The chemical industry is the backbone of India’s industrial and agricultural development. Achieving the industry’s ambitious growth targets will require a combination of policy intervention, company-level initiatives, industry-academic partnerships, wise investments, and greater international access.
The chemical industry’s role as the key enabler of economic growth is well-established worldwide. From the ubiquitous cellphone, to solar panels producing carbon-free energy, to LED lights providing efficient lighting — all are made possible by chemical industry products. In India, the chemical industry occupies a pivotal position in meeting basic needs and improving quality of life as well. Although India is severely deficient in conventional hydrocarbons, the country has a well-developed refining industry that provides several basic chemical industry feedstocks.
The chemical sector, which is knowledge- and capital-intensive, is the mainstay of industrial and agricultural development, and provides building blocks for downstream industries such as textiles, papers, paints, soaps, detergents, and pharmaceuticals, among others. The fertilizer and agrochemical industries ensure food security, and are thus vital to India’s developing and agrarian economy. Likewise, the synthetic fiber industry is crucial to providing affordable clothing, and the pharmaceutical industry gives the country’s vast population access to low-cost drugs.
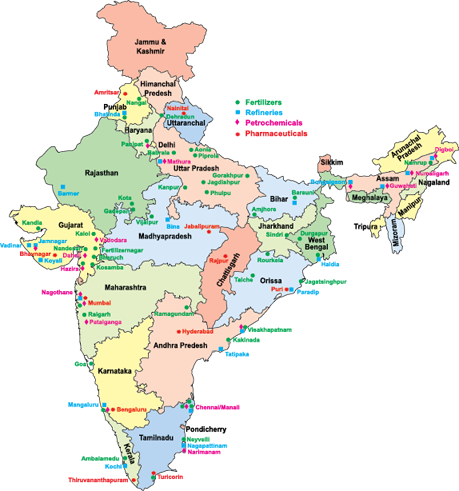
▲Figure 1. India is the seventh-largest country by area, with petrochemical, refining, fertilizer, and pharmaceutical plants located throughout its 29 states. Plants run by small and medium enterprises are mainly located in the states of Gujarat and Maharashtra.
One of the world’s fastest growing economies, India is a federation of 29 states and seven union territories (Figure 1). This article traces the development of India’s chemical industry, its importance to the Indian economy, its major sub-sectors and their growth potential, and the technology and policy measures needed to drive sustainable growth.
Historical development
The development of the chemical industry in India can be traced to the indigenous efforts of P. C. Ray, a professor of chemistry at Calcutta Univ. Ray established the pharmaceutical company Bengal Chemicals and Pharmaceutical Works in 1892; it was incorporated nine years later. This was followed by the founding of Alembic Chemical Works at Baroda (now Vadodara) in Gujarat, by B. D. Amin (1).
During World War II (1939–1945), foreign drug supplies decreased and several Indian pharmaceutical companies opened, including Unichem, Chemo Pharmaceuticals, Zandu Pharmaceutical Works, Chemical Industrial and Pharmaceutical Laboratories (CIPLA), and East India Pharmaceutical Works. The Indian government later established five public-sector companies. Two of them— Hindustan Antibiotics Ltd. (HAL) in 1954 and Indian Drugs and Pharmaceuticals Ltd. (IDPL) in 1961 — played particularly important roles.
During the first two decades after India’s independence from British rule in 1947, several industrial units were established to make basic chemicals, dyes and textile auxiliaries, and fertilizers (Table 1). By the 1960s, India had also developed a sizeable alcohol-based chemical industry that used ethanol as feedstock (2). A recommendation that “molasses-based alcohol be totally reserved for industrial use,” rather than used as an energy source (3), and stricter controls on sugarcane molasses as well as alcohol prices and allocations played a role in this development.
