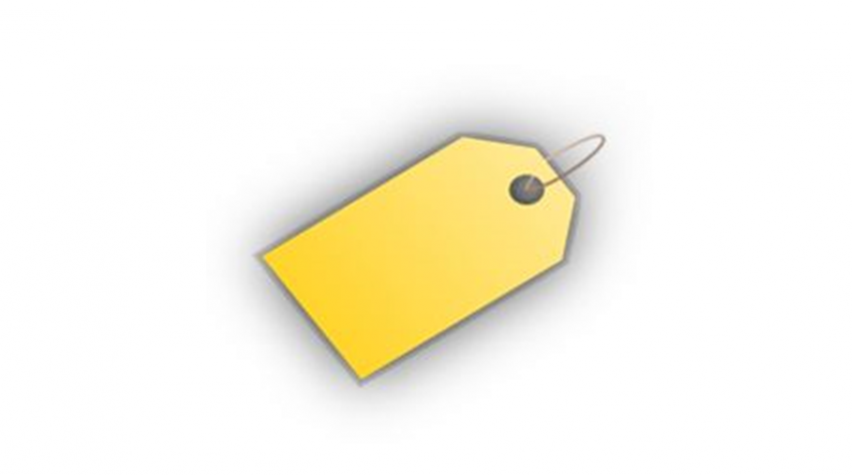
With a Bit of Smoke, a Few Mirrors and a Degree in Hieroglyphics, Anyone Can Learn to Read a P&ID.
Part 4 - Codes, Tags and Labels
So you are back for more in Part 4? After all we went through in Part 3, those still standing probably deserve a medal or something. That said, unlike Part 3 where we really covered a lot of detailed "nuts-and-bolts", this part will be a comparative piece of cake. Kind of like the last day of school where you know you still need to go and it might even be kind of fun, but you don't have to do any real work and the stuff you do take home will be memories not homework. That's the frame of mind you need to have for Part 4, ok? But before you take this as a cue to start shooting spitballs at your host, sit up straight because this part is vital to your understanding and development of clean, clear, odor-free P&IDs. Since this series is kind of long (hey, who snorted!?), let's get the requisite recap out of the way for those who missed the previous parts and need to circle back:
- Part 1 talked about why the interpretation of P&IDs is important to everyone involved in the planning, design, and construction through operation of a process plant.
- Part 2 described the various functions P&IDs serve and highlighted the kinds of information they convey, along with the support documents that are commonly associated with them. We also talked about some of their weaknesses.
- Part 3 covered the nitty-gritty aspects of instrumentation and control symbology. Along with that, we dissected tag abbreviations and how loop numbers uniquely identify devices. Since we were on a roll, we closed out this part with all the ancillary I/O symbols, line types, piping connections and other various sundry items peripheral to the main theme.
Up till now, we have spent a great deal of our time focusing on the first lead sheet, D001 - Instrumentation and Valves, provided along with other drawings in the supporting file download to this series. In this Part 4, we will turn our attention to the remaining lead sheet, D002 - Codes, Tags, and Labels. As I have mentioned previously, D002 is an example lead sheet typical of the ones I have
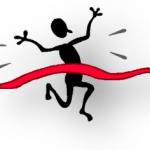
used in the past. It may look different from the ones your company uses and that's OK. It's not as important how a company prefers to do labeling on a P&ID, only that they do it clearly, consistently and based on a robust system that is amenable to future change and additions. An extensible tagging system if you will. That's a concept that may be a bit unfamiliar to some so I will discuss that as a sort of prerequisite. Hang in there, I see the finish line...just around the corner!
P&IDs Are Really Databases, Wait..what?
