Sections
State-of-the-art manufacturing facilities, digital communication, and advanced engineering techniques are making modular process plants more sustainable than ever.
Sustainability efforts in the chemical process industries (CPI) have traditionally focused “inside the pipe” — making the process chemistry more benign, using renewable sources for raw materials, and designing products with end-of-use recycling in mind. In fact, eight of the twelve principles of green engineering — and the first six — relate directly to the process itself, not to the plant (1). This focus ignores the work being done to make the design, fabrication, installation, operation, and eventual decommissioning of process plants more sustainable.
This article discusses how to design sustainable process plants, with a special focus on the benefits of modular plants, in which each unit is built offsite, skid-mounted, and shipped to the site where they are integrated and connected to site utilities (2). Designing process plants to be modular can decrease labor costs and environmental impact while increasing the flexibility of the facility. Modular plants can offer many benefits over conventional stick-built facilities (i.e., assembled in place at the final operating site), such as sustainability, schedule efficiency, and worksite safety. This article highlights the many ways that modular plant design is being used to improve sustainability, reduce environmental impact, and enhance safety of process plants.
Reuse, retrofit, and relocate: Benefits of going modular
Introducing flexibility through modular design. Process modules display plug-and-play capability as they are readily interchangeable. In flow chemistry plants in the pharmaceuticals, biotech, and specialty chemicals industries, this trait allows process modules to be used in multiple locations and in different plants if the platforms are compatible (Figure 1). The major advantage of this approach is that a single plant can run multiple processes through the flexible configuration of the process modules. This flexibility decreases equipment costs while reducing the environmental impact of the process by decreasing the total amount of newly built equipment.
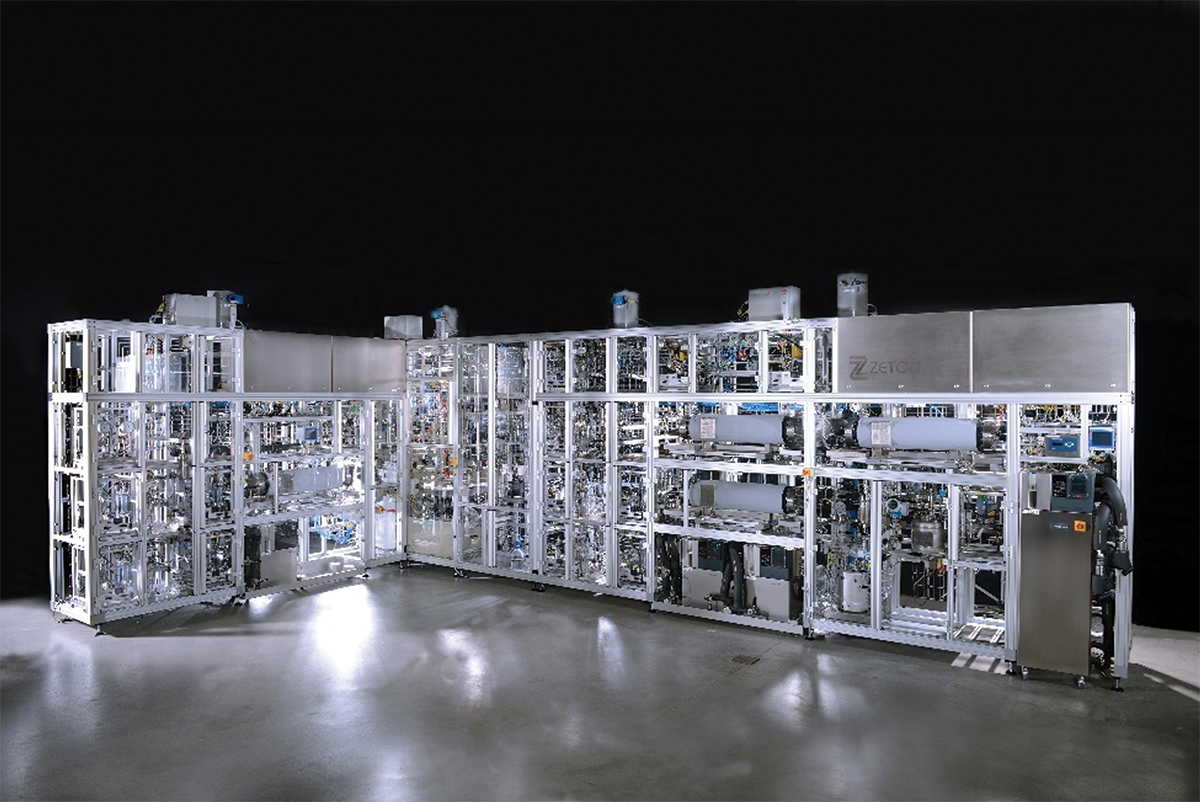
▲Figure 1. Modular processes often have plug-and-play capability — i.e., interchangeable process modules — like this pharmaceutical flow chemistry plant. Here, the modular design facilitates installation and reduces the process footprint.
