Steel is the backbone of the modern world. The iron-based alloy is essential to construction, transportation, and many other activities tied to higher living standards. However, the iron and steel sector is a major source of carbon dioxide emissions, which are destabilizing the Earth’s climate.
The sector generates 3.7 gigatons of CO2 directly and indirectly each year — 10% of the global total. Existing iron and steel production methods require high temperatures of around 1,600°C, typically achieved by burning coal. Predominant steel production methods also rely on high-carbon coal (coke) as a chemical reactant for reducing iron oxide to iron metal. Approximately 90% of the steel industry’s CO2 emissions occur during pyrochemical reduction of iron oxide (ore) into iron metal in blast furnaces and direct reduction furnaces.
However, decarbonizing iron and steel production is more complicated than removing coal and other fossil fuels from the production process. High-temperature alternatives to coal-based iron and steel production — such as hydrogen-fueled direct reduced iron (DRI) — require high-grade iron ores, which are projected to be in short supply by the end of this decade.
This shortage may impose technical and cost challenges that will likely slow the phase-out of coal and other fossil fuels from the iron and steel sector. To speed up the decarbonization of iron and steel, it is critical to find new production methods that are both carbon-free and compatible with more abundant, lower-grade iron ores.
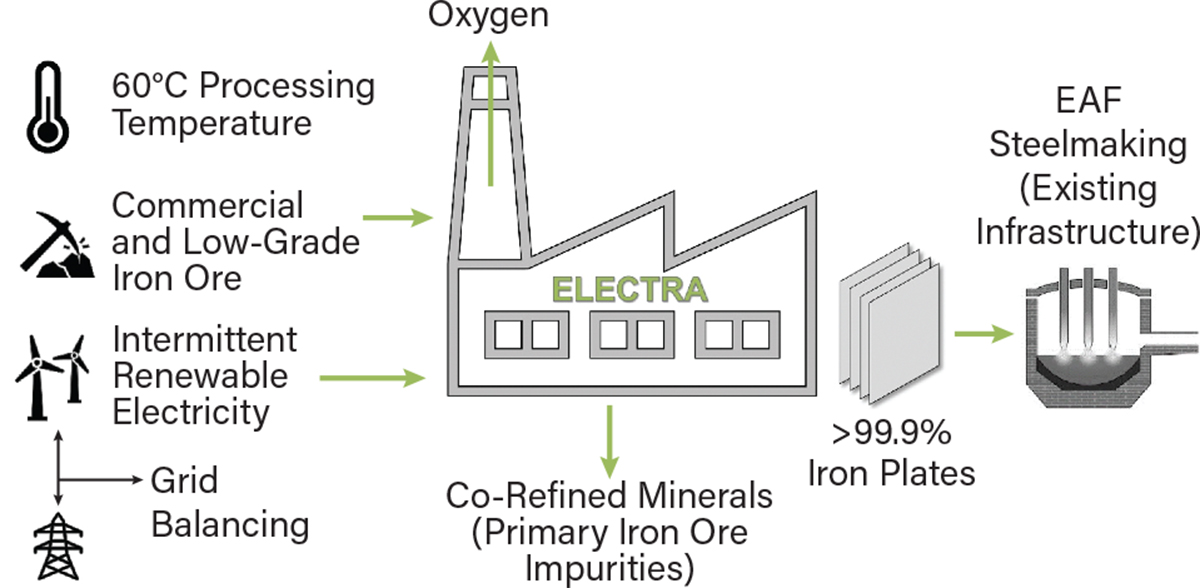
▲ Low-temperature iron (LTI) can be produced using a novel process that dissolves low-grade iron ores in solution. Iron can be electroplated from the solution, taking advantage of intermittent renewable electricity. The resulting iron plates can be upgraded to steel using existing electric arc furnace (EAF) technology.
Electra (formerly ElectraSteel), a Colorado-based cleantech start-up supported by the U.S. National Science Foundation (NSF), has pioneered an electrochemical process for refining iron ore into pure iron that addresses both of these challenges, while operating at dramatically lower temperatures. The process is designed to work with low-cost intermittent renewable electricity and cheaper, low-grade iron ores to produce low-temperature iron (LTI).
Electra Co-Founder and Chief Technology Officer Quoc Pham led a team of scientists and engineers to develop a new understanding of iron ore dissolution kinetics and a novel electrochemical regeneration scheme that enhances iron ore dissolution and increases the efficiency of iron extraction. Instead of heating and smelting the iron ore, Electra’s process dissolves the ore in a water-based acid solution. Next, electricity is used to electroplate iron with >99.9% purity from the solution while regenerating all chemicals and water used in the process. Unlike incumbent processes that emit CO2, Electra’s process releases only pure oxygen.
The electroplating takes place around 60°C — the same temperature as a cup of coffee. Electra’s LTI, also called green iron, can then be converted to green steel using the existing and growing infrastructure of electric arc furnaces that are currently used to recycle scrap steel.
“We are excited to partner with Electra and its revolutionary process to produce emission-free iron,” says Leon Topalian, Chair, President, and Chief Executive Officer of Nucor Corp. “Just as Nucor changed the face of the steel industry 53 years ago with our first electric arc furnace, successfully developing and scaling up a zero-carbon iron product is the type of transformative technology that could change the steel industry as we know it.”
“Electra plants can start and stop production quickly due to low operating temperatures,” says Pham. “This is highly compatible with intermittent renewable electricity, which is increasingly available at under $20/MW-hr. Combined with the use of low-cost, lower-grade ores that cannot be used economically in steelmaking today, electrifying ironmaking is economically feasible with no market-distorting green premium for the first time.”
Initially, Electra’s technical team demonstrated the process at bench scale by producing iron plates that were 2 cm2 in size, and they have since scaled up 200 times. In 2023, Electra aims to complete an integrated pilot plant that will produce iron plates approaching 1 m2 in size. The company anticipates building a commercial-scale plant in the second half of this decade, with production costs at scale that are the same or less than today’s fossil-fueled technologies.
This technology was partially supported by the NSF Small Business Innovation Research (SBIR) program.
This article was prepared by the National Science Foundation in partnership with CEP.
Copyright Permissions
Would you like to reuse content from CEP Magazine? It’s easy to request permission to reuse content. Simply click here to connect instantly to licensing services, where you can choose from a list of options regarding how you would like to reuse the desired content and complete the transaction.