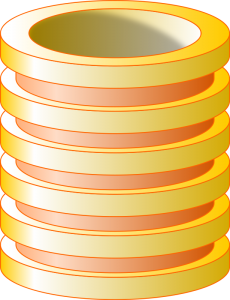
While P&IDs are representations of the process to the casual observer, their underlying structure more closely resembles a relational database. In fact, for those of you familiar with today's common computer aided drafting packages, you may realize that a CAD drawing is really a database of objects assembled in a structured manner. Even if you reuse the same object over and over in a drawing, the CAD system keeps track of it with a unique identifier. This is very similar to a process plant in that, well for starters, we apply tags to keep track of equipment, piping, valves, devices, etc.--things that we reuse over and over again in any given process design. So I am here to tell you folks, when you design a process and develop the P&IDs in CAD, you are really assembling a database along the way. This isn't lunacy with half a bowtie. I'm serious and I would urge you to get familiar with relational database design, if only from an academic standpoint. Like object-oriented programming, these abstract concepts are extremely valuable towards implementation in our line of work. Some examples? Ok, behold my exhibits--like a database, a process plant illustrated using CAD on a set of P&IDs:
- Contains collections of similar objects with unique tags so that even identical objects (valves, pumps, instruments, etc.) can be uniquely identified.
- Is assembled in a structured manner that lends itself to additions, deletions, changes, etc. with a granularity as coarse as whole unit areas, down to a single valve on a pipe anywhere in the plant.
- Contains lots of metadata in the tagging systems that can inherently provide (or link to) much more detail such as specifications, materials of construction, data sheets, etc.
There's more than just the above but I will rest my case. I hope you agree that while the tags and labels themselves are self-evident, the real power is in the underlying tagging system used. And so you're still thinking, "why must a tagging system be so robust and extensible? I mean, come on Bob, aren't you making a mountain out of mole hill?" Well, glad you asked; the answer is quite simply because most plants change over their useful life. Change comes from a lot of different angles:
- Operational Tweaks--improvements often come from the operations folks. In my experience, some of the best improvements to a plant don't come from the egghead engineers sitting in their cubicles, but from the folks in the plant dealing with the machine each and every day. It is in their interest to make it work better, safer and cheaper.
- Capacity/Production Changes--often, a particular unit operation needs to be expanded to meet new production requirements or changes in feedstock or product requirements that shift the process design needs. I've seen instances where complete new trains have to be added to a system.
- PSM Audit Review--Process Safety Management requires that process documentation be kept up to date and routine plant audits and Process Hazard Review may reveal changes that should be implemented to a plant that is already in operation. The P&IDs are the reference upon which such reviews are based and must always be in a current "As-Built" state.
The key take-away from the list above is that the P&IDs serve initially as the process definition upon which the plant is designed. But then they serve operations long after the plant is built. This is why earlier in this series I espoused the need for engineers to be routinely, actively engaged in ongoing operations. Not only will you learn a lot about the plant that you yourself may have helped build, the feedback you receive will be invaluable to maintaining a safe operation. Plus, you can implement the lessons learned on future projects. Now that I've driven home the importance of a structured tagging system, let's turn attention to the meat of this Part 4--the actual tagging of equipment and devices.
Equipment Tags
Lots of companies use what appears initially to be an intuitive, simple system to tag equipment. It later reveals itself not to be very intuitive or robust. Let's pause for fictitious example (that bears no resemblance to my past, really). GitRDun Process, Inc. has decided to build a new plant to produce Trimethylkabif, a precursor to a drug that yields quick weight loss, improved memory and muscle tone while eliminating irritable bowl, gastric reflux and attention deficit. The process folks start out tagging equipment as follows:
- Pumps are simply tagged P-1, P-2, P-3 (makes sense right?)
- Agitators are tagged AG-1, AG-2, AG-3, etc. Dude - this is so simple!
- And of course tanks and vessels are tagged TK-1, TK-2, TK-3 (or V-1, V-2, V-3). Could do this in my sleep...
And so on...Life is good. Later on, though less common equipment starts getting added, and this starts to stress the "intuitive" nature of the system. For example, a centrifuge is initially tagged C-1 but now they need to add a conveyor but C is taken so they decide to call the conveyor CO-1. Now they think, well, we will just revise the centrifuge tag to CE-1. Crisis avoided...But wait, later they need to add a chemical feed package and want to tag that CF-1. OK, that's cool but then a bunch of cross flow filter modules is added they decide to "steal" the CF label for those and change the chemical feed to CE, no wait...can't do that, CE is taken by the centrifuge. So they bite the proverbial bullet and call the chemical feed skid CS-1 where S is "intuitive" for supply. Right? Try again quiz kid. Nobody is going to see that as intuitive. And then one day, it hits GitRDun's process engineers that their initially conceived so-called intuitive tagging system is a heap of broken confusion and nobody knows their CE's from their CO's. Cue the Jackson 5 song A B C, simple as 1 2 3!
