This article focuses on adsorbents, including activated carbon, zeolite molecular sieves, and polymeric adsorbents, as well as ion exchange resins.
Adsorption is a unit operation that exploits the attraction of solutes in a liquid or gas to a solid surface. This attraction allows the solutes to be removed, or solutes with different affinities for the solid to be separated. The first article (1) of this two-part series presented the fundamentals of adsorption, including equilibrium and mass-transfer considerations, the mass-transfer zone concept, breakthrough, regeneration, and column sizing. This article, Part 2, covers the most widely used adsorbents — in order of decreasing commercial importance (2, 3): activated carbon, zeolite molecular sieves, silica gel, activated alumina, and polymeric adsorbents — with discussion of their physical characteristics, suitable applications, and regeneration requirements. Ion exchange, a process that is similar to adsorption and is used to remove ions from solution, is also reviewed.
Activated carbon
Activated carbon is a hydrophobic, highly porous adsorbent that is produced by roasting one of a variety of organic precursors, including coconut shells, wood, lignite, and coal. Roasting is followed by activation, which increases adsorption capacity by removing contaminants from the surface of the adsorbent. Activation can be done thermally, by heating the material to 1,000°C or higher to decompose impurities. Afterward, the material is exposed to an oxidizing atmosphere, which substantially increases the pore volume. Alternatively, chemical agents such as phosphoric acid can be used to activate the adsorbent.
Activated carbon products may be granular (i.e., made directly from a granular precursor), pelletized, or crushed to a powder. Powdered activated carbon has shorter diffusion paths and thus higher mass-transfer rates. However, powdered carbon is suitable only for the treatment of liquids in a batch mix tank, because the high pressure drop precludes its use in a column. Spent powdered carbon must be removed by filtration, and regeneration is not practical.
Activated carbon is a highly versatile adsorbent, because its performance characteristics can be tailored by varying the precursor, roasting conditions, and activation method. Consequently, products are available for a wide range of applications, for treating both gases and liquids. Liquid applications include potable water treatment (discussed later), groundwater remediation, industrial and municipal wastewater treatment, sweetener decolorization, and chemical and pharmaceutical processing. Examples of gas applications are removal of organics from waste gas, capture of gasoline vapor emissions from automobiles, and adsorption of gaseous radionuclides from nuclear power plants.
Key properties of four common types of carbon are shown in Table 1. Coconut-derived carbons are generally considered high in quality, as evidenced by their high hardness (so they experience less attrition), low ash content, low dusting tendency, relative ease of regeneration, and high iodine number. The iodine number is the milligrams of elemental iodine adsorbed per gram of carbon. This funda-mental performance parameter is an indicator of activity, particularly for liquid applications. A higher iodine number is better.
Table 1. Activated carbon can be generated from a variety of precursors, including coconut, coal, lignite, and wood. | ||||
Coconut | Coal | Lignite | Wood (Powdered) | |
Micropores (<20 Å) | High | High | Medium | Low |
Macropores (>500 Å) | Low | Medium | High | High |
Hardness | High | High | Low | N/A |
Ash, % | 5 | 10 | 20 | 5 |
Water--Soluble Ash | High | Low | High | Medium |
Dust | Low | Medium | High | Very High |
Ease of Regeneration | Good | Good | Poor | None |
Bulk Density, g/cm3 | 0.48 | 0.48 | 0.40 | 0.35 |
Iodine Number | 1,100 | 1,000 | 600 | 1,000 |
Coal-derived products have higher ash content and are more prone to dusting. Lignite-derived carbons are lower in quality, with low hardness, high ash content, high dusting tendency, poor regenerability, and low iodine number. The large number of macropores allows better diffusion of large molecules, which makes lignite-derived carbons suitable for use with liquids. However, more macropores means less surface area per unit volume of adsorbent, and, in turn, lower capacity. Powdered carbon derived from wood also has a large number of macropores, as well as low ash content and a high iodine number — but powdered carbons have several disadvantages, as outlined earlier.
To illustrate the effects of fluid properties and operating conditions on activated carbon performance, consider potable water treatment as an example. The objectives are to improve taste and to remove precursors of toxic products that would otherwise form during chlorination. Activated carbon is a hydrophobic adsorbent, and it typically removes large molecules more easily because they tend to be more hydrophobic than small molecules. Performance is better at acidic pH, because many contaminants in public water supplies are organic acids that originate from decaying plant matter, and the protonated form is more hydrophobic than the salt form. A rule of thumb is that the required bed size increases by 20% for every pH unit above 7 (4).
Higher feedwater hardness equates to greater polarity. Higher polarity causes a shift in the equilibrium distribution in favor of the solid, which increases adsorption. In addition, adsorption improves with a higher adsorbate concentration, because the amount adsorbed at equilibrium is correspondingly higher. In water treatment service, activated carbon typically adsorbs about 10% of its weight in organics (4).
As with adsorption processes in general, water treatment with activated carbon typically improves with decreasing flowrate. The usual residence time is 15–30 min, although the faster mass transfer obtained with smaller particles allows higher flowrates. In general, 20×50 mesh particles (with diameters of 0.3–0.8 mm) can accommodate twice the flowrate of 12×40 mesh ones, which in turn can handle twice the flowrate of 8×30 mesh carbon. However, even though smaller particles can accommodate higher flowrates, they have higher pressure drops (4).
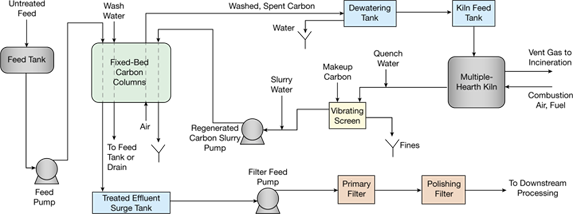
▲Figure 1. In this process for treating a liquid with activated carbon, the treated column effluent is filtered before it moves to downstream processing. Spent, washed carbon is conveyed by air to a dewatering tank, then fed to a kiln for regeneration.
In an activated carbon liquid treatment plant (Figure 1), the treated column effluent is filtered to remove any carbon fines that pass through the screen supporting the carbon bed, or to catch particles that may escape because of a screen or gasket failure. A polishing filter may be necessary to remove fine particulates, or to protect the downstream process in the event of a primary filter malfunction.
In the process depicted in Figure 1, spent, washed carbon is conveyed by air to a dewatering tank, where...
Would you like to access the complete CEP Article?
No problem. You just have to complete the following steps.
You have completed 0 of 2 steps.
-
Log in
You must be logged in to view this content. Log in now.
-
AIChE Membership
You must be an AIChE member to view this article. Join now.
Copyright Permissions
Would you like to reuse content from CEP Magazine? It’s easy to request permission to reuse content. Simply click here to connect instantly to licensing services, where you can choose from a list of options regarding how you would like to reuse the desired content and complete the transaction.