Table 1. These milestones in the early development of India’s chemical industry illustrate India’s drive to become self-reliant in chemical production. Source: (4). | ||
Year | Company Name and Location | Notes |
1901 | Assam Oil Co. (now Indian Oil Corp. Ltd.) Digboi, Assam | India’s first petroleum refinery with a capacity of 500,000 m.t./yr |
1919 | Dharamsi Morarji Chemical Co. Ambernath, Maharashtra | First producer of sulfuric acid (lead chamber process) and phosphate fertilizers in India |
1943 | High Explosive Factory Kirkee Maharashtra | Nitric acid from ammonium sulfate for manufacture of the explosive trinitrotoluene |
1944 | Tata Chemicals, Ltd. Mithapur, Gujarat | Second soda ash plant in India; now the second-largest producer in the world |
1947 | The Fertilizers and Chemicals Travancore (FACT) Kochi, Kerala | First ammonium sulfate plant in India; used wood as raw material for making ammonia |
1947 | Kochi, Kerala Atul Ltd. Atul, Gujarat | Incorporated by Kasturbhai Lalbhai to make India self-reliant in chemicals; set up joint ventures to make basic chemicals, dyes, agrochemicals, and polymers |
1951 | Sindri Fertilizers and Chemicals Ltd Dhanbad District, Jharkhand | Reparation from Great Britain for World War II Second in India to produce ammonium sulfate (1951); first fertilizer factory to have its own captive power plant (1951); first in India to make urea (1959) and ammonium nitrate-sulfate (1959); used gypsum (carted by train from distant Jodhpur area) and coal as raw materials |
Synthetics and Chemicals Ltd. (Bareilly, Uttar Pradesh) was one of several companies to begin using alcohol as feedstock for butadiene and styrene-butadiene latex production. Other units, located in sugar-producing states, manufactured acetic acid, acetone, butanol, ethyl acetate, ethylene, monoethylene glycol, and polyethylene at various times over the years. Removing alcohol price controls in the early 1990s, and its diversion as a gasoline additive after a 2015 policy shift, has made most alcohol-based chemical units unviable. Today, only a handful operate and produce few chemicals, including ethyl acetate and monoethylene glycol.
In the 1960s, Union Carbide set up the first ethylene cracker in Mumbai with alcohol as feedstock, later switching to naphtha from an adjacent oil-refinery pipeline. In 1964, National Organic Chemicals Industries Ltd. (NOCIL), today a leading Indian manufacturer and supplier of rubber chemicals, entered into technical collaboration agreements with Royal Dutch/Shell to build a naphtha cracker and downstream plants in Navi Mumbai.
The petrochemical industry continued to grow in the 1970s, with Indian Petrochemicals Corp. Ltd. (IPCL) building its first integrated naphtha-based cracker in Vadodara. Again, the decision was aided by experts’ recommendations that naphtha — which was already in surplus in the country — be used preferentially for petrochemical production and made available free of taxes and duties to improve the petrochemical industry’s competitiveness. IPCL was also the first large Indian company to start R&D before production began. The company’s R&D director was a full-time member of the Board of Directors — a trend subsequently followed in other public-sector companies, including Engineers India Ltd. (EIL) and Indian Oil Corporation Ltd. (IOCL).
In the 1980s and 1990s, the petrochemical industry expanded rapidly with the development of integrated naphtha and gas crackers, along with related downstream plants for polymers, synthetic fibers, aromatics, and other chemicals. After an early-1980s Ministry of Petroleum and Natural Gas policy decision to separate ethane from natural gas, IPCL established gas-based crackers at Nagothane (Maharashtra) and Gandhar (Gujarat); GAIL India Ltd. developed a unit at Pata (Uttar Pradesh). A 2016 policy decision to separate ethane from imported liquefied natural gas (LNG) led ONGC Petro Additions Ltd. (OPaL) to use LNG for ethylene production at Dahej (Gujarat).