Another example that demonstrates the flexibility of modular design is the plant-in-a-box concept, where the building is integrated directly with the modular skid structure. In the case of the biomass pyrolysis production plant shown in Figure 2, the exterior skid structure provides the structural support for the building. This innovative design reduces the quantity of steel and concrete required for construction and simplifies the civil work onsite.
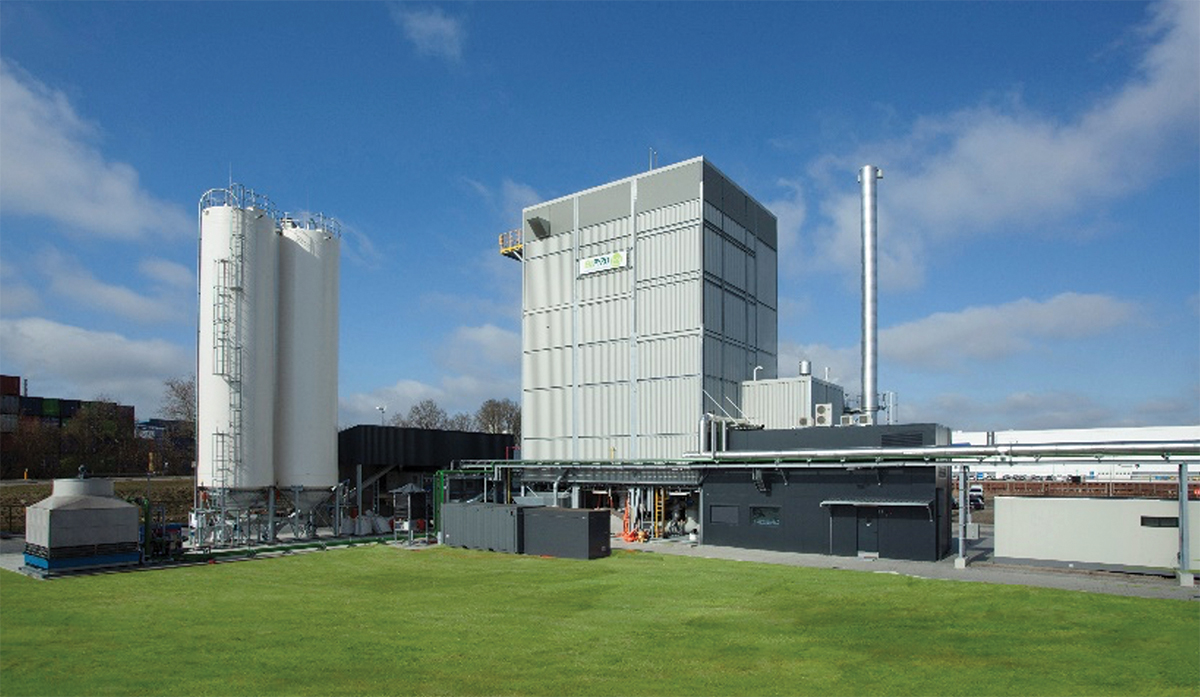
▲Figure 2. This biomass pyrolysis plant uses the plant-in-a-box building concept, as the building’s external walls are directly integrated with the modular skid structure.
