Natural disasters present chemical plants with unique challenges. Reduce environmental harm and avoid regulatory penalties by mitigating hazardous waste releases during and after these events.
Since 1980, the U.S. has experienced 40 hurricanes that were defined as billion-dollar disasters. The damages from the trio of hurricanes that occurred in 2017 — Hurricanes Harvey, Maria, and Irma — incurred costs of more than $250 billion combined (Table 1) (1). That’s more than 30% of the total damages since 1980, making that year the most costly year in 38 hurricane seasons (2). Unfortunately, the frequency and intensity of storms seems to be trending upward.
Table 1. Hurricanes have the potential to incur tremendous financial impact. These are the top five costliest U.S. hurricanes on record (1). | |
Hurricane | Cost |
1. Katrina (2005) | $161 billion |
2. Harvey (2017) | $125 billion |
3. Maria (2017) | $90 billion |
4. Sandy (2012) | $71 billion |
5. Irma (2017) | $50 billion |
The Atlantic hurricane season officially begins on June 1 and lasts until November 30. Each year, the National Oceanic and Atmospheric Administration (NOAA) releases a hurricane season outlook that serves as a general guide to the expected overall activity during the hurricane season (3). However, such an outlook cannot predict severity or the level of hurricane activity that any one location will experience.
Considering the magnitude of the destruction caused by natural disasters like hurricanes, companies and professionals in the chemical process industries (CPI) should prepare well in advance for these costly and potentially catastrophic events.
Hurricanes put chemical process plants at tremendous risk in terms of asset damage, environmental mishaps related to the loss of hazardous materials, and risk to personnel and the community, all of which can be both costly and deadly. These risks can be reduced by proper planning and disaster preparedness.
Natural disasters can create significant health and safety risks for the individuals who work within CPI facilities, often in the form of hazardous waste spills and leaks. Potential environmental risks also include air, water, and ground or soil contamination due to runoff.
To reduce the risks of injury, environmental harm, or regulatory penalties, a successful disaster response requires extensive expertise and knowledge of hazardous materials and waste management, including applicable procedures and regulations.
This article discusses some hazardous wastes that are common in CPI facilities. It outlines five considerations that chemical engineers, environmental engineers, and environmental, health, and safety (EHS) professionals should keep in mind when handling waste streams before, during, and after flooding, high winds, and other extreme weather conditions.
Defining hazardous waste
The U.S. Environmental Protection Agency (EPA) defines hazardous waste as “waste with properties that make it dangerous or capable of having a harmful effect on human health or the environment” (4).
EPA regulates hazardous waste under the U.S. Resource Conservation and Recovery Act (RCRA), which was enacted in 1976 to ensure that these wastes are managed in a safe and compliant manner. The growing amount of waste generated has made it increasingly important for waste management personnel to develop strategies to manage wastes safely (5).
RCRA established a framework for the proper management of hazardous wastes, and from this authority, EPA has established a comprehensive regulatory program to ensure that hazardous waste is managed safely from cradle to grave — i.e., from the time it is created, through transportation, treatment, and storage, until it is disposed (6).
All generators must follow the framework established by RCRA. A hazardous-waste generator is defined as any organization that produces a hazardous waste. Generators of hazardous waste are regulated based on the amount of hazardous waste they create in a calendar month, not the size of their business or facility (7). EPA recognizes three categories of generators in the regulations:
- very-small-quantity generators (VSQGs) produce 100 kg (~220 lb) or less per month of hazardous waste, or 1 kg (~2 lb) or less per month of acutely hazardous waste
- small-quantity generators (SQGs) produce more than 100 kg (~220 lb), but less than 1,000 kg (~2,200 lb) of hazardous waste per month
- large-quantity generators (LQGs) produce 1,000 kg (~2,200 lb) per month or more of hazardous waste, or more than 1 kg (~2 lb) per month of acutely hazardous waste.
Many substances that are handled, stored, and manufactured within CPI plants are regulated as hazardous waste. Therefore, engineers and other personnel must follow all requirements outlined within RCRA, as well as any other relevant federal, state, or local regulations that dictate how to properly manage and dispose of hazardous waste.
Common hazardous wastes
Listed wastes are wastes that come from common manufacturing and industrial processes. They can also come from specific industries, or can be discarded commercial products. A waste is determined to be a hazardous waste if it is specifically listed on one of four lists — the F, K, P, and U lists — that are found in Part 261 of Title 40 of the Code of Federal Regulations (CFR).
