Evolving market requirements have increased the need for automation vendors to build process automation solutions that are more flexible, interoperable, open, and future-proof.
Automation technology is evolving in response to today’s market demands, broadening the possibilities for chemical producers to optimize process efficiency with smarter, more agile operations and reduced maintenance needs. Distributed control system (DCS) vendors are taking advantage of the latest technology trends and open standards to boost plant performance and sustainability without diluting the core DCS qualities of reliability, availability, safety, and security.
Since their debut over 40 years ago, DCSs — also widely referred to as decentralized control systems — have played a starring role in orchestrating many of the complex industrial processes that our society is dependent on. DCSs oversee safer, more dependable, and more efficient operations in thousands of industrial facilities worldwide, spanning chemicals, pharmaceuticals, and oil and gas to metals, minerals, water treatment, food and beverage, pulp and paper, and more (Figure 1).
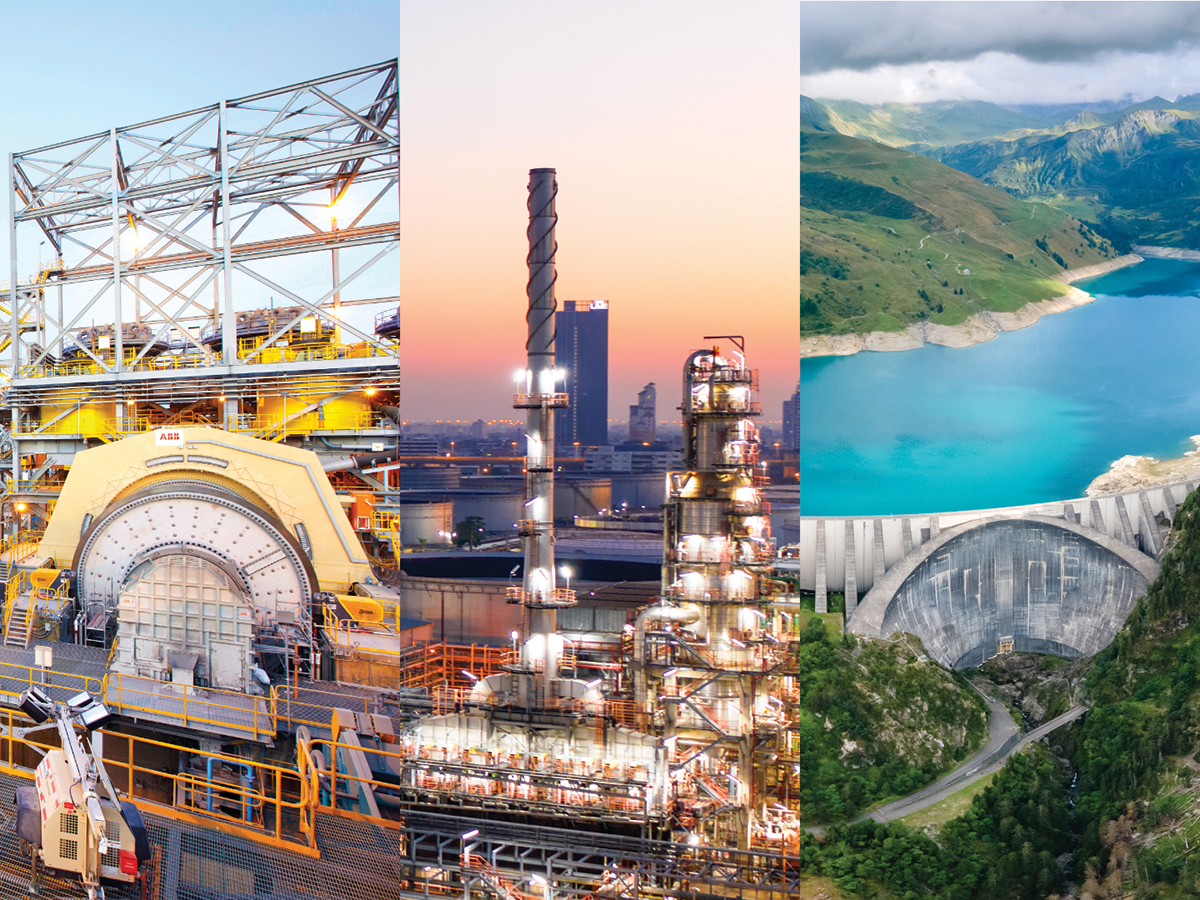
▲Figure 1. For over 40 years, distributed control systems (DCSs) have helped run important industrial processes that we rely on every day. They make processes safer, more reliable, and more efficient in industries like chemicals, oil and gas, food production, and even water treatment.
The success of DCSs has grown from their ability to manage and solve the challenges commonly encountered in large-scale industrial operations. Foremost amongst these is managing the complexity of processes that handle multiple variables and equipment spread across wide geographical areas. By distributing control functions across multiple controllers, they enable localized control of different sections of the plant, ensuring that each process area operates efficiently and can respond to changes or anomalies without overwhelming a central system.
Another challenge is improving system reliability and minimizing downtime. Using multiple controllers provides effective redundancy in the event of a problem, avoiding the risk of shutdowns or incidents caused by the knock-on impact of a failed controller or subsystem affecting the rest of the system. The availability of real-time diagnostics also assists with troubleshooting, enabling problems to be pinpointed and rectified before they can escalate without disrupting the whole system.
The ability to meet future demands is also becoming increasingly important as companies face growing pressure to adapt to rising energy costs, new regulations, and shifting customer trends. DCSs facilitate this by making it easier to add new equipment or expand the system as the plant grows, avoiding the need for the significant redesigns and disruptions associated with updating centralized control systems. Futureproofing is further enhanced by the ability to create customized control strategies tailored to the specific needs of each section of the plant, increasing operational flexibility...
Would you like to access the complete CEP Article?
No problem. You just have to complete the following steps.
You have completed 0 of 2 steps.
-
Log in
You must be logged in to view this content. Log in now.
-
AIChE Membership
You must be an AIChE member to view this article. Join now.
Copyright Permissions
Would you like to reuse content from CEP Magazine? It’s easy to request permission to reuse content. Simply click here to connect instantly to licensing services, where you can choose from a list of options regarding how you would like to reuse the desired content and complete the transaction.