In the metal product value chain, from mined ores to finished products, the most energy-intensive step is the oxide-to-metal conversion. Metal producers generate large amounts of greenhouse gases and other pollutants. In the U.S. alone, these industries produce more than 100 million m.t. of CO2e. Electrolysis is one approach to decarbonize the metals industry by substituting clean electrical energy sources for fossil fuel sources. However, the electrolytic reduction of metal oxides — which requires carbon anodes to electrolyze oxides dissolved in halides — emits CO2 and perfluorocarbons that harm the environment.
A new electrolytic process that reduces costs, energy use, and emissions has been developed at Boston Univ. by Dr. Uday Pal with support from the U.S. National Science Foundation (NSF). The process uses an oxygen-ion-conducting solid oxide membrane (SOM) as a selective electrolyte between the molten salt and the anode for the production of metals and alloys. Metals and/or their alloys form at the cathode and pure oxygen gas forms at the anode through direct electrolysis of their respective oxides. The process brings many advantages: simplified design, decreased use of energy and consumables, higher efficiency, zero emissions, and higher purity of metal and oxygen produced.
The SOM-based anode’s selectivity for oxygen separation is the key benefit of this process. For instance, when applied to solar-grade silicon production, it would eliminate direct emissions and reduce manufacturing cost and energy use by 80–90%. The membrane-based anode is typically made of stabilized zirconia. It has an oxygen-producing electrode on one side and a cathode to collect the reduced metal on the other side in a supporting ionic molten salt electrolyte bath (typically an alkali fluoride). The metal oxide is electrolyzed inside the salt medium by applying an electric potential between the cathode and the anode. The oxygen produced at the anode is pure due to the membrane’s selectivity, and the membrane completely isolates the oxygen from the salt bath and the metal at the cathode, making the metal and the reactor parts insusceptible to oxidation. In addition, the applied potential does not oxidize the halide ions or any multivalent cations in the salt.
The SOM process has been used to reduce several metal oxides to their respective metals or alloys and intermetallics, including light structural metals (aluminum and magnesium), silicon, rare earths, and corrosion-resistant metals (titanium and tantalum). Previously, Pal partnered with SunEdison to investigate SOM process scale-up for solar-grade silicon production. Fundamental studies on the structure-property relationship of molten salts and modeling of the SOM process have helped Pal to extend his collaboration with Germany-based Airbus Defence and Space, TU Bergakademie Freiberg, and the Fraunhofer Institute for Manufacturing Technology and Advanced Materials (Dresden). In this collaboration, SOM-based electrolysis of lunar regolith (i.e., lunar soil) is used as part of the in-situ resource utilization program on the Moon. Oxygen and metals are key resources for the build-up of a lunar infrastructure and need to be produced from local resources such as lunar regolith. An adaptation of the SOM process, called Regolith to Oxygen and Metals Conversion (ROXY), is ideally suited for this application (Figure 1). ROXY can provide reduced regolith as a high-quality raw material to manufacture a wide range of “Made on the Moon” products.
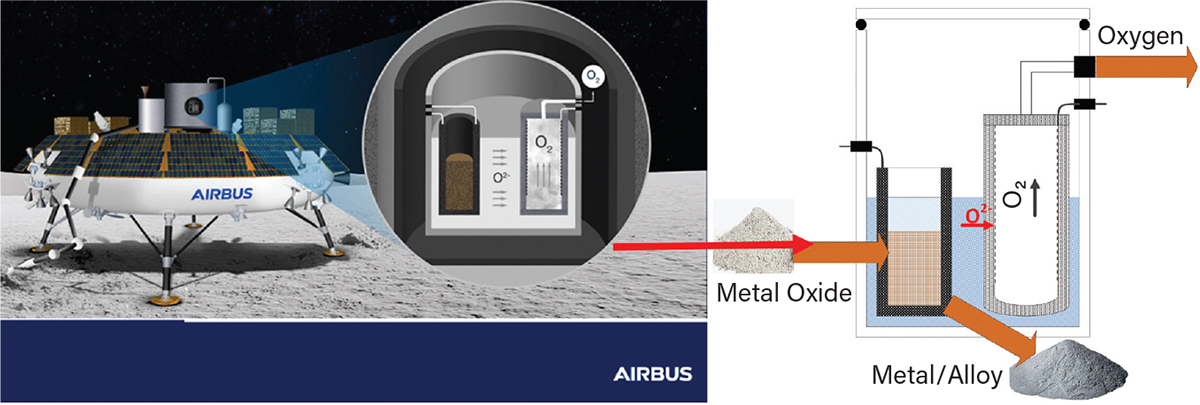
▲Figure 1. The Regolith to Oxygen and Metals Conversion (ROXY) process uses membrane-based electrolysis to convert lunar regolith into high-quality raw materials.
According to Achim Seidel, project manager at Airbus Defence and Space, “Future exploration missions to the Moon and beyond will be dependent on the use of lunar regolith to produce metals/alloys and oxygen. Among the many methods that have been studied, SOM-based molten salt electrolysis appears to be most promising since it meets all of the viability criteria.” A lunar demonstration mission is being prepared to address a wide range of scientific objectives related to regolith handling and diagnostics, the ROXY process, and post-processing steps. The mission will help propel the development of future larger-scale lunar ROXY systems.
This technology was supported through programs in the NSF Engineering Directorate.
This article was prepared by the U.S. National Science Foundation in partnership with CEP.
Copyright Permissions
Would you like to reuse content from CEP Magazine? It’s easy to request permission to reuse content. Simply click here to connect instantly to licensing services, where you can choose from a list of options regarding how you would like to reuse the desired content and complete the transaction.