A Better Tag Numbering System
To avert the problems inherent in the above example, many process industries utilize a numeric-only system for tagging equipment. This helps simplify the logical categorization of equipment during the process design phase. Moreover, a structured tag system is more intuitive for the development of design documentation, operating procedures and training, and general documentation upkeep/maintenance. With that in mind (and considering the points presented earlier in this Part), the following method is but one example of how to tag process equipment using an extensible system.
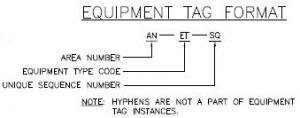
Area Number, AN Most sizable process plants are comprised of multiple areas. An area is a physical, geographical, or logical grouping determined by the site. It may contain process cells, units, equipment modules, and control modules (more details can be found at isa.org). To facilitate a hierarchical organization of equipment, equipment tags should then incorporate area designation.
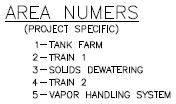
A small or simple project may have only one area. Conversely, larger more complex projects may have multiple areas. The assignment of areas is at the discretion of the process engineer and can be subjective. The only general rule that I like to employ is that common equipment that serves multiple areas, e.g., utility and infrastructure system be placed into a "Common Resources" area rather than be made a part of any other process area. Once areas have been designated for a particular project type, engineers should strive to maintain common area designations on future, similar projects. For example, the areas shown in the figure above may be defined on the lead sheet for a fictitious project.
Equipment Types, ET
Equipment can be identified based on its type using a numeric system such as the simple one shown below. In cases where equipment has multiple functions, user discretion is advised in selecting the most suitable type code.
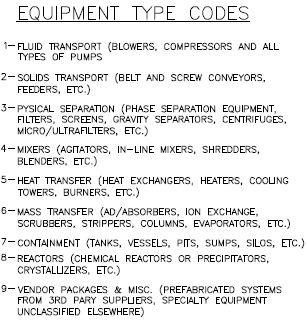
Sequence Number, SQ
This is the consecutive numbering of like equipment in a particular area. The sequence begins with 01. All equipment is to a have its own sequence number. The use of alphabetic or other tag suffixes is to be avoided.
Example Equipment Tags
Using the system outlined above, a four-digit system emerges that may not be instantly recognizable in terms of what the specific equipment is (or where), but it will eventually become very familiar to those who are intimate with the plant. A few examples using the area numbers defined above are provided below:
- 1101 - The first pump in the tank farm area.
- 1701 - The first tank in the tank farm area.
- 1405 - The fifth mixer in the tank farm area.
- 2901 - A vendor package in the Train 1 area.
The equipment tag number should be prominently displayed near the symbol used for the equipment. For example, the tag number for a centrifuge might appear as follows on a P&ID.
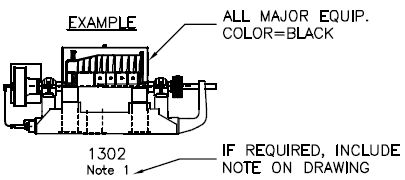
Lastly, all major equipment should be named and provided general specifications in a label placed along the drawing border. A couple examples for a pump and tank follow.
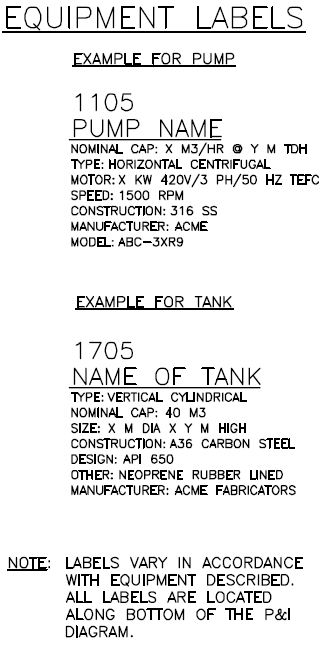
It is up to your company to decide on the final formatting, location (some companies like to put certain equipment labels near the top of the border), and which particular specifications should be included along with each major equipment label. The system presented here is fairly simple and broadly applicable. Irrespective of these details, I highly recommend that every piece of major equipment receive a label with a similar level of detail.
Instrument Loop Numbers
A benefit of using four digit equipment numbering system such as the one presented above is that the tags lend themselves toward application in defining associated instrument loops. This makes grouping equipment and associated instrumentation devices more logical. Think back to our friends at GitRDun Process, Inc. Their tagging system consisted of tags like P-1, AG-1, CE-2, etc. These tags are not amenable for use in defining instrument loops. However, a four digit system does neatly tuck into instrument bubbles and when you think about it, most instruments and devices serve or are primarily associated with a piece of equipment. And even when that is not the case, they can readily borrow from the equipment type code "9" in cases where, for instance, a pressure gauge on an air header serving the entire area must be defined. Considering the above points, the following instrument and device tagging system is but one effective way to tag instruments and devices:
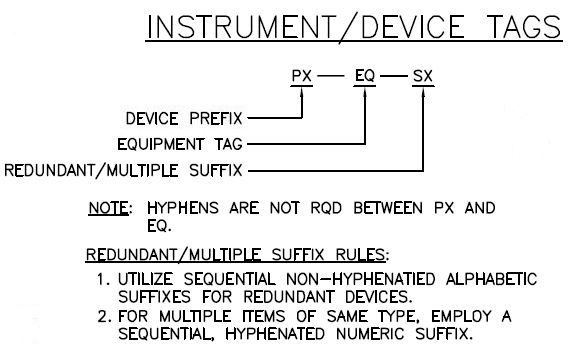
Where;
- PX - device type prefix (as per ISA 5.1)
- EQ - the associated equipment tag (as defined above)
- SX - duplicate or redundant device suffix (see details below)
Duplicate Suffix, SX Rules
A suffix is provided to accommodate instances were many devices of the same type are associated with a given piece of equipment. For example, a vessel may have many lines connected to it, each having its own actuated valve. To resolve these instances so that each device has its own unique loop number, there are two suffix tag methods that can be employed,
- If a piece of equipment has redundant devices associated with it, an alphabetic suffix may be appended to the loop number, e.g., FV1101A, FV1101B, FV1101C, etc. (Note: Redundant means serving the same purpose as another device in a backup fashion.)
- If a piece of equipment has multiple items of the same type, each of which with different functions (not redundant) then a numeric system should be employed, e.g., FV1101-1, FV1101-2, etc.
Example Loop Tags
Based on the above discussion, some example loop tags are provided below. If needed, the reader can visit a more though discussion in Part 3 regarding instrument abbreviations. (Note: In the examples provided, I use the example Area Numbers presented as examples above.)
- PI1101 - A pressure indicator on the discharge of the first pump in the tank farm area.
- LT1701 - A level transmitter on the first tank in the tank farm area.
- IT1405 - A current transmitter (for the motor) on the fifth agitator in the tank farm area.
- AE1701A - One of at least two redundant analyzers on the first tank in the tank farm. Hence, one would expect to see AE1701B, AE1701C... as indicated.
- XV1701-1 - An actuated valve on the first tank in the tank farm area. The suffix -1 implies there are other valves associated with tank 1701 but in an alternate service (i.e., not redundant). For example, XV1701-1 may be on the inlet to the tank, while XV1701-2 may be on the outlet.
Line Numbers
Similar to equipment and instrumentation, every pipe on a P&ID requires a unique tag number so that it can be uniquely identified during design, or referenced in operating procedures. Since most lines are also affiliated with a major piece of equipment to which they connect, I like to employ a numbering system similar to that used for instrument loops whereby the equipment tag is integrated into the line tag in the following manner (Note: D002 provides an alternate method that employs drawing number instead of equipment number but I generally prefer the method given below.)
X"--SVC--ET:SQ--LS
Where;
- X" - the nominal size of the pipe
- SVC - the service code for the material that normally flows in the line (see examples below for list)
- ET:SVC - a unique line tag that includes two parts, the equipment tag from which the line originates followed by a unique sequential number
- LS -line specification for the pipe, including class and material type, valves etc.
Service Codes, SVC
Service codes are abbreviations for the fluid the line primarily handles.
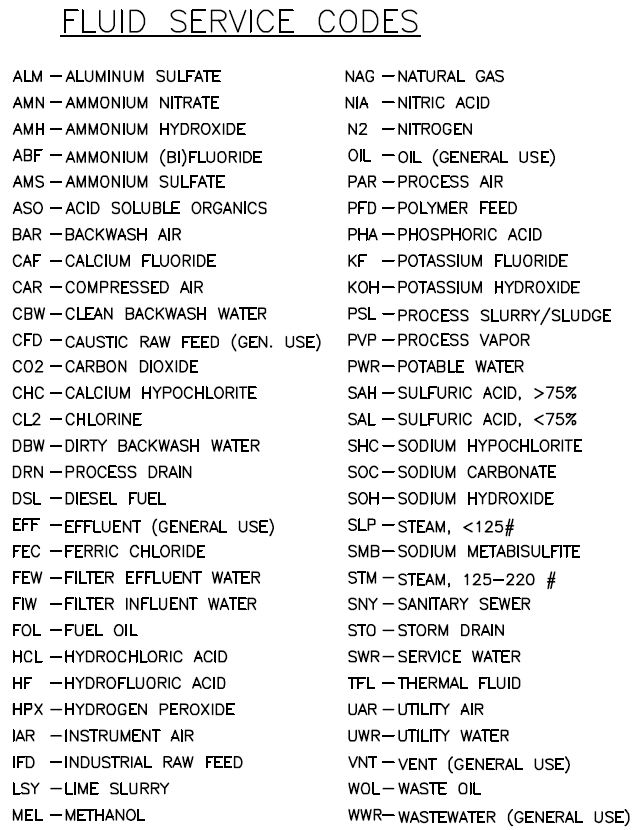
Since some lines can serve many different process fluids, the fluid used to specify the materials for the line should go here. The list should be available on a lead sheet in a manner similar to that provided in the example above.
Line Specifications, LS
Line specifications cover all the details related to the piping system used to handle the fluid for the line. This should include all details regarding material of construction, valves and trim, gaskets, fittings, T/P limits, and much more. This is beyond the scope of this series but is such a critical component of plant design that I might expand on this in a future post.
Hand Valves
Hand valves require a consistent and clear tagging system for reference in operating procedures. There are a number of techniques that can be used, but one that I generally prefer is as follows.
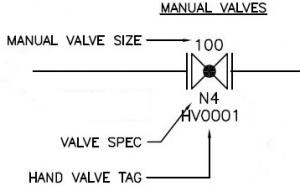
In the example provided at left, one can discern valve size, spec and tag number. This might be more information than you want to include on some P&IDs. In cases where you just want to show the valve tag and allow the spec and size to be derived implicitly from the line tag, the following method is one option:
"V" - D# - SQ
Where;
- HV or V - A literal and required part of all hand valve tags
- D# - last two digits of P&ID drawing number
- SQ - Sequence Number (01 to 99)
- V0001 - The first hand valve on P&ID D100
- V1205 - The fifth hand valve on P&ID D102
Example Hand Valve Tags
- V0001 - The first hand valve on P&ID D100
- V1205 - The fifth hand valve on P&ID D102
Wrap-Up
Further to the content in this part, D002 includes a few more examples of common tags and codes applied in P&IDs, such as insulation, interconnecting arrows, etc. These are important parts but are pretty self-evident. Aside from that, most companies have very specific ways and means on these items so I won't cover them in depth here. Well, I started this out by saying it was going to be fun and simple and I hope you leave this series feeling like I made some solid points that will be of value to you going forward. In a follow-up to this series, I will put together a complementary video where I take a few typical P&IDs (like the ones I've attached here) and discuss all of these aspects in what I hope to be a much more engaging manner. You will then be able to get a much better feel for seeing and hearing this information. Now venture forth with your new knowledge and apply it for good. Stay safe and have fun.
Comments
Good job Robert, I liked the simplicity in your presentation
This is a great post for new engineers. I didn't learn these details about P&IDs in school so it's nice to have it explained somewhere in a straight forward manner!
Thanks for the kind feedback folks. I just finished up a few companion videos that are in the queue for posting here. I hope they provide even more insight. I was considering expanding this to a more complete resource that covers details as well. Just need to find time!
I'm graduating from college this semester and I didn't know anything about P&IDs - this is very comprehensive and informative - thanks! - I wish they teach this stuff in school...
Burrito¡ Estaba buscando informacion sobre el tema y es muy limitada la que encontre, con este nuevo material solo me resta traducirlo, gran aporte amigo Gracias¡
Martin, Thanks for your kind feedback. I used translate.google.com to translate your response. Perhaps it can be used for your needs here? Best, Bob
Very well written, thanks for that. Did you get round to doing Line Specifications, LS? I've ben looking for more information on this but not easy to find. Thanks again
Hi Bob, Great work on the P&ID presentation. I've been working in oil and gas for about 2.5 yrs now. Some of the stuff came in real handy, especially in pt 3 with instrumentation and controls. Instrumentation and controls stuff on P&IDs confused me before I read your presentation. Can't wait for the stuff you're planning to present on piping materials / piping specifications and functional control description. Keep up this great service. Thanks,
Absolutely wonderful series..enjoyed it thoroughly..you should get that medal.
Robert, thanks alot for the videos on youtube, i just begining to lear instrumentation, didnt know anything about it but this is making it alot easier, thanks again, and if you have more info on the basics i will appreciate it , thanks
Dear Robert, I'm from Brazil and would like to thank you for this post. As I started an internship right now it's being very useful. However, I'm facing problems to access part3, the links aren't working. If you could fix that, would be very grateful!! Congratulations on this work! Cheers
Hi Robert, Should the last to digits of the drawing numbers of the valves be V0001 and V0205 •V0001 – The first hand valve on P&ID D100 •V1205 – The fifth hand valve on P&ID D102 Thanks
Yes, you are correct. I can tell you were paying close attention. This is the kind of attention to detail that really pays off in the long run. Thanks for pointing it out.
Hi Sir Robert, I really need your help, Can you teach me on how to create a material codes for Bolt & Nuts, Construction Materials, Cables and wires. I am certain that you will assist me on this. Regards
Fasteners are a key component of a comprehensive piping and material specification. This is based on the service (material, P/Temperature) and structural considerations. Additionally, one may encounter "classes" of service where, for example, a particular line may have a specification up to a certain P/T but another class for a more severe condition. On the point of cables and wires, this is altogether outside the realm of process engineering scope and is not an area of expertise for me. I can say that, similar to materials, there are a host of considerations, NEMA, NFPA, combined with site-specific issues (corrosive area, etc), that makes this as challenging an endeavor as defining line specifications. I hope I left you with a better understanding of the problem you are attempting to solve!
Dear Mr. Robert, This is a very useful article and superbly written, lucid, concise and explanatory. I was worried about the valve numbering , at the end. I thought maybe I had misunderstood the concept and went through it several times until I saw that someone had pointed out the inadvertent error. Please keep up the good work. Cheers Pandurang
Outstanding presentation - one of the most straightforward and useful I have seen. Thank you for sharing this work.
Excellent Robert, many thanks
First of all I want to thank you Robert the great effort in the development of these tutorials, great job. The aim of this comment is to know if exist and specific Identification Letter for Temperature & Humidity devices. Usually I use T for temperature sensors and M for Humidity or Moisture sensors, but ¿I need to use a User's Choice letter for Temperature and Humidity Sensors? Thanking in advance you attention and collaboration in this subject, receive greetings from Barcelona.
Xavier, It sounds like you have a humidity analyzer (AE) with a built-in temperature element (TE). This is common with pH meters as wel as temperature compensation is desired to improve the reading due to the affect of temperature. If the humidity and temperature sensors are physically integrated into a common sensor, then using two circle bubbl s that are physically touching each other on the drawing (no connection line) would be appropriate. If they are separate sensors routing to a common transmitter then you can show them as discrete bubbles with electrical signal to the transmitter. Shoot me an email to discuss or I can send you some options and how they compare. Robert.graham.cook at gmail.com.
Great article on P&ID. Now, I would like to ask about how to start tagging my instruments on the P&ID of say a pump that has the following instruments: At suction: PSL, PSLL, PI, At discharge: PSHH, FSLL, PI, On the motor and pumps: VSHH (DE),VSHH (NDE) LSL, TSHH, Who comes first in the sequential numbering for the instruments? Assume we want to start at 1100 Please help! I am depressed :(
Do we need a separate line number if there is a pipe spec break in the line?