Effective commissioning is critical to realizing the benefits of new equipment. As many facilities transition to smart technologies, this process requires even more diligence.
What Is Commissioning?
Commissioning includes various activities that take place after equipment is installed. During installation commissioning, tests are performed to demonstrate that an installed component or subsystem functions as designed. Operational commissioning includes tests to demonstrate that components or subsystems operate in an integrated fashion to achieve overall system functionality.
These commissioning efforts do not ensure that the installed system will function according to the investment rationale that considered throughput, cost, quality, reliability, and safety, given day-to-day variations in the production environment. Rather, performance (or production) commissioning ensures, before the supplier leaves the plant, that the new equipment can sustain function that meets the business objectives that justified the investment. Commissioning requirements are defined early in a project, and each phase of equipment design informs a related phase of commissioning.
To avoid confusion, commissioning in this article refers to performance commissioning, which includes all of the activities required to make a fully functional, integrated system ready for sustained production, and sustained production implies that the system fully meets the original investment rationale for the capital expenditure.
Many older facilities that invest in data analytics, advanced sensors and controls, and other smart technologies may find that the benefits of these assets take months or more to realize. It is not the technology that is causing problems, but rather how the technology interacts with everything around it.
The purpose of smart technology is to drive performance improvements through better connectivity, communication, and coordination of activities. Data from one process informs another, allowing each to adapt to changing conditions. Adjacent processes must be designed to exchange information to benefit each other. When a breakdown occurs in this communication, even smart technologies can be ineffective.
This interdependency between new smart equipment and the surrounding legacy business ecosystem is difficult for many production teams to anticipate when specifying equipment. It is often not until system integration occurs that disconnects are observed. If issues are not anticipated and addressed in a coordinated manner, they can cause disruptions in throughput, quality, and uptime.
Commissioning activities can stress-test and resolve any disconnects caused by the new capabilities offered by smart machinery. In many cases, however, this requires us to challenge existing business conventions.
Develop better success metrics. Smart equipment that is designed for cost efficiency may not address key interdependencies, such as consistency of incoming material properties. Acceptance tests will likely only confirm basic functionality, so commissioning should focus on the equipment’s impact on adjacent business activities.
Consider information lost in handoffs. Because handoffs during the sourcing process often obscure the intended business performance of the capital investment, information about the rationale for the investment can get lost. If the equipment is simple or has very little connection to other business functions (such as the purchase of a new band saw), the impact may be minimal. However, smart technologies promise transformative capabilities that are tied to the broader organization. Commissioning plans should consider proof of business performance outcomes, not just equipment functionality.
Account for inadequate specifications. The engineering discipline has seen a gradual loss of deeply experienced staff due to an aging workforce that was not replenished in the 1990s when manufacturing employment dipped. This lack of experience has revealed itself in specifications that have errors of omission. The potential for omissions in smart technology specifications is higher, as many of the interdependencies require a more complete understanding of business operations. Less-experienced engineers may capture key technical requirements, but they might overlook the impact equipment has on adjacent business functions (e.g., maintenance, scheduling, information technology). By developing more comprehensive commissioning plans, omissions in specifications can be exposed before production starts and while suppliers are still engaged contractually.
Contract for flexibility. Purchasing contracts are set up to pay suppliers upon completion of tangible deliverables. Commissioning smart technologies can involve many intangibles related to human skills, production schedules, information assets, environmental conditions, and material properties. Because it is difficult to consider intangibles in a fixed-price contract, the commissioning phase of delivery — where issues related to intangibles are most likely to be exposed — should be contracted more like a consulting service.
This article provides guidance for successful smart equipment commissioning, which can deliver cost, quality, and performance benefits, but only if commissioned properly.
Develop better success metrics
Most capital sourcing efforts are driven by cost efficiency, for good reason. With more competitors in each market, buyers can find multiple, high-quality suppliers to choose from. Any reduction in cost through competition favors the bottom line. For less-complex equipment, this is a sound strategy.
But, when smart technologies are integrated with various business processes, elements of the supply chain, other equipment, information systems, and human behavior patterns, the cost of an unanticipated deviation or performance gap can exceed the funds spent on the equipment. In addition, legacy production systems are not typically designed for the speed, quality, or cost improvements offered by smart technologies.
To better account for the impact of a complex capital investment, financial models must consider new interdependencies. Capital approval processes take a simplistic view of labor, quality, and material cost. A typical justification might claim that automating a process will increase throughput with no additional labor. As attractive as that might be, it greatly understates the eventual scope of the investment.