Petrochemical demand, which was suppressed by inadequate supply and high import tariffs, rapidly expanded when private-sector companies entered the industry. Of particular importance were the Reliance Industries Ltd. facilities at Patalganga (Maharashtra), Hazira (Gujarat), and Jamnagar (Gujarat). Integrated petroleum and petrochemical refining offered enhanced competitiveness, as did the significantly larger scale of operations. This is exemplified in the polyester business, where Reliance Industries integrated its value chain from crude oil, refinery, and aromatics, to p-xylene, purified terephthalic acid, and polyethylene terephthalate resin. They used the new materials to make polyester fiber, filament, and bottles.
The Council of Scientific and Industrial Research (CSIR) was established in 1942 with the mission to provide scientific and industrial research and development to maximize economic, environmental, and societal benefits for the people of India. Three laboratories were created under CSIR to serve the chemical sciences: Central Drug Research Institute (CDRI), National Chemical Laboratory (NCL), and Indian Institute of Chemical Technology (IICT), previously known as Regional Research Laboratory (RRL).
The Indian Chemical Manufacturers Association, now called Indian Chemical Council (ICC), was founded in 1938 by P. C. Ray, Rajmitra B. D. Amin, and a group of industrialists who strived to promote the nascent chemical industry’s interests. Over the years, ICC became the industry’s representative body and celebrated its achievements, including those in indigenous technology development, through coveted and prestigious annual awards.
Importance to the Indian economy
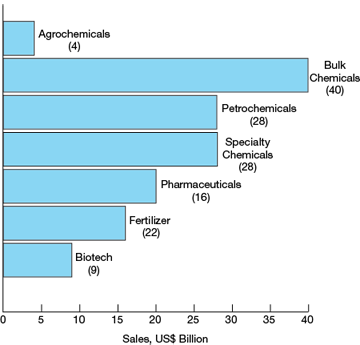
▲Figure 2. Bulk and petrochemicals accounted for almost half of India’s chemical product sales of US$147 billion from 2014–2015.
From 2014 to 2015, India’s chemical industry was valued at US$137 billion, with overall chemical and chemical product sales of US$147 billion. Bulk chemicals, petrochemicals, and specialty chemicals accounted for 65% of total sales (Figure 2) (4). The fertilizer and agrochemical industries represent important nationwide industry segments, which is not surprising given the agrarian nature of India’s economy.
Despite its apparently large size and significant contribution to gross domestic product (GDP), the Indian chemical industry accounts for 3% of the worldwide chemical market, valued at US$4.3 trillion. Excluding pharmaceutical products, it ranks 14th in chemical exports and eighth in imports.
International trade
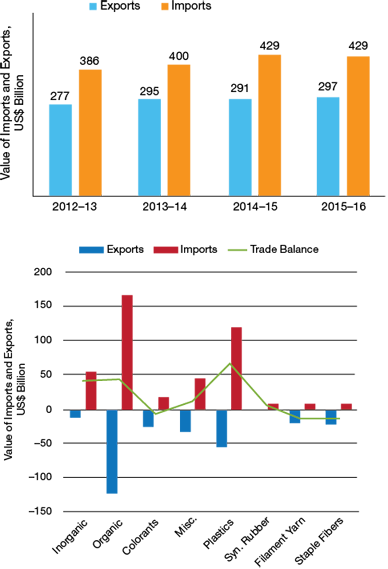
▲Figure 3. In 2015–2016, India remained a net importer of chemicals and related products (top), and the value of exports of some products, such as colorants, surpassed the value of imports (bottom).
India’s chemical industry accounts for about 10% of the country’s manufactured exports. This has remained relatively constant over the last four years. The industry remains a net importer of chemicals, although in certain product categories, such as drugs, agrochemicals, and dyes and pigments, the trade surplus is positive (Figure 3). The share of chemical imports, relative to total imports, has increased from 7.9% in 2012–2013 to 10.5% in 2015–2016.
Petrochemicals

▲Figure 4. India’s per capita petrochemical consumption is lower than global averages and will likely grow as the country prospers.
Petrochemicals play a vital role in almost all key economic sectors, including agriculture, infrastructure, healthcare, textiles, and consumer durables. India’s low per capita consumption of most petrochemicals, compared to global averages, points to the growth possibilities that will arise as the country becomes more prosperous (Figure 4). India’s demographics also favor growth. More than 70% of Indians are under the age of 40 and the majority are in the working and consumer classes. This cohort will continue to drive consumption of goods and services for a very long time.