Mitigating environmental threats. Stick-built plants face many environmental challenges, including stormwater pollution, site erosion, construction site runoff, crew housing and sanitation issues, diesel generator requirements, problems related to mobile diesel-powered cranes, and uncontained volatile organic compounds (VOCs), to name a few. These issues are inherent to building a plant fully onsite, as opposed to having each unit shipped to the site skid-mounted and ready for installation. These challenges can be either partially or entirely mitigated by modular fabrication in a dedicated shop (Figure 3). Furthermore, the quantity of waste material generated over the course of a project is significantly reduced, as any leftover material from one project can be used on future projects.
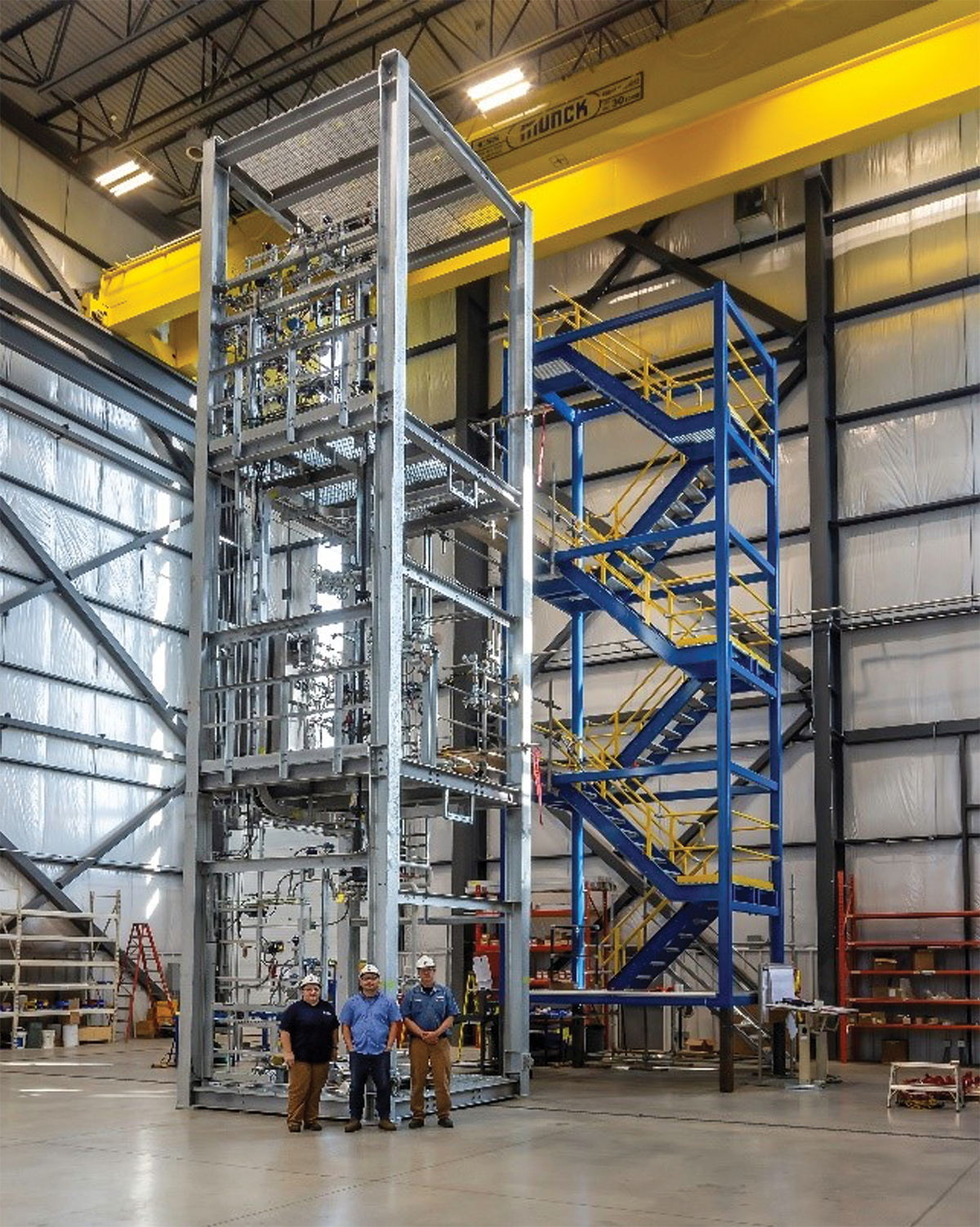
▲Figure 3. Modular process units are often constructed offsite and reassembled or installed at the final facility location. Fabricating the unit on a modular skid reduces construction time and cost, as well as the potential risk to employees.