Many legacy manufacturing processes are designed to leverage low-cost labor. When automation replaces manual processes, the burden on operators shifts from physical activity to mental. For a manual process, an operator with dexterity and the will to work diligently will be effective. That same operator may not have the skills required to operate equipment that needs more monitoring and adjusting than physical manipulation. In reality, many smart manufacturing systems require higher-cost labor, but that labor becomes a lower marginal cost because of higher throughput and quality.
Commissioning plans must be aligned with the right success metrics. For complex systems with interdependencies across the business, the success metrics must consider strategic objectives beyond ensuring that the equipment simply fulfills the scope and meets a budget and schedule.
Consider information lost due to handoffs
Handoffs of responsibility and information from one group to the next are an inherent part of any capital equipment sourcing process. Business leadership identifies a need and the financial rationale for a capital project and delegates execution to engineering and sourcing experts. Engineering and sourcing decompose the request into a set of actions and then contact a supplier. The supplier ships and installs the equipment, but then hands it off to the operations team.
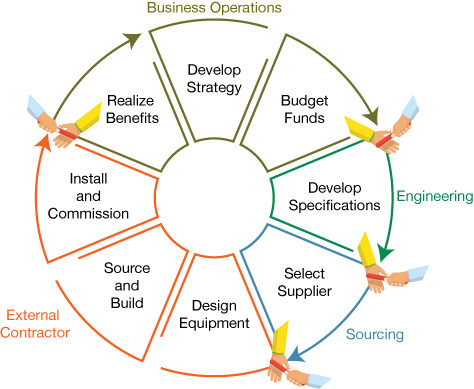
▲Figure 1. Information continuously passes between parties during equipment sourcing and commissioning, which can obscure the original rationale for the investment.
In each handoff, one party provides information to the next, and the party providing the information typically understands it better than the party receiving the information (Figure 1). For example, business leadership may provide a request for capital investment to an engineering team. The engineering team is tasked with developing a specification, but the team may not be privy to the details of the strategy behind the investment. Engineers do not typically develop financial models that calculate internal rate of return (IRR) or outline burdened labor costs. Instead, engineers rely on throughput capacity, number of operators to be allocated in production, and expected uptime to develop a specification. The engineers will identify process parameters, mechanical design constraints, and control strategies. They provide that information to sourcing, which will do their best to interpret those details before contacting suppliers.
Each handoff in the process strips away critical details. By the time the supplier finishes installing equipment designed and built to the engineering specifications, the original investment rationale is hidden a few steps behind. As a result, commissioning is typically aligned with the only good information available — the specification.
Few specifications are developed to accommodate the broad impacts that smart technologies have on business functions. Instead, specifications usually only capture the independent functions of the new equipment. By planning for more comprehensive and system-oriented commissioning, the information gaps created during handoffs can be identified and addressed earlier in the sourcing process.
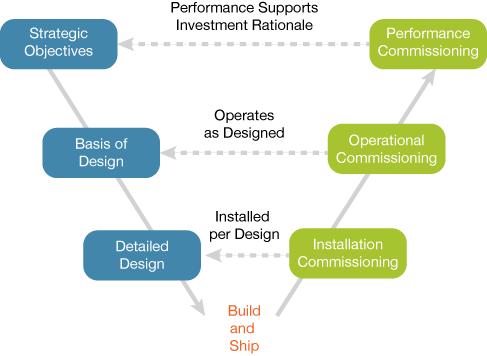
▲Figure 2. Each phase of commissioning has its own objectives. Installation commissioning ensures that the equipment is installed as designed; operational commissioning validates that the equipment operates to satisfy the design basis; and performance commissioning, which is critical to smart equipment, ensures that the investment rationale is met.
Equipment requirements defined at each stage of the design process align with different phases of commissioning (Figure 2). Detailed design captures functional requirements that are proven as part of installation commissioning. These details might include the sequential operation of valves or the measurement of temperature, but do not necessarily require processing of material.
The basis of design (also referred to as the design concept) outlines performance capabilities that must be demonstrated as part of operational commissioning. To successfully complete operational commissioning, the system must process material using established parameters, under the control of operators. Typical performance characteristics validated in operational commissioning include cycle time, quality, and throughput.