F List. The F List, found at 40 CFR Section 261.31, identifies wastes from common manufacturing and industrial processes as hazardous (8). Because the processes generating these wastes can occur in different sectors of industry, F-List wastes are known as wastes from nonspecific sources (9). They are divided into seven groups that depend on the type of manufacturing or industrial operation that creates them:
- spent solvent wastes
- electroplating and other metal-finishing wastes
- dioxin-bearing wastes
- chlorinated aliphatic hydrocarbons production wastes
- wood-preserving wastes
- petroleum refinery wastewater treatment sludges
- multisource leachate.
K List. The K List identifies hazardous wastes from specific sectors of industry and manufacturing that are considered to be source-specific wastes. To qualify as a K-listed hazardous waste, a waste must fit into one of 13 categories on the list, and the waste must match one of the detailed K-List waste descriptions in 40 CFR Section 261.32 (8). The 13 industries that generate K-List wastes are:
- wood preservation
- organic chemicals manufacturing
- pesticides manufacturing
- petroleum refining
- veterinary pharmaceuticals manufacturing
- inorganic pigment manufacturing
- inorganic chemicals manufacturing
- explosives manufacturing
- iron and steel production
- primary aluminum production
- secondary lead processing
- ink formulation
- coking.
P and U Lists. The P and U Lists designate hazardous waste as pure, commercial-grade formulations of certain unused chemicals that are being disposed of. For a waste to be considered a P- or U-List waste, it must meet the following criteria: the waste must contain one of the chemicals listed on the P or U List, the chemical in the waste must be unused, and the chemical in the waste must be in the form of a commercial chemical product.
The P List identifies acute hazardous wastes from discarded commercial chemical products. The P List can be found at 40 CFR Section 261.33 (8). The U List identifies hazardous wastes from discarded commercial chemical products and can be found in the same section of the CFR. Both the P- and U-listed chemicals refer to materials or products that can no longer be used for their intended purpose. However, the P-listed chemicals are referred to as acutely hazardous waste because they are very hazardous even at small concentrations or amounts, like cyanides.
Other hazardous wastes. Other hazardous wastes are known as characteristic wastes. These are wastes that exhibit any one or more of the following characteristic properties: ignitability, corrosivity, reactivity, or toxicity.
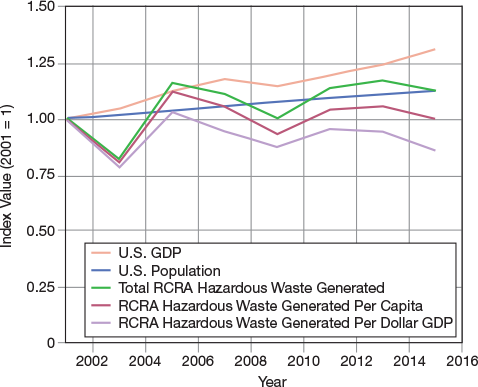
▲Figure 1. Total hazardous-waste generation was 12.7% higher in 2015 than it was in 2001, but fluctuations occurred in the intervening years (10).
According to the EPA, the amount of total hazardous waste generated in the U.S. is trending upward (Figure 1) (10). From 2001 to 2015, the quantity of hazardous waste generated in the U.S. ranged from 20.3 to 29.1 million tons. CPI facilities should consult the EPA’s website for an inventory of listed and characteristic wastes. State regulatory requirements for waste generators may be more stringent than those of the federal RCRA program. Be sure to check state-specific policies, which can also be found on the EPA’s website (11).
Develop an emergency contingency plan
Being prepared for potential disasters can help CPI firms to mitigate some potential damage and safeguard their employees, the community, and the environment. Outlined here and in the following sections are several steps companies should take to protect their facilities in the event of a natural disaster.
Every large chemical facility and refinery should have a contingency plan in place for extreme weather events. This should include an emergency response plan (which some third-party waste-management providers may create for you as part of an existing service agreement).
Begin by assessing the facility’s risk for incidents related to natural disasters. For example, a business on the Pacific coast has the greatest risk of being impacted by earthquakes, wildfires, and mudslides. However, a facility on the Atlantic coast may be more likely to encounter hurricanes and flooding.
