initiate rapid lab development to understand and mitigate concerns around differences between the two pieces of equipment pertaining to compressibility, washing, and temperature control. Centrifugation can be challenging to adequately evaluate at the lab scale due to the dependence on basket size and changing liquid height as the driving force. Dynochem modeling was leveraged to bridge the gap between bench and pilot scale to inform operating conditions for initial pilot scale batches. The pilot scale demonstration investigated a range of operating parameters and derisked the initial processing concerns, clearing the way for implementation of the process at commercial scale. The work culminated in the successful utilization of the centrifuge at manufacturing scale, achieving reproducible filtration performance across multiple batches, isolated product of desired quality, and additionally a significant reduction in drying cycle time.