Sectors driving demand for petrochemicals include packaging, construction, automobiles, and agriculture. Sustained government investments in infrastructure upgrades, including low-cost housing, will provide strong stimulus for polymer demand. In the short term, low oil prices are expected to help the petrochemical industry, both directly through access to low-cost feedstock, and indirectly, by providing consumers with additional disposable income.
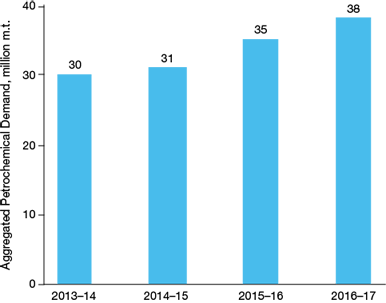
▲Figure 5. Sectors driving the increase in petrochemical demand include packaging, construction, automobiles, and agriculture. Aggregated petrochemical demand is expected to reach 41 MMmt in 2017–18 (Source: CPMA).
According to the Chemical and Petrochemicals Manufacturers Association (CPMA), aggregated demand for petrochemicals increased 5% in 2014–2015 to 32 million metric tons (MMmt) and to 35 MMmt in 2015–2016 (11% year-on-year growth). Demand is estimated to have reached 38 MMmt in 2016–2017 and to 41 MMmt in 2017–2018 (Figure 5) (5).
The Indian polymer market is dominated by polyethylene (PE) and polypropylene (PP), which represented 73% of all commodity resins consumed in 2015–2016. After experiencing subdued growth in 2013–2014, polymer growth rose to 7% in 2014–2015, and about 14% in 2015–2016. The market is expected to grow an estimated 11% in 2016–2017.
India’s petrochemical capacity is currently where South Korea’s and China’s stood about 15 years ago. Even if India’s consumption rises at a pace of about 1.2 to 1.5 times GDP, as expected, its petrochemical industry will still only be slightly larger than South Korea’s and about a quarter of China’s in 2025 (6).
On the demand side, there are also strong grounds for supporting petrochemical investments. India’s ethylene deficit could range from 4 MMmt/yr to 8 MMmt/yr by 2025, and propylene’s could be anywhere from 1 MMmt/yr to 3 MMmt/yr. Butadiene, an important olefin for copolymers and synthetic rubbers, is also expected to exceed supply until 2025. While benzene is expected to remain in surplus, this should not be a cause for concern. Several value chains in which there is now no domestic production can be built, leading to significant offtake of the aromatic.
Even considering speculative capacity, an additional 4 MMmt/yr of PE and about 3 MMmt/yr of PP capacity could be justified by 2025. Investment opportunities also exist in several other C2 and C3 value chains.
The former includes products such as ethylene oxide (EO); monoethylene glycol (MEG); polyvinyl chloride (PVC) and its raw materials ethylene dichloride (EDC) and vinyl chloride monomer (VCM); vinyl acetate monomer (VAM); styrene monomer; and ethylene vinyl acetate copolymers (EVA).
All of these are expected to experience 6–12% annual demand growth, which will justify investments in one or more world-scale plants. For example, PVC demand is now in excess of 3 MMmt/yr, with more than half covered by imports. Styrene monomer demand is over 700,000 MMmt and fully met by imports.
Rough calculations show that by 2025 India will need about 30 world-scale plants in the ethylene value chain, including 23 facilities in the vinyl chain, four for EO/MEG, and two for styrene monomer
The propylene (C3) value chain is even more barren, with about 95% of all propylene converted to PP. The opportunities expected to arise include acrylic acid and esters, phenol and acetone, oxo-alcohols (butanol, 2-ethylhexanol), propylene oxide and glycol, and acrylonitrile. If expected demand growth is maintained, at least nine worldscale plants can be built by 2025: three each in the acrylic acid, cumene/phenol/acetone, and oxo-alcohol value chains. Other investment opportunities include methyl methacrylate and polycarbonate resin.