Most importantly, strategize on a successful disaster-response plan and have the plan in place before it is needed. When creating a natural disaster emergency plan, consider several factors. First, engineers and plant executives should work together to determine emergency response roles. Decide who will make crucial decisions in the event of a storm and who will be involved in hazardous-waste management and removal.
Many other elements should also be considered in the emergency response plan. Determine how to secure all hazardous chemicals safely outside of potential flooding areas. Identify what hazardous wastes could be generated as a result of loss of containment or loss of power. Also consider what type of reporting will need to be completed after the incident.
An ideal emergency response plan should include a proper, strategic communication protocol and chain of command. One of the biggest mistakes companies make when preparing for a natural disaster is a lack of communication. Communication that is not handled properly creates additional obstacles for organizations to overcome during and after the disaster.
The importance of a robust contingency plan can be demonstrated with a real-life example in which a chemical plant’s emergency plan failed during Hurricane Harvey in 2017. The hurricane wreaked havoc on Houston, TX, and left the facility without power and inundated by an unprecedented six feet of water. Although the company took several measures to safely shut down the plant ahead of time and brought in multiple backup power generators, the multiple layers of protection to refrigerate potentially toxic substances on-site failed (12). Some of the chemical containers exploded and caught fire, emitting large fume clouds. Police and emergency workers filed a $1-million lawsuit against the chemical company, claiming they were injured after the company failed to take adequate steps to avoid a fire caused by the substances (13).
If the company had drafted and implemented a more robust contingency and safety plan, the explosion, fire, and resulting injuries might have been prevented.
Partner with a company that specializes in emergency planning
In many cases, the correct response to a disaster might not be obvious to the untrained eye. After a disaster, hazardous wastes may look the same as nonhazardous wastes. However, hazardous wastes cannot simply be put in a trash can and taken away. Hazardous wastes need to be identified, segregated, and properly disposed of to ensure their proper cradle-to-grave management.
Experienced third-party waste-management experts that specialize in emergency response and planning can partner with a plant’s leadership team to provide critical advisory services to help minimize risk. From the initial response to cleanup and ultimate closeout of all regulatory paperwork and reporting, this third-party partner can help to manage risk throughout the entire lifecycle.
When facing a large-scale event, emergency response firms can assemble a nationwide network of experts, facilities, equipment, and subcontractors. Managing hazardous wastes through an emergency response company helps manufacturers to find proper disposal outlets and enlist expert help with onsite segregation.
These waste-management companies may offer emergency services such as:
- spill containment
- unknown substance handling
- cleanup services for container leaks, fuel spills, and chemical spills
- roadside cleanup of vehicle leaks
- handling of mercury and other materials
- 24/7 emergency call center services.
Choose an emergency response provider that guarantees their personnel have the proper safety and health certifications and experience conducting regular audits and evaluations.
Because many roads and access points may be blocked during and after a disaster, an emergency response partner should be in contact with local law enforcement and emergency response teams to find out when it is safe to travel to the affected facility and begin the hazardous-waste cleanup process.
Unexpected downtime following an emergency can cost the facility several hundred thousand dollars per day. The facility’s goal is to reopen the impacted location as quickly and safely as possible to minimize the business interruption and get employees back to work. Without a pre-existing agreement in place, it may take longer for a third-party cleanup team to access and service a location after a hurricane or natural disaster, as their priority will be to contracted customers first. With that in mind, leadership teams at CPI facilities should find the best emergency response partner before or early in hurricane season, rather than waiting until the damage has been done and a potential crisis is underway.
When it comes to managing waste streams in anticipation of a potential environmental emergency, a little bit of planning goes a long way — and so does having a partner that understands the regulatory environment and how to navigate it.
Hire a backup vendor
Companies can often contract a backup emergency response partner and require that the backup vendor have specific knowledge of the established emergency contingency plan. That vendor can then assist during extreme weather events if the primary vendor cannot respond quickly due to access issues, distance from the disposal facility, overwhelming demand for services, and other factors.
In the aftermath of Hurricane Maria, which made landfall in Puerto Rico in September 2017, the overall conditions on the island were very poor — roads were damaged, power lines were down, phone coverage was scarce, clean and drinkable water was hard to come by, and basic supplies were not available. The primary objective of the emergency response partners was to remove hazardous materials such as flammable products, pharmaceuticals, and other dangerous waste streams from the island. But obstacles at the port, which was damaged and clogged with shipments waiting to be transported, made efficient entry and waste removal difficult. If the primary waste-management partner was not able to remove the waste from the island and dispose of it properly in a timely manner, the damaged plant could then turn to its backup emergency response partner for contingency intervention. The backup partner is typically located in a different area than the primary and thus may have access to alternative routes and disposal locations.