With appropriate resources in place, reassembly of the completed process plant modules at the site typically takes days or weeks, not months. This serves to minimize neighboring plant shutdowns due to site construction activity. Plant shutdowns increase energy consumption, raw materials usage, and waste generation from existing operations, so minimizing plant shutdowns by implementing a modular fabrication approach has a significant environmental benefit.
Increasing workplace safety. Operating sustainably and protecting the health and safety of staff should be central tenets for every company. These two goals are intertwined, and modular fabrication can improve both.
An indoor shop environment is an inherently safer workplace than outdoor site construction. For example, inclement weather is not a factor as the shop is climate-controlled during the winter and summer months, which improves worker productivity. Cranes run overhead — not at ground level — and they are electric, which eliminates diesel exhaust fumes. A well-lit workplace with excellent housekeeping and enhanced building security all contribute to improved working conditions and enhanced health and safety performance.
During skid reassembly on site, the optimized plant footprint facilitated by modular design allows for a well-defined and well-controlled construction area, enhancing the safety of site personnel as the process plant modules are lowered into place (Figure 4).
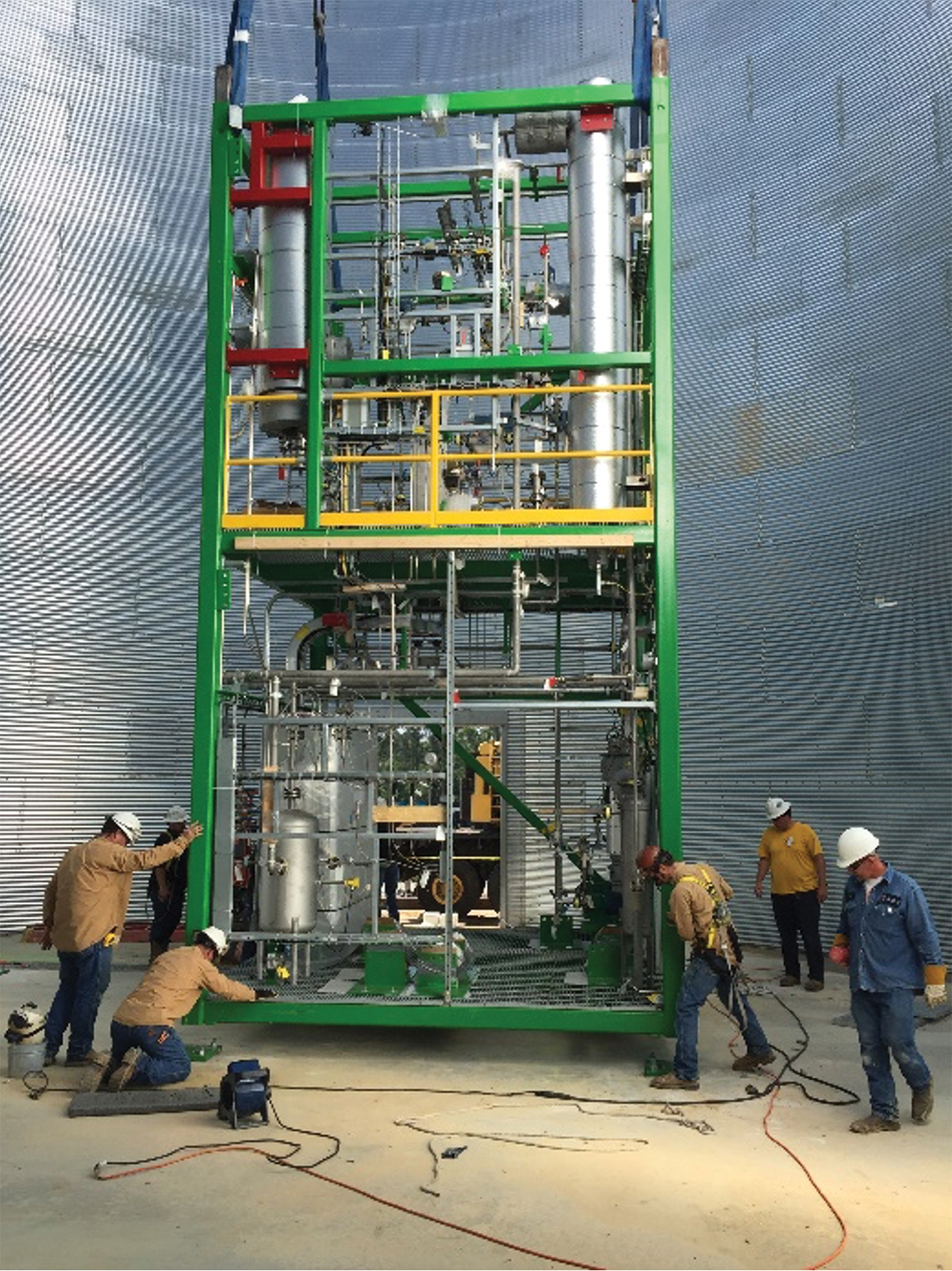
▲Figure 4. Installing a prefabricated process module is often safer for workers than the more traditional route of stick-building a plant at the site.
Going paperless in plant design
One strategy that many companies and organizations implement to improve sustainability is to reduce the amount of paper used in the design workflow. By implementing paperless design documents over the past decade, Zeton has significantly reduced the amount of paper and toner used by its engineers (Figure 5). Examples of the company’s actions to become primarily paperless include:
- Software (e.g., BlueBeam) is used to review and mark up piping and instrumentation diagram (P&ID) PDFs from anywhere. Design engineers no longer need to carry hardcopy drawings to offsite client meetings. The technology is intuitive, and comments and changes are securely captured online in real-time for formal redrafting at a later date.
- The manufacturing progress of modular plant projects is tracked using a system of project metrics. Metrics are recorded and updated wirelessly using an iPad running a custom database application developed in-house. The data is stored securely on a local server; the iPad is an operator interface, and no data is stored locally on the device. Project managers can view the project metrics in real-time and relay the percent complete to customers. This not only reduces paperwork but also helps ensure modular plant projects stay on schedule by showing progress clearly and efficiently.
- Modular process plants are highly optimized during the design phase, as the dimensions of each unit are well-established during plant design and layout. Plant designers generate detailed plant 3D models (e.g., in AutoCAD Plant 3D) that they export to a free-to-download viewer (e.g., Autodesk Navisworks 3D) so the designs can be shared with customers. This allows for detailed layout reviews at the 30%, 60%, and 90% design stages before the plant enters manufacturing.
- 3D scans of modular plants during fabrication (e.g., using Matterport) reduce the frequency of in-person customer visits and allow for a detailed review by a greater number of client team members. To initiate a new scan, a project team member walks through the skid while holding the Matterport camera in front of them, and the camera automatically captures a 3D image of the plant. 3D scans proved invaluable during the pandemic lockdowns and allowed projects to continue.