Fine and specialty chemicals
Specialty chemicals are often customized offerings, based on an in-depth understanding of customer needs and problems. While plant capital costs are lower than those for commodity chemicals, the business requires significant application development and R&D investments to stay relevant. Products are sold based on their functionality in the intended application, rather than on their chemical identity. Companies often take strong intellectual property positions such as patented formulations and registered trade names.
Several Indian companies now hold leading positions globally in fine and specialty chemicals, at times with 30–80% of global capacity.
Conventional wisdom holds that the specialty chemicals business enjoys better margins than commodity chemicals. But that is not always true — the realities in India depend on many factors, including the nature of the specialty, competition, technological complexity, and timing (7).
The Indian specialty chemicals market is still in its infancy. While size estimates vary, US$20 billion is not far off the mark (Table 2). Of the 1,000 specialty chemical companies, most are home-grown, with a few major international companies. The industry is fragmented by several companies constrained by capital, technology, and managerial bandwidth. These companies are little more than imitators that offer low-quality products made without sufficient regard to environmental standards and safety.
Table 2. Colorants and paints and coatings account for half of India’s $20 billion specialty chemicals market. | ||
Segment | Market Size, US$ Million | Growth Rate, % |
Colorants | 5,400 | 11% |
Paints and Coatings | 5,300 | 10% |
Flavors and Fragrances | 3,300 | 14% |
Surfactants | 3,000 | 13% |
Textile Chemicals | 1,250 | 12% |
Personal Care | 700 | 14% |
Construction Chemicals | 610 | 12% |
Polymer Additives | 477 | 10% |
Water Treatment | 458 | 14% |
While the overall Indian chemical industry has grown 10–12% annually, the specialty chemicals business has grown at about 14%. This figure, however, camouflages some challenges. For instance, company performance in sectors such as textile dyes, pigments, and leather chemicals has been impacted in the past few years by issues in their end-use segments. In contrast, segments such as construction chemicals, personal care ingredients, and water treatment chemicals have grown up to 20% in the same time period.
Indian specialty chemical companies also face product stewardship challenges. Many chemicals have come under the regulatory microscope, especially in Europe. The European chemical legislation — Registration, Evaluation and Authorisation of Chemicals (REACH) — is rewriting chemical safety rules for certain chemicals suspected to be dangerous to human health and the environment.
These include chemicals used in fire retardants, surfactants such as nonylphenol ethoxylates, and plasticizers such as dioctyl phthalate. All these substances could face restrictions or even outright bans. While these moves will first impact companies exporting chemicals and other goods to Europe, it may not be long before Indian regulators seek similar legislation.
Feedstock options for India’s chemical industry
Naphtha. India has little access to the inexpensive gas that fuels Middle Eastern and North American petrochemical production. This situation is unlikely to change, because imported LNG will always be burdened with high handling and transportation costs. India, however, has refining capacity in excess of domestic requirements, and large quantities of naphtha are now being exported. Naphtha export volumes have risen almost every year since 2009, when India became a net naphtha exporter. This surplus is expected to increase as new refining capacity is built. In 2015, naphtha exports were close to 7 MMmt and sufficient to serve at least two worldscale ethylene crackers.
Cheap oil has brought back naphtha as a competitive feedstock for petrochemical production. Its price has almost halved from the peak attained when crude oil prices soared above $140 per barrel and significantly narrowed the cost advantage enjoyed by Middle Eastern and North American gas-based producers.
India’s crude oil refining companies are seeking to integrate downstream into petrochemicals, to improve margins and cater to underserved markets. Naphtha production is scattered across the country, which presents challenges for petrochemical producers eyeing it as feedstock. Much naphtha capacity (about 12.5 MMmt/yr) is concentrated in the west, and petrochemical production is best located in this part of the country.