Monitor hazardous-waste inventories
Most CPI facilities have satellite accumulation areas that need to be monitored and maintained. Once a container in the satellite area is full of hazardous waste, that container is typically moved to a central accumulation area (CAA). Per the regulations spelled out in the CFR, a large-quantity generator must ship that full container within 90 days of it being moved to a CAA.
A small-quantity generator must ship the full container within 180 days. Very-small-quantity generators are not required to ship their wastes within a specific timeframe, but they cannot accumulate more than 2,200 lb of waste on-site at any given time.
Before an extreme weather event hits, create a detailed inventory of the onsite CAA — including the number of containers and the type of waste each contains. Remove these before the arrival of severe weather, if possible.
If you know in advance that severe weather is coming — which is often the case, as hurricane storm warnings are issued ten days in advance — schedule a pickup and ensure that the waste accumulated since the last shipment is taken offsite before the storm arrives.
The same caution applies to satellite accumulation areas. Before the storm comes, take inventory of all hazardous-waste streams and sources on-site, including the number and type of containers in satellite accumulation areas. Waste pickups should be scheduled in advance of the impending storm.
If the facility cannot remove all of its hazardous waste, several safety precautions should be followed to secure those materials that will remain on-site. For example, correct lids should be securely fastened on containers, and containment areas should be set up and properly cleaned. If possible, move hazardous wastes to higher-elevation storage areas and ensure that storage-containment systems, such as flammable liquid cabinets, are sufficiently anchored.
Consider unit-turnaround waste. If a facility is conducting a unit shutdown or turnaround project, the EHS team needs to know what types of waste are being generated and how they are packaged. This is important in case the material needs to be moved out of the facility before an extreme weather event occurs.
Maintain year-round compliance
Keeping up with day-to-day operations and proper waste segregation must remain a high priority for any CPI facility all year long. This includes making sure waste materials are in proper containers, in secure locations, and ultimately disposed of in a manner that meets regulatory requirements of the EPA and the U.S. Dept. of Transportation (DOT).
Waste should be kept in proper containers at all times. Improperly segregated waste streams can make an emergency response situation more difficult.
As environmental releases are a growing concern for the public, news outlets are quick to report perceived offenses made by corporations. A quick online search of “hazardous waste fines” results in hundreds of news articles reporting on offenders. In addition, the proliferation of social media allows news about regulatory fines or improper disposal of hazardous waste to spread quickly and pervasively across many channels.
Common missteps that could result in fines and brand damage include (but are not limited to):
- lack of, or improper, labeling
- open containers of hazardous waste
- dumping hazardous waste down the drain
- not having, or having inadequate, hazardous-waste manifests
- failing to properly train employees in hazardous-waste management, handling, and emergency preparedness
- failing to comply with regulations pertaining to hazardous-waste generation
- not having appropriate hazardous-waste determinations on file.
The average cost to develop and maintain a proactive environmental-compliance program for hazardous waste varies. However, with millions of dollars in potential fines a possibility for noncompliant practices, and brand reputation and consumer loyalty at stake, organizations must be well informed about changes from the EPA and update their hazardous-waste management programs to keep up with evolving regulations.
Most importantly, to remain compliant in an ever-changing regulatory environment, partnering with a trusted and experienced waste-management company is recommended. Working closely with one dedicated and knowledgeable partner for both emergencies and day-to-day operation ensures continuity and communication. These partners service thousands of generators and deal with thousands of tons of waste a year. They can provide a variety of services, including transformation and disposal of hazardous waste year-round.
Additionally, such dedicated waste-management companies often provide services related to:
- thermal treatment
- fuels blending
- incineration
- waste-to-energy conversion of nonhazardous waste
- recycling
- water treatment
- chemical treatment
- landfill disposal of both hazardous and nonhazardous waste.
Such services also require special types of equipment. Accordingly, these specialized companies can provide equipment such as:
- tractor trailers, trucks, and vans that can handle a variety of containers, such as 55-gal drums, 275-gal intermediate bulk containers (IBCs), etc.
- bulk tankers for liquids, such as vacuum tankers or straight tankers
- bulk roll-off and vacuum boxes for solids and sludge
- tank-cleaning equipment
- dedicated personnel to manage onsite projects.