Strategic objectives establish the investment rationale for the system, including those related to finance, quality, and delivery. Strategic objectives are demonstrated as part of performance commissioning, in a real-world setting subject to normal random conditions. Depending on the system being commissioned, it may take weeks or months to show that the system is capable of meeting expected benefits.
Account for inadequate specifications
Engineers are often responsible for implementing production systems — balancing people, methods, equipment, materials, and funding to achieve output. They translate business strategy into execution in the manufacturing environment. In the capital investment process, engineers capture and transmit strategic objectives through specifications. When companies lack sufficient experienced engineering staff, specifications can suffer from errors of omission and the realities of the production environment may not get properly documented.
The realities that impact sustained production involve operational noise factors, which typically relate to environment, infrastructure, human factors, equipment condition, materials, degradation effects, or interdependencies. Smart technologies are particularly sensitive to sources of operational noise. For instance, batch reactions that rely on advanced sensors to tightly control batch properties can be significantly affected by irregular calibration cycles, confounding advanced algorithms. Identifying and documenting such noise factors demands a deep understanding of the process being specified. Inexperienced engineers can easily miss key factors. Moreover, most site acceptance tests evaluate a very limited set of variabilities that may not reveal these issues until the new system is put into production.
A well-designed commissioning plan can account for any oversights, anticipating sources of variability and giving the operations team and suppliers time to fix issues before they disrupt production. During commissioning, a design of experiments (DOE) approach should be followed to find conditions that are less stable. This involves varying process inputs to stress equipment and evaluate the reaction, focusing attention on critical performance gaps.
If sensor calibration is determined to be a critical factor, commissioning tests can be designed to show how drift in sensor calibration impacts batch properties. These tests can help focus operational support staff, such as the maintenance team, on the tasks that are most critical to achieve high-quality production.
Contract for flexibility
A typical capital equipment contract has payment milestones aligned with project deliverables, including conceptual design review, long-lead materials ordering, detailed design review, successful factory acceptance test, and successful site acceptance test. Equipment purchases that involve less uncertainty will benefit from this kind of contract structure, as it allows aggressive scope, cost, and schedule management by the procurement team.
Smart technology that involves the integration of disparate business functions, however, requires demonstration of more than mere equipment function. The interactions between business functions, which may not be obvious, must also be demonstrated. For example, frequent changeovers in a chemical processing line driven by production schedules can significantly reduce expected throughput. Contracts that do not anticipate these uncertainties can allow suppliers to exit the equipment startup too soon, leaving operations staff to identify performance gaps during production.
At the successful completion of site acceptance tests, suppliers should receive payment for delivery. However, the contract should demand their active engagement during a set of stress tests aimed at showing the equipment is capable of sustained, high-quality, and high-rate production, subject to normal production variations. Variations incorporated into performance commissioning tests might include:
- 24/7 operation with operators of different skill levels
- deliberate interruption of power, water, or air pressure
- variations in batch size or material flowrates
- operation of equipment beyond preventive maintenance intervals
- operation at a turndown ratio that is outside of specification
- loss of communications with host servers.
These variations are particularly important when introducing smart technologies to manufacturing environments that have been running legacy processes.
Developing a contract for the performance commissioning phase of equipment procurement demands a level of partnership between the buyer and supplier. Experimentation during commissioning tests can yield uncertain results. Engaging the supplier more like a consultant during this phase of the project enables more flexibility and allows the supplier to act as a production resource. These services can be difficult to deliver within a firm fixed-price contract structure. Contracting for these services on an hourly basis allows the supplier’s expertise to be engaged only when and where needed.
Rethink commissioning
Smart manufacturing technologies promise a new level of performance for producers, but these technologies are often installed in legacy production systems that are not designed to leverage those benefits. By definition, smart technology demands connectivity of digital and operational systems. In manufacturing environments that have operated without connectivity, introduction of new technology can be disruptive.
It would be ideal for a business starting on the journey toward smarter manufacturing to upgrade all of its systems and staff at the same time to make the transition easier, but that is not always possible. (Read “Smart Manufacturing: Hope or Hype?,” in the June 2019 CEP for more guidance on transitioning to smart manufacturing.) Facilities need to start somewhere, and effective commissioning is a good first step in assuring the potential benefits of smart technologies are realized.
Copyright Permissions
Would you like to reuse content from CEP Magazine? It’s easy to request permission to reuse content. Simply click here to connect instantly to licensing services, where you can choose from a list of options regarding how you would like to reuse the desired content and complete the transaction.