CPI companies are switching to fixed valves despite a slight loss in operational flexibility. Fixed valves offer better reliability, fouling resistance, and more robust valve designs.
Distillation is an essential separation technology for a wide range of applications in the chemical process industries (CPI). Of critical importance to the separation are the mass-transfer devices on distillation trays that create intimate mixing of the liquid and vapor.
The most common types of mass-transfer devices for conventional cross-flow trays (Figure 1) are moving valves and fixed valves. Although moving valves provide operational flexibility, many CPI companies have started selecting fixed valves. They are willing to accept the loss of some operational flexibility to gain benefits provided by fixed valves, including better reliability, fouling resistance, and more robust valve designs that can better withstand operational upsets.
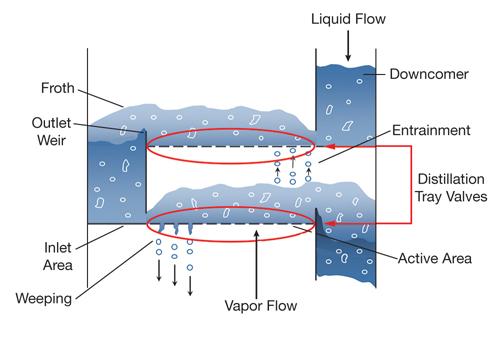
▲Figure 1. In a conventional cross-flow distillation tray, liquid moves down as vapor moves up.
This article discusses moving valves and fixed valves, explains their advantages and disadvantages, and offers guidance on selecting the appropriate valves for distillation trays. The article also includes several examples that illustrate the benefits of fixed valves.
Bubble-cap trays and sieve trays
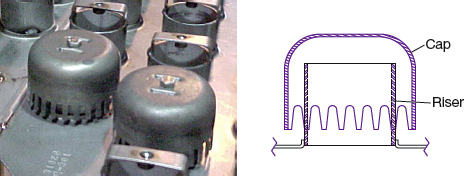
▲ Figure 2. A bubble-cap tray has risers on each hole with caps covering the risers.

▲ Figure 3. Sieve trays have round holes punched or drilled into the tray.
Before discussing fixed and moving valves, it is important to first discuss two non-valve tray designs — bubble-cap trays (Figure 2) and sieve trays (Figure 3) — that were used in the early days of industrial distillation. These provide a reference point against which to compare other designs.
Bubble-cap trays have been in use since the early 1800s (1). The bubble-cap tray contains holes with a riser on each hole covered by a cap. Vapor passes through the riser as it moves upward and is forced downward by the cap, and then it moves back up as it bubbles through the liquid on the tray. Bubble-cap trays require extensive labor and more materials to produce than extruded fixed valves, and therefore are significantly more expensive (by a factor of 2–3). Although very common in older plants, bubble-cap trays have fallen out of favor for general distillation use due to their high cost.
Bubble-cap trays do have advantages and are appropriate for some low-liquid-rate niche applications, as well as applications with widely varying vapor loads. If designed and installed properly, bubble-cap trays do not weep. If weeping occurs on a bubble-cap tray, it is the result of improper design or incorrect installation. A well-sealed bubble-cap tray can have almost infinite vapor turndown (ignoring tray activity, which is discussed later).
Sieve trays, which contain round holes cut or punched through the tray deck, were developed around the same time as bubble-cap trays. In contrast to bubble-cap trays, sieve trays are relatively easy to produce, as production involves simply creating round holes in the tray deck. While sieve trays are inexpensive to produce, they generally do not perform as well — in terms of capacity, flexibility, and fouling resistance — as other mass-transfer devices.
Sieve trays begin to experience entrainment at lower vapor flowrates than fixed-valve or moving-valve trays. Unlike on a valve tray, where vapor is deflected horizontally as it exits a fixed or moving valve, vapor exiting the holes of a sieve tray moves vertically. The vertically directed vapor creates higher froth heights, increasing the potential for entrainment.
This vapor deflection increases the vapor velocity on the tray deck around fixed or moving valves, which helps prevent zones of stagnation where solids can deposit, polymerization can begin, or corrosion can occur. Thus, valve trays offer more fouling resistance than small-hole sieve trays.
Valves
Although bubble-cap and sieve trays are sufficient for certain applications, valve trays have become the most common mass-transfer devices in the CPI. The vapor deflection helps induce more intimate vapor-liquid contacting than is experienced on sieve trays, and valve trays are less expensive than bubble-cap trays.