Any organization, particularly those that produce chemicals, byproducts, and waste streams, must face the simultaneous challenges of managing their hazardous-waste streams, maintaining and ensuring regulatory compliance, and minimizing environmental impact during and after a natural disaster. It is especially important to address these challenges in the face of increasing consumer focus on environmental responsibility.
Closing thoughts
Chemical waste services, from routine waste pickups to large-scale disaster response, must be handled with the utmost professionalism and attention to detail. In addition to being expensive, any industrial waste regulatory violation or oversight — especially in the case of a natural disaster — has the potential to seriously impact employees, the public, and the environment.
In the aftermath of a natural disaster, waste and environmental concerns are only part of a larger, complicated picture. Every emergency situation must be managed with a commitment to safety and full compliance, and this becomes even more important when hazardous-waste streams are involved. When disaster strikes, follow all applicable regulations from beginning to end.
Literature Cited
- National Oceanic and Atmospheric Administration, “Fast Facts: Hurricane Costs,” NOAA, Washington, DC, https://coast.noaa.gov/states/fast-facts/hurricane-costs.html (May 2019).
- Dapene, K., “Rising Costs of Hurricanes,” The Wall Street Journal,www.wsj.com/articles/the-rising-costs-of-hurricanes-1538222400 (accessed Sept. 29, 2018).
- National Oceanic and Atmospheric Administration, “NOAA Predicts Near-Normal Atlantic Hurricane Season,” NOAA, Washington, DC, www.noaa.gov/media-release/noaa-predicts-near-normal-2019-atlantic-hurricane-season (accessed May 23, 2019).
- U.S. Environmental Protection Agency, “Learn the Basics of Hazardous Waste,” EPA, Washington, DC, www.epa.gov/hw/learn-basics-hazardous-waste (accessed April 26, 2019).
- U.S. Environmental Protection Agency, “Summary of the Resource Conservation and Recovery Act,” EPA, Washington, DC, www.epa.gov/laws-regulations/summary-resource-conservation-and-recovery-act (accessed Aug. 15, 2019).
- U.S. Environmental Protection Agency, “Resource Conservation and Recovery Act (RCRA) Laws and Regulations,” EPA, Washington, DC, www.epa.gov/rcra (accessed Feb. 12, 2019).
- U.S. Environmental Protection Agency, “Categories of Hazardous Waste Generators,” EPA, Washington, DC, www.epa.gov/hwgenerators/categories-hazardous-waste-generators (accessed Mar. 25, 2019).
- “Identification and Listing of Hazardous Waste,” 40 CFR Section 261, Washington, DC (accessed June 20, 2019).
- U.S. Environmental Protection Agency, “Defining Hazardous Waste: Listed, Characteristic and Mixed Radiological Wastes,” EPA, Washington, D.C., www.epa.gov/hw/defining-hazardous-waste-listed-characteristic-and-mixed-radiological-wastes#FandK (accessed Mar. 25, 2019).
- U.S. Environmental Protection Agency, “Quantity of RCRA Hazardous Waste Generated and Managed,” EPA, Washington, DC, https://cfpub.epa.gov/roe/indicator.cfm?i=54#3 (accessed June 26, 2018).
- U.S. Environmental Protection Agency, “Links to Hazardous Waste Program and U.S. State Environmental Agencies,” EPA, Washington, DC, www.epa.gov/hwgenerators/links-hazardous-waste-programs-and-us-state-environmental-agencies (accessed Mar. 26, 2019).
- Fowler, T., “Texas Chemical Plant Braces for Explosions, Fires After Hurricane Harvey as ‘Noxious’ Smoke Rises,” ABC News, https://abcnews.go.com/US/texas-chemical-plant-braces-explosions-fires-hurricane-harvey/story?id=49521170 (accessed Aug. 31, 2017).
- Reuters, “Police and EMTs are Suing Arkema Over the Chemical Plant Fire After Hurricane Harvey,” Business Insider, www.businessinsider.com/r-update-1-police-and-emts-sue-arkema-over-chemical-plant-fire-after-harvey-2017-9 (accessed Sept. 7, 2017).
Copyright Permissions
Would you like to reuse content from CEP Magazine? It’s easy to request permission to reuse content. Simply click here to connect instantly to licensing services, where you can choose from a list of options regarding how you would like to reuse the desired content and complete the transaction.