- As an alternative to printing many layout drawings, loading the latest 3D model onto computers on the shop floor allows craft technicians to view the model in real-time, which significantly reduces paperwork, manufacturing downtime, and unnecessary rework.
- Virtual meeting platforms have revolutionized the way project meetings are carried out, and this also extends to factory acceptance testing, which was carried out remotely during COVID-19 lockdowns (Figure 6).

▲Figure 5. To meet sustainability goals, many companies are streamlining operations and going paperless. These six examples of paperless operations maximize the use of digital communication in the design of modular process plants.
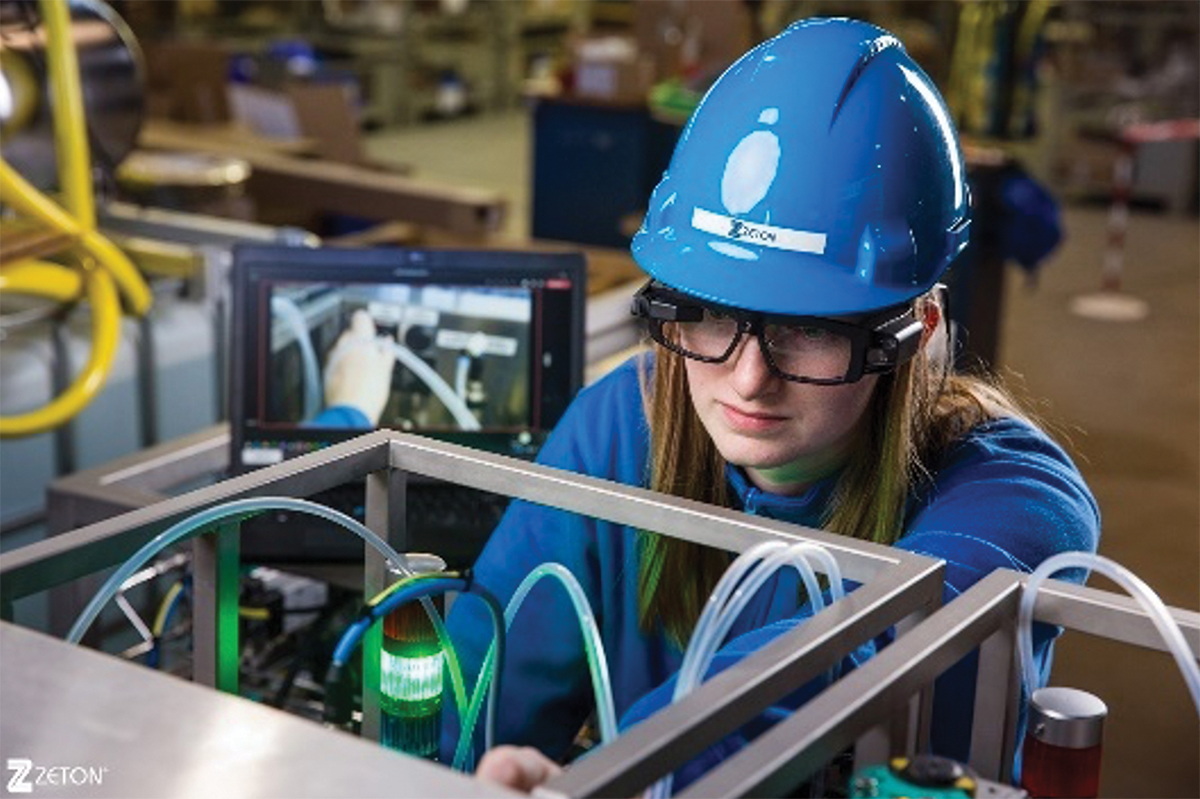
▲Figure 6. Factory acceptance testing can be carried out remotely via a direct video link.