The most critical aspect of naphtha cracking will be gainful and complete utilization of all coproducts, particularly heavier olefins (C4s and C5s). Their contribution to operating margins will be significant, provided cracking is done at scale and in a comprehensive manner.
Biomass. India is well positioned to make use of biomass, thanks to its strong agricultural base. Sugarcane biomass is the most well developed and available in significant quantities at a single site. Its separation into cellulose, hemicellulose, and lignin can provide raw materials for further valorization. Efforts by private companies, aided by government funds, have provided some breakthroughs.
Publicly and privately funded organizations have developed second-generation ethanol technologies and established pilot- and demonstration-scale projects. Commercial plants could be online in about two years.
India has 600 m.t. of extra biomass with an average agricultural growth rate of 10 m.t./ha-yr. Scientists have proven an enhanced growth rate of 100 m.t./ha-yr, and ongoing experiments aim to take it further, to 150 m.t./ha-yr. The principal biomass conversion technologies are biomethanation, thermal pyrolysis, and gasification. Biomethane production will remain restricted to the transport sector and household cooking. Pyrolysis must be followed by biorefinery processing and gasification by Fischer-Tropsch reaction.
India has attractive biomethanation economics. However, the country needs to develop reliable, economical technologies for pyrolysis and gasification.
Pharmaceuticals
The Indian pharmaceutical industry is considered a global success story, and its technology development is progressing well. Its success, however, hides somedisturbing trends. The industry relies heavily on imports of active pharmaceutical ingredients (APIs) and intermediates, mostly from China. APIs and advanced intermediates imports increased from US$800 million in 2004 to US$3,461 million in 2013, with China’s share rising from 39% to 58% during that time. In volume terms, China’s dominance is even more glaring: In 2014, Chinese imports accounted for 75% of API and intermediates tonnage. For most of India’s ten largest pharmaceutical companies, Chinese imports accounted for 30–50% of total imported raw materials, with some companies importing more than half their needs. Inexpensive Chinese imports have rendered penicillin manufacture unviable in India, forcing the closure of four production units.
Even for APIs where India has a formidable global presence, dependence on imports for intermediates is a matter of concern. For example, India is the leading producer of paracetamol (a commonly used analgesic/antipyretic) and manufactures over 30,000 MMmt/yr. Most paracetamol is produced from the intermediate para-aminophenol, nearly 30,000 tons of which was imported from China in 2015.
Promoting domestic manufacture of APIs and their intermediates will require a balancing act that does not jeopardize the hard-won global competitiveness of the Indian formulations industry. The latter does have a legitimate right to access raw materials — including APIs — in the manner that makes the most commercial sense.
Creating a welcoming investment environment will strengthen the backbone of India’s pharmaceutical industry. The Katoch Committee, appointed in 2013 to recommend steps to encourage domestic production, stressed the need to establish several “API Parks” with shared facilities, including common effluent treatment plants, testing facilities, captive power plants, and services such as storage, testing laboratories, and intellectual property rights management. The committee recommended creation of fee-based special-purpose vehicles to offer these services to park participants. It also suggested several fiscal and financial supports for investors, and strengthening industry-academia collaborations (8). The committee’s recommendations are key to augmenting India’s API and intermediates manufacturing capabilities and an important step toward ensuring holistic development.
Agrochemicals
Agriculture is critical to the Indian economy and food security, accounting for 15% of gross value added. About 60% of rural households rely on farming for their livelihood.
Indian agriculture faces many challenges and must adapt to doing more with less. A growing population, urbanization, and industrialization are shrinking farmlands, and demands from an increasingly affluent population — including in rural India — are rising. Water availability for irrigation has become a source of contention, leading to disputes with neighboring countries and between states. Groundwater depletion has reached alarming levels, especially in areas at the forefront of the Green Revolution, which turned India from an importer of food grains to an exporter.
Increasing agricultural productivity is important and will require diverse approaches to consolidation of land holdings. Consolidation will yield economies of scale, mechanized farming, and wider adoption of high-yielding seeds, including those genetically modified. Better nutrient management, including balanced fertilizer usage, more efficient water management, and integrated pest management (IPM), combining chemical and biological approaches, will also be beneficial.