The valves can be fixed or moving. Fixed valves are permanently open, while moving valves are lifted open by the vapor flowing up through the tray holes.
Moving valves
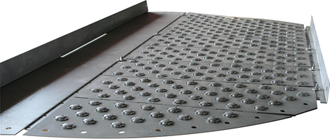
▲ Figure 4. A moving-valve tray has valves that move up and down.
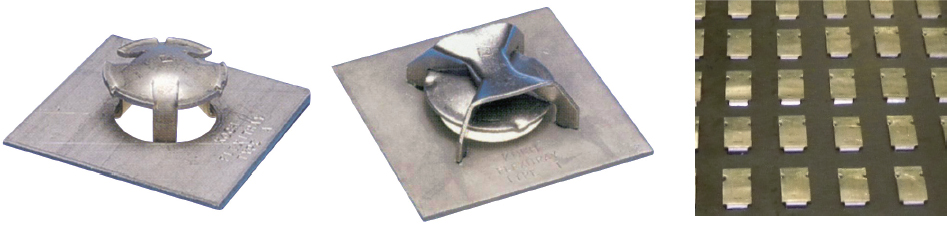
▲ Figure 5. Moving valves come in several shapes and sizes, including round valves with legs that protrude through the tray orifice (left), caged assemblies (center), and rectangular valves (right).
After its introduction in the early 1950s, the modern moving-valve tray (Figure 4) became a standard for distillation in the chemical industry. Its chief advantage is that its variable vertical movement accommodates a wide operating range. The range of a valve’s movement is determined by either the length of the valve legs that protrude through the tray deck orifice (Figure 5, left and right images), or by a cage assembly (Figure 5, center) that restricts vertical movement.
To take advantage of the moving valve’s wide operating range, an operator can simply turn up or turn down the vapor flowrate within a certain operating window. Moving valves can generally achieve a nominal turndown (i.e., the ratio of the maximum vapor flowrate to the minimum vapor flowrate) of 4:1.
Turndown ratio is primarily a function of available pressure drop. As the vapor flowrate decreases, so does the pressure drop across the tray. When the tray pressure drop becomes too low, the tray begins to weep, which causes the efficiency of the column to decline. On a moving-valve tray, however, some of the valves begin to close when the vapor flowrate decreases, reducing the effective open area of the tray and limiting the tendency to weep.
Another factor affecting turndown for moving-valve trays is tray activity. As the vapor flowrate decreases, so does the number of valves on the tray actively bubbling vapor. This is particularly important for multipass trays, which typically require a higher vapor flowrate to ensure that all passes are actively bubbling vapor. Tray efficiency declines sharply if one pass becomes inactive. The more flow passes a tray has, the more difficult it is to ensure complete activity on that tray.
One way to improve the turndown performance of moving-valve trays is to install the valves in rows of alternating metal thickness (e.g., alternate 14-gauge and 16-gauge). Using valves of slightly different weights gives the designer control over which valves close first as the vapor flowrate decreases. This design can extend the operating range beyond the 4:1 turndown mentioned previously. Turndown ratios of 10:1 are possible with properly designed moving valves, provided the available pressure drop and tray spacing are reasonable and the system is nonfoaming.
While the standard moveable valves provide a high hydraulic turndown ratio and are more efficient than sieve trays, they also have disadvantages:
- Because they typically have more surface area available for the deposition of contaminants, moving valves are more prone to fouling than fixed valves. This is a serious concern for towers operating in severe environments that have a much higher potential for particulate deposition caused by dirt and debris, various forms of corrosion (e.g., from acids), dewpoint salt formation, and, in some cases, polymerization.
- As moving valves open and close, the valve legs can contact the edges of the orifice, which can cause erosion and increase corrosion.
- Fouling or polymer deposition can cause moving valves to stick to the tray deck. To eliminate sticking, most valves are equipped with dimples that...
Would you like to access the complete CEP Article?
No problem. You just have to complete the following steps.
You have completed 0 of 2 steps.
-
Log in
You must be logged in to view this content. Log in now.
-
AIChE Membership
You must be an AIChE member to view this article. Join now.
Copyright Permissions
Would you like to reuse content from CEP Magazine? It’s easy to request permission to reuse content. Simply click here to connect instantly to licensing services, where you can choose from a list of options regarding how you would like to reuse the desired content and complete the transaction.