Sustainable plant fabrication and delivery
Sustainability in manufacturing extends from how the process plant is designed to where the plant is constructed.
Modular skids are typically constructed in large, purpose-built factory buildings. Beginning with the factory’s layout and design, large vertical windows incorporated into the building design introduce more ambient light into the shop, improving working environments for staff and lowering lighting costs in the event a bay is temporarily unoccupied (Figure 7). Typically, this happens between projects, after one plant has shipped and before the next project starts. Another example of sustainable plant design is the use of light-emitting diode (LED) lighting in factories, which has replaced high-pressure sodium lamp technology as the lighting of choice.
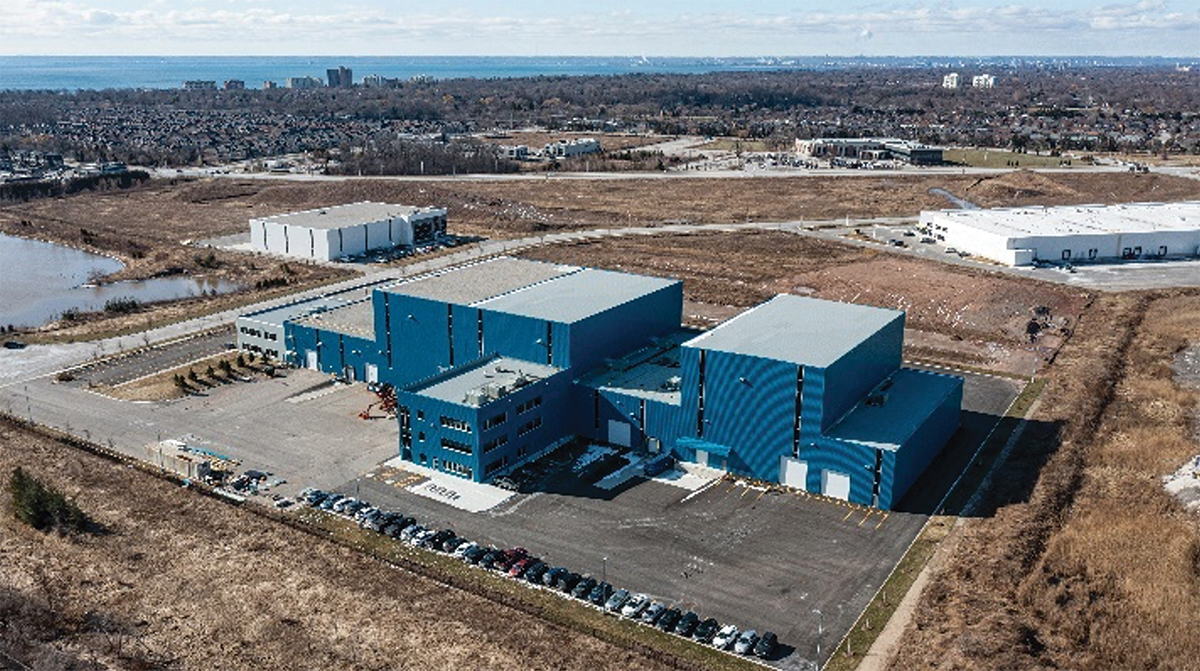
▲Figure 7. Large vertical windows were incorporated into Zeton’s building design to introduce more ambient light. Increasing passive lighting reduces energy consumption and improves working spaces.
As the factories are permanent structures, they can deliver multiple modular plant projects with minimal retooling between projects. From a sustainability viewpoint, this is superior to stick-built projects where a temporary construction site is erected and dismantled with each project. This permanency opens the door to additional sustainable features like rooftop solar power generation, electric vehicle charging stations, and xeriscaping — landscaping with slow-growing, drought-tolerant, and native plants to conserve water and reduce yard trimmings.