Unlike other agro-based economies, India is fortunate to have a vibrant agrochemicals industry — the fourth-largest in the world after the U.S., Japan, and China. The industry produces mostly generic (off-patent) products for the local market and, increasingly, for export. India has become the dominant producer of products such as synthetic pyrethroids and isoproturon (the latter made without using phosgene). In 2015–2016, the industry’s output was valued at about US$4.3 billion, divided roughly equally between domestic sales and exports. The overall market is expected to grow at 10–12% annually to about US$7 billion by 2019. Exports are expected to grow faster (12–14% compound annual growth rate) than the domestic market (7–9% CAGR) (9).
While India’s agrochemicals industry has made considerable progress, it does have vulnerabilities. The market is skewed toward insecticides, which is not surprising given India’s tropical climate, and fungicides and herbicides shares are small. Distribution, however, is slowly becoming more balanced. The introduction of pest-resistant genetically modified cotton (Bt-cotton) has dramatically reduced insecticide use but not eliminated it. The evolution of the agricultural basket — with a larger proportion of horticultural products, fruits, and vegetables, at the expense of food grains and cotton — is increasing fungicide use. A labor shortage, surprising for such a populous country, is driving greater herbicide usage, as mechanical weed removal gives way to chemical approaches.
Much of the industry is focused on making and marketing older-generation products that could be edged out by newer patented products that are more efficacious, targeted, and safer for human health and the environment.
Indian agrochemical companies are not likely to invest in research for new molecules, given the limitations posed by individual and collective size. Continued company success will hinge on their ability to adopt one of four broad business strategies: going global, forging marketing alliances, entering into toll and contract manufacturing arrangements, or focusing on formulation development. Several companies are already adopting one or more of these approaches.
The agrochemicals business is changing dramatically. The industry is now viewed holistically, with a portfolio of seed and biotech capabilities that complement the traditional chemicals business. The global business landscape is also undergoing reorganization, with several mega deals in the making, including the Dow-DuPont merger, Chem China’s acquisition of Syngenta, and Bayer’s purchase of Monsanto. These dynamics will play out directly in the Indian market, where all of the multinationals have a presence. They could also impact existing relationships with Indian vendors and force realignment of marketing strategies.
Education and research
The specialty chemicals sector’s capital and operating expenditures are comparable, or in some cases lower than, global standards. Costs can be reduced by as much as 50% via process intensification techniques, which could also increase production to US$100 billion per year. India has adequate research and education infrastructure to support process intensification work, with 90,000 masters and 6,000 PhD chemistry graduates and 1,000 masters and 300 PhD chemical engineering graduates each year. Considerable work is still needed to generate the appropriate skills to meet the needs of specialty chemicals manufacturing and research.
Concluding thoughts
There is broad consensus that India can achieve and maintain 7% GDP growth for a reasonable period of time. The Confederation of Indian Industry (CII) has set a target to triple the size of the Indian chemical industry between 2015 and 2025, which, if achieved, will take the industry to about US$430 billion by 2025. This ambitious target will not be achieved if business runs as usual. It will require a coordinated blend of policy interventions and company-level initiatives plus greater international market access.
The industry will need to recognize paradigm shifts in technology and markets that will have consequences for Indian companies (10). In fine chemicals, for example, a transition from batch to continuous processing is well underway, offering the benefits of safety, quality, scale, and investment.
The recent replacement of multiple indirect taxes by a single goods and services tax (GST) will positively impact manufacturing. With long value chains, the chemical industry will be a significant beneficiary, as taxes impact pricing of products and services, supply chain optimization, IT, accounting and tax compliance systems, and more (11).
