Malonates, including malonic acid and its dimethyl and diethyl esters, are specialty chemicals used in flavors and fragrances, pharmaceuticals, adhesives, and electronics manufacturing. Although malonates have a range of beneficial properties, their use is limited to high-value applications because the processes for manufacturing them are expensive and involve toxic chemicals. Industrial routes to manufacture malonates start with two environmentally hazardous raw materials (chloroacetic acid and hydrogen cyanide), produce substantial amounts of acid and salt waste, and suffer from low product yield.
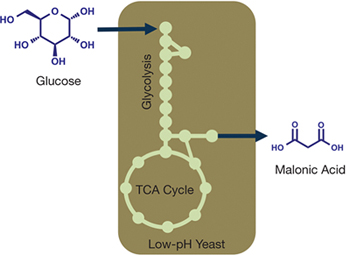
▲ Lygos has developed a fermentation-based process that converts glucose into malonic acid using a low-pH, organic-acid-tolerant yeast. The biosynthetic pathway, which diverts carbon from the organism’s tricarboxylic acid (TCA) cycle, is highly efficient and produces two moles of malonic acid per mole of glucose.
A lower-cost process based on renewable raw materials could spur the development of new applications and markets for malonates. For example, malonates could be condensed with adlehydes to make α,β-unsaturated carbonyl products. Methylene malonates, which are produced by condensing formaldehyde with malonates, would be useful for the production of new adhesives, coatings, composites, and inks. In addition, condensation of malonic acid with diamines or diols are new routes to polyamides and polyesters, respectively.
Lygos, Inc., a California-based biotechnology company, is developing a novel, low-cost fermentative route to malonic acid using engineered yeast. Lygos’ scientists have engineered Pichia kudriavzevii, an acid-tolerant yeast, to produce malonic acid from glucose. The biological pathway is highly efficient, with a stoichiometric theoretical yield of 2 moles of malonic acid per mole of glucose consumed. With a higher theoretical yield than industrial processes, the new route to malonic acid has lower raw material costs, and thus a competitive advantage over the synthetic, petrochemical-based route.
With funding from a Small Business Innovation Research (SBIR) grant from the National Science Foundation (NSF), Lygos has developed a genetic engineering toolkit for P. kudriavzevii.
“When producing an organic acid microbially, it is important to find an organism capable of growing at low pH and high product concentrations,” says Jeffrey Dietrich, Lygos’ Chief Technology Officer and co-founder. “The industrial workhorses of industrial biotechnology, Escherichia coli and Saccharomyces cerevisiae, are neutral-pH microbes poorly suited for producing malonic acid. We had to find a new microbe whose physiology was a good match with our envisioned industrial process.”
Lygos found that match in P. kudriavzevii, a strain of yeast that can grow well in the presence of high concentrations of organic acids. But the company faced the challenge of engineering the microbe, which does not naturally produce malonic acid. Effective tools and techniques commonly found in a metabolic engineer’s toolbox (e.g., plasmid expression vectors, well-characterized promoter libraries, gene-silencing techniques, and auxotrophic markers) were not available for this strain of yeast. So Lygos developed a high-throughput P. kudriavzevii engineering toolkit using malonic acid biosynthesis as the test case. Now, the same powerful engineering techniques used to genetically modify S. cerevisiae and other model strains can be applied to this more industrially relevant, low-pH yeast.
Lygos has developed the process to a point sufficient for commercial production of malonic acid that is cost-competitive with malonic acid made via traditional petrochemical-based processes. It has also developed a lab-scale purification technique to separate the malonic acid from the fermentation broth. The company is currently producing 1-kg batches of purified malonic acid for customer validation and testing.
Moving forward, Lygos plans to scale up the integrated manufacturing process, and has received a Small Business Voucher from the U.S. Dept. of Energy to run larger-scale pilot fermentations at the National Renewable Energy Laboratory (NREL) in Colorado. After that, the company plans to use various contract manufacturers to begin producing commercial quantities of malonic acid in late 2016.
This technology was funded through the NSF Small Business Innovation Research Program.
This article was prepared by National Science Foundation in partnership with CEP.
Copyright Permissions
Would you like to reuse content from CEP Magazine? It’s easy to request permission to reuse content. Simply click here to connect instantly to licensing services, where you can choose from a list of options regarding how you would like to reuse the desired content and complete the transaction.