When fabricating modular units, tubing and compression fittings can be installed for certain applications with pipe sizes of 0.5-in. and below, rather than piping. The material weighs and costs less than metal piping and fittings, and the manufacturing labor costs to install tubing are lower. Also, the ease of future modification is greater as hot work permits are not required for tubing systems, whereas they typically are for welded piping systems. This additional benefit — ease of modification — is especially important for pilot plant and research and development (R&D) projects. Half-inch diameter tubes can accommodate a surprisingly large volumetric flowrate. If the customer’s specifications allow, plastic vessels can also be substituted for traditional metal tanks in modular units (Figure 8).

▲Figure 8. Using plastic vessels and tubing, as shown in this lithium extraction pilot plant, reduces weight and manufacturing costs.
An important consideration during the modular unit’s fabrication is the amount of structural steel used to build it. Steel is produced by one of two production routes: basic oxygen steelmaking (BOS) is the primary route, and electric arc furnace (EAF) steelmaking is the secondary method. While the BOS process includes the reduction of iron ore and incorporates 10% to 15% scrap steel, EAF utilizes 100% scrap steel, making it the more sustainable option.
Of the estimated 1.87 billion tons of steel produced globally in 2019, approximately one-third comes from scrap metal, with the proportion increasing every year as more steel is recycled. This increase in steel recycling reduces the amount of iron ore that needs to be mined and processed. In fact, with steel being 100% recyclable and recycled at a very high rate (>95%), it is a good example of closed-loop recycling.
The structural steel used in modular plants is highly amenable to recycling once the plant reaches its end of life, given that the structures are almost universally self-supporting and can, therefore, be easily salvaged. Economics dictates that steel skid structures are either repurposed at the end of life or recycled, but they are never simply disposed of in a landfill or waste facility.
As mentioned previously, in modular plant design, the overall steel design and skid layout are highly optimized. This generally results in less steel used to accomplish the same amount of work, with a smaller overall footprint, than an equivalent stick-built plant. And, in certain applications, aluminum can be substituted for steel in smaller-framed units (Figure 9) to cut down on the weight and manufacturing labor.

▲Figure 9. Using an aluminum frame instead of a steel or stainless steel frame for a modular unit can reduce manufacturing costs and weight while maintaining a high degree of corrosion resistance and recyclability.
Finally, when it’s time to ship the completed modules, consider the sustainability and cost of available packaging options. Heavy-duty reusable tarps can be used for North American road shipments, while shrink wrapping should be reserved for overseas ocean or air travel. This minimizes the amount of waste plastic generated in the shipping of process plant modules within the U.S., Canada, and Mexico.
Closing thoughts
Several benefits should be kept in mind when considering modular fabrication over the traditional stick-built approach for delivering process plant projects. Now, decision-makers can add sustainability to the list of advantages.
The design and fabrication of modular process plants will continue to evolve as companies harness the power of digital technologies. This, together with advances in the materials and techniques used in the manufacturing of process plants, will see plants delivered in an increasingly sustainable way compared to how they were delivered in the past.
Literature Cited
- Anastas, P. T., and J. B. Zimmerman, “Design Through the 12 Principles of Green Engineering,” Environmental Science & Technology, 37 (5), pp. 94A–101A (Mar. 1, 2003).
- Edwards, D., “Sustainability in Modular Process Plants,” presented at the 2023 AIChE Process Development Symposium, Vancouver, B.C. (June 14, 2023).
Acknowledgments
The authors would like to thank their colleagues at Zeton — Ed De Rubeis, Nigel Semegen, Matt Soucie, Herman Bottenberg, and Leisl Dukhedin-Lalla — as well as Chris Biondolilo, Bob Perry, Rich Mitchell, and Pat Noonan of Merrick & Company for their input during the writing of this paper.
Copyright Permissions
Would you like to reuse content from CEP Magazine? It’s easy to request permission to reuse content. Simply click here to connect instantly to licensing services, where you can choose from a list of options regarding how you would like to reuse the desired content and complete the transaction.