While the chemical industry will continue to be dependent on oil and gas for the near future, it is prudent to look at alternative feedstock options. Biomass and coal come to mind, and a more comprehensive and coordinated approach is needed to exploit both. India had a thriving alcohol-based chemicals industry that was decimated by the diversion of ethanol as a gasoline additive. While coal is making a comeback for fertilizer production, using it for chemicals such as methanol, olefins, and derivatives, which seems to have worked well in China, need to be carefully evaluated in the Indian context. Integrated gasification combined cycle (IGCC) plants to burn even low-grade coal efficiently and cleanly for power generation need to be pursued further.
Unlike many other countries with significant chemical industries, India still lacks a national inventory that identifies chemicals in commerce and the risks and hazards they pose in their value chains. This should become a priority project with clear timelines for the phase-out of harmful products and support for innovation of safer substitutes.
The industry will also have to decouple its past growth models and reexamine available opportunities. Many leading global companies are reeevaluating their portfolios through the lens of sustainability, and there are lessons for Indian companies here as well.
India has a proven track record of entrepreneurship. The country also has some strengths in technology development that have not been fully leveraged. Its chemical industry has a long way to go in forging intercompany and academic partnerships to drive innovation, although some pharmaceutical companies have nurtured internal capacities to meet their own business requirements. Long-term research is still lacking and even companies that like to be counted in global rankings have only made tentative forays.
India must make wise investment choices, and fine and specialty chemicals hold particular promise because they do not expose the economy’s weaknesses (e.g., high cost of capital, lack of access to hydrocarbons, and high energy costs) while leveraging strengths (e.g., high technical skills, and low-cost innovation capabilities). Developing a fine and specialty chemicals business will provide significant opportunities for India’s chemical companies. However, the business will not thrive without the backing of a robust and broad-based industry. Finally, industry must have access to enough workers with the right skill sets and motivations. Given the industry’s poor image among the country’s youth, this is no small challenge.
Literature Cited
- Rama Rao, A.V., “Indian Organic Chemical Industry: Decades of Struggle and Achievements,” Indian Journal of History ofScience,49 (4), pp. 399–412 (2014).
- de Sousa, J. P., “History of the Chemical Industry in India,” Technical Press Publications, Bombay, India (1961).
- Committees and Commissions in India, “1977 Report — Committee to Conduct Study and Make Recommendations for the Development of Industries Based on Ethyl Alcohol,” 15 (A) (1977).
- TATA Strategic Management Group, “Handbook on Indian Chemical Industry,” https://fenix.tecnico.ulisboa.pt/download-File/1407993358852239/Roland_Berger_India_Chem_20101109.pdf. (2016).
- Chemicals & Petrochemicals Manufacturers’ Association, “Indian Petrochemical Industry: Review of 2015–16 and Outlook for 2016–17,” APIC Conference Proceedings, Charlotte, NC (2016).
- Raghavan, R., “Leveraging Naphtha for Petrochemicals: Opportunities and Challenges,” Chemical Weekly, pp. 135–136 (Aug. 8, 2017).
- Confederation of Indian Industry, “CII Report on Key Feedstock for Speciality Chemicals” (Mar. 2016).
- Katoch, V. M., “Committee Report on Active Pharmaceutical Ingredients: Recommendations,” Ministry of Chemicals and Fertilizers (Feb. 2015).
- Raghavan, R., “Indian Agrochemicals Industry: On the Throes of Change,” Chemical Weekly, pp. 135–136 (Dec. 20, 2016).
- Raghavan, R., “Achieving 3X Growth in the Indian Chemical Industry: What Will It Take?” Chemical Weekly, pp. 135–136 (Dec. 6, 2016).
- Raghavan, R., “GST — A Welcome Measure with Wide-Ranging Implications for Manufacturing,” Chemical Weekly, pp. 135–136 (Aug. 16, 2016).
Acknowledgments
The authors are grateful to Professor M. M. Sharma, Former Director, Institute of Chemical Technology, for his valuable guidance and suggestions.
Copyright Permissions
Would you like to reuse content from CEP Magazine? It’s easy to request permission to reuse content. Simply click here to connect instantly to licensing services, where you can choose from a list of options regarding how you would like to reuse the desired content